Option Force sensor set
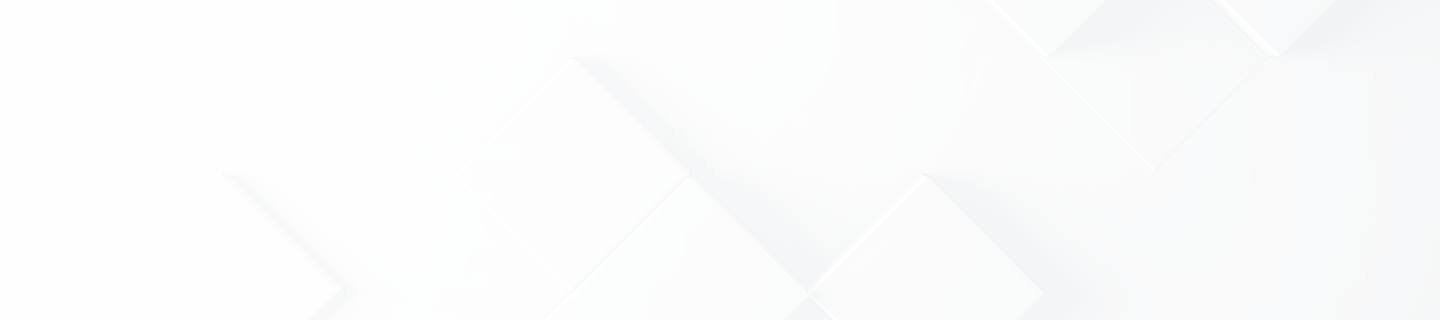
Introduction
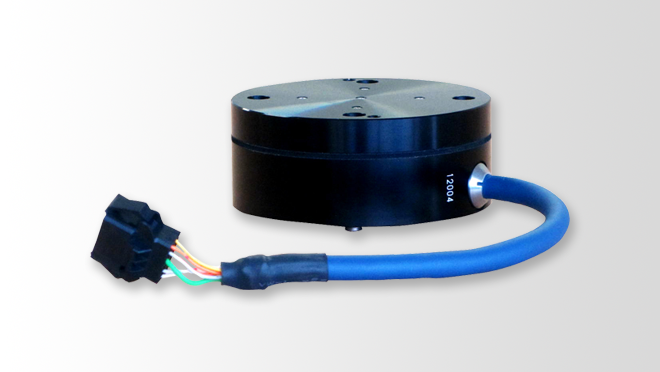
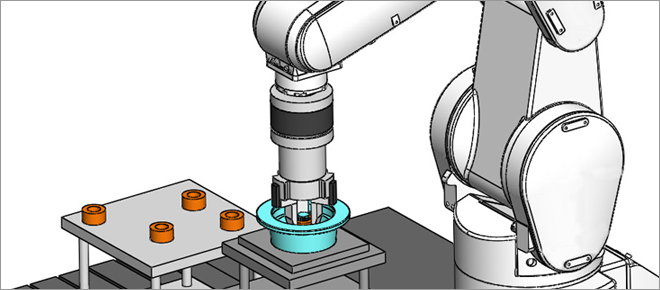
Assembly/processing tasks are performed in the same manner as a human being, while sensing the force that is applied to the gripper.
- Controls the robot so that it moves delicately along the contours of a workpiece.
- Operates with a constant force in a direction specified by the user.
- Changes the delicacy level for the robot movement and the conditions of contact detection during operation.
- Obtains the position and force data at the time of contact.
Please refer to the Catalog for details.
Features
Improved production stability
- Controls “force” and “flexibility”. Modifies control properties during operation.
- Keeps the force constant so that the workpiece can be handled without causing damage.
- Quality can be managed using log data, and the causes of work errors can be analyzed.
Realization of complex assembly and processing tasks
- Switches operation in response to transitional states.
- Complex assembly tasks achieved through techniques such as phase matching.
Easy control and Simple operations
- Based on examples of programs, programs can be easily created using dedicated robot language.
- The robot can be quickly [taught] accurate positions based on position and force data from the teaching box. Work conditions can be verified and adjusted by viewing the position, force data and the graph waveform.
MELFA Smart Plus
Enhancement function for force sense control
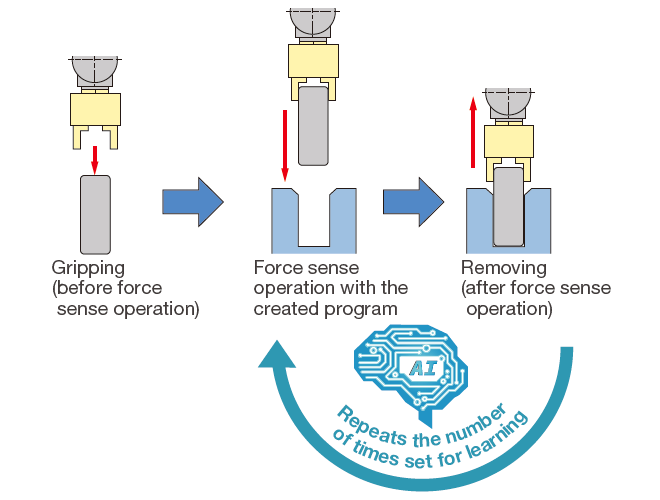
AI optimizes control parameters, positions and speed!
AI automatically adjusts to the optimum parameters for force sensing.
The optimum parameter calculation function allows anyone to easily adjust to the optimum parameters in a short time.This allows shorter system startup and tact time.
(*Supported Robots: FR series, CR series)
Function examples
Introduction of some of the functions.
Basic functions
Force control
Controls “force” and “flexibility”. Modifies control properties during operation.
Keeps the force constant so that the workpiece can be handled without causing damage.
Force detection
Switches operation in response to transitional states.
Complex assembly tasks achieved through techniques such as phase matching.
Force log
Checks the work status to facilitate adjustment. Log data analysis also allows predictive safety measures.
Gravity Offset Cancel Function
Compensates for gravity in response to changes in force on the force sensor in the X, Y and Z directions when the attitude changes. Force control can be exercised correctly even when the attitude changes.
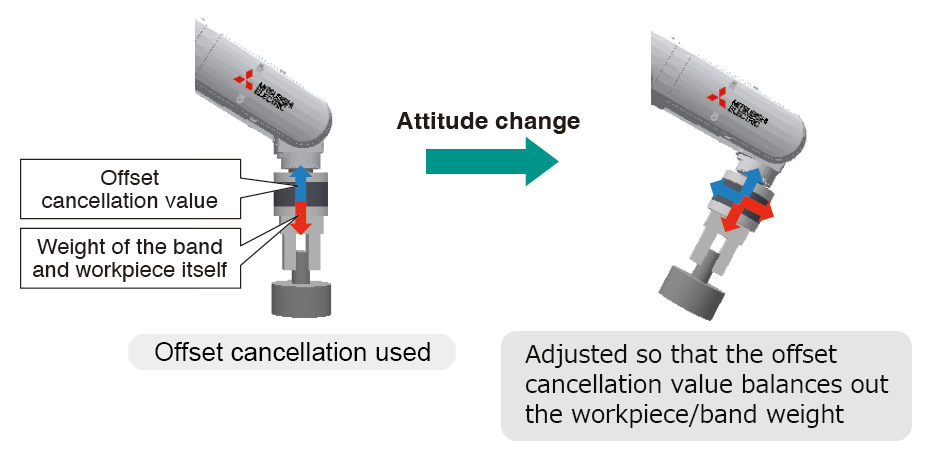
Teaching work assistance
Force GUI included(*1)
(*1:Graphical User Interface)
- Computer software (RT ToolBox3) and a teaching box (R86TB or R32TB) are standard features of the force GUI screen, making it easy to use force sensors.
- Teaching can be carried out while monitoring the reactive force on the force GUI screen.
- Settings of safety logic, monitoring of signals, variables, and load conditions, and more features can be utilized with just this one teaching box.
- Force data synchronized to the positional data can be saved as log data.
- Log data can be viewed as graphs using RT ToolBox. Also, log data files can be downloaded to a computer via FTP.
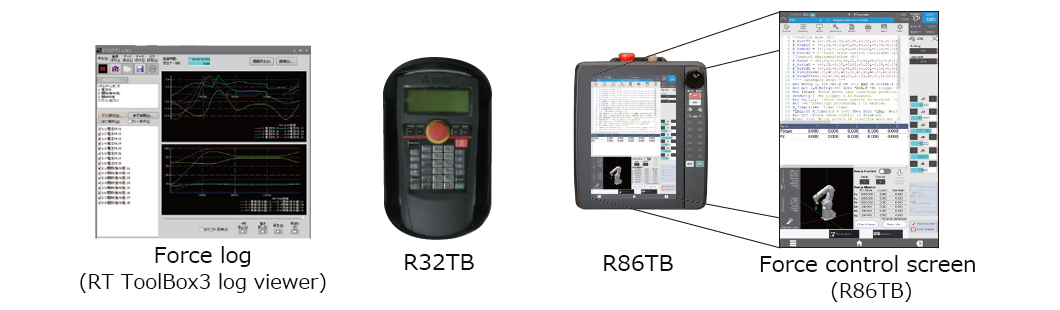
Related Catalog
Please refer to the Related Catalogs.