Controllers MELSEC-QS/WS Series Safety Programmable Controller (Out of production)
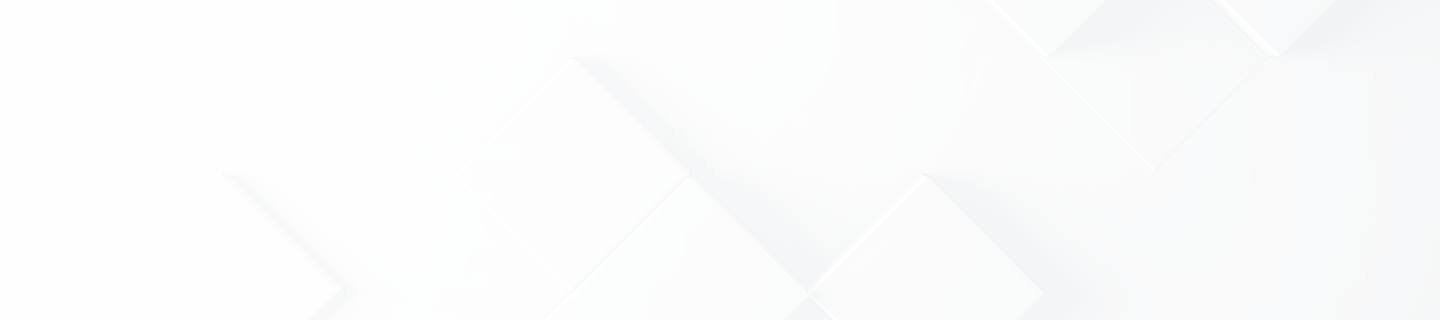
The safety programmable controller is compliant with international safety standards, EN ISO 13849-1 Category 4/PL e and IEC 61508 SIL 3. It is ideal for medium- to large-scale safety control systems. Ladder programs and certified safety function blocks*1 realize flexible programming.
*1.They can be used to structure EN ISO 13849-1 Category 4/PL e and IEC 61508 SIL 3 safety applications.
This Series has been discontinued in September 2023.
Lineup
Product name | Model |
---|---|
Safety CPU* | QS001CPU (-K) |
Safety main base* | QS034B (-K) |
Safety power supply* | QS061P-A1 (-K) |
QS061P-A2 (-K) | |
CC-Link IE Field Network master/local (with Safety Communication Functions) | QS0J71GF11-T2 |
CC-Link Safety system master* | QS0J61BT12 (-K) |
CC-Link Safety system remote I/O | QS0J65BTB2-12DT (-K)* |
QS0J65BTS2-8D | |
QS0J65BTS2-4T |
*S-mark compatible part models are indicated in parentheses.