Administering real-time wide visualization in the new normal
First released September, 2022
“We were able to eliminate numerous devices and reduced operational costs by about ¥1 million annually.”
Ryohei Kitada, Environment Promotion Section, Nagoya Works
MITSUBISHI ELECTRIC NAGOYA WORKS- Manufacturing, Japan -
Administering real-time plant-wide visualization in the new normal
Mitsubishi Electric’s GENESIS64™ SCADA software is a visualization solution for the process, infrastructure and manufacturing industries. The software is deployed at the Nagoya Works to administer energy infrastructure throughout the entire plant. GENESIS64™ systematically monitors the operating conditions and loads on equipment in real-time whilst being able to be accessed remotely, addressing the issues of the “new normal”.
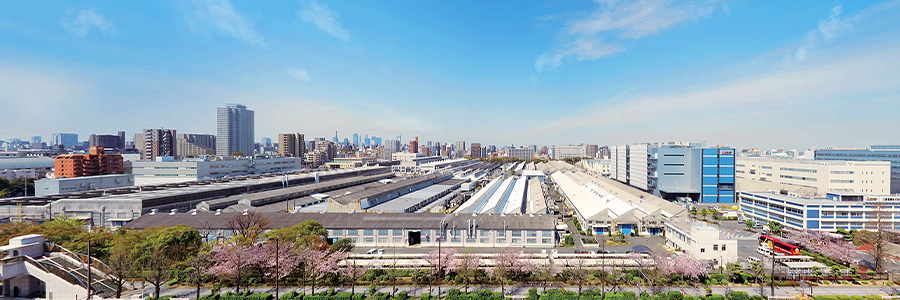
Key Points:
- 1.Developed from administering infrastructure equipment one piece of at a time to monitoring entire works
- 2.Creates real-time visualization of the operating status of electrical substations, boilers, etc.
- 3.Makes it possible to administer and operate infrastructure from anywhere thanks to remote access capabilities
Mitsubishi Electric Nagoya Works
The Nagoya Works is the linchpin of Mitsubishi Electric’s factory automation business. There are teams of diverse employees involved with factory automation who work at this vast facility that is home to over thirty buildings dedicated to production, administration and social service facilities. Significant infrastructure has been built to supply electricity, air, and power for steam to all parts of the works.
Regularly checking the infrastructure operational status and its load factors is crucial to provide stable power that is indispensable to production. At the Environment Promotion Section of the Manufacturing Systems Division that administers the infrastructure equipment at the Nagoya Works, they do more than just perform regular maintenance and repairs on equipment. They also monitor the infrastructure operational status and undertake precaution measures that will prevent any major problems from occurring such as production stoppages due to supply deficiencies or breakdowns caused by overloads.
To that end, they must patrol the buildings and facilities collecting operational information from individual monitoring systems for substations and steam boilers. However, these monitoring systems are all independent from one another, creating a lengthy process. To gather information from individual monitoring systems and assess the load conditions on the wiring and piping that links the equipment together, they had to collate and analyze the statuses of the equipment. This took more than just man-hours. According to Ryohei Kitada from the Environment Promotion Section of the Nagoya Works, “Given that we also needed to do things like update our administration of the system map, we also needed the skills to assess current conditions from the revised map and this task was up to individuals. When coming up with new arrangements for the equipment, we would also have to do a cross-sectional study of the power-supply capacity of the current infrastructure, and we believed it was necessary to come up with a method for administering the infrastructure throughout the entire works in a unified way rather than just monitor individual pieces of equipment.”
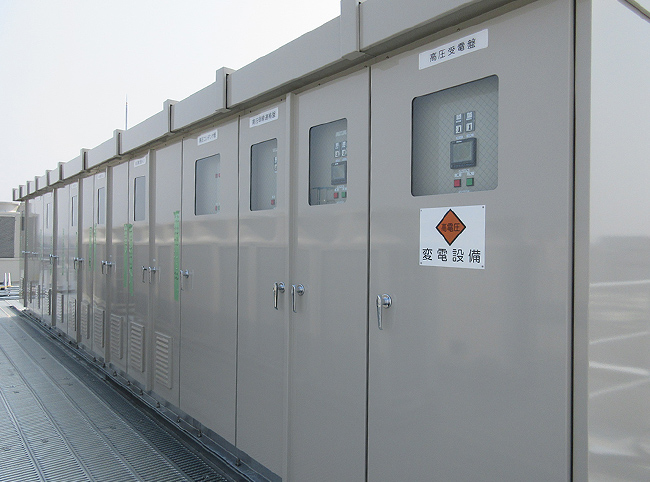
Numerous high-voltage transformers are installed right across the Nagoya Works and must be monitored in a unified fashion. presented in an easy-to-understand graphic.
GENESIS64™ realizes the goal of creating a unified visualization, making it the optimal solution for addressing these concerns. To corroborate this, it was decided to use the infrastructure equipment at the Nagoya Works and review the results.
Creates visualizations every 10 seconds of equipment operations throughout the plant
Most of the energy monitoring systems for each building use Programmable Logic Controllers (PLCs). Each of those PLCs are connected to LAN networks. The information is collected on an OPC UA server, and then a visualization of that information is created through GENESIS64™ software.
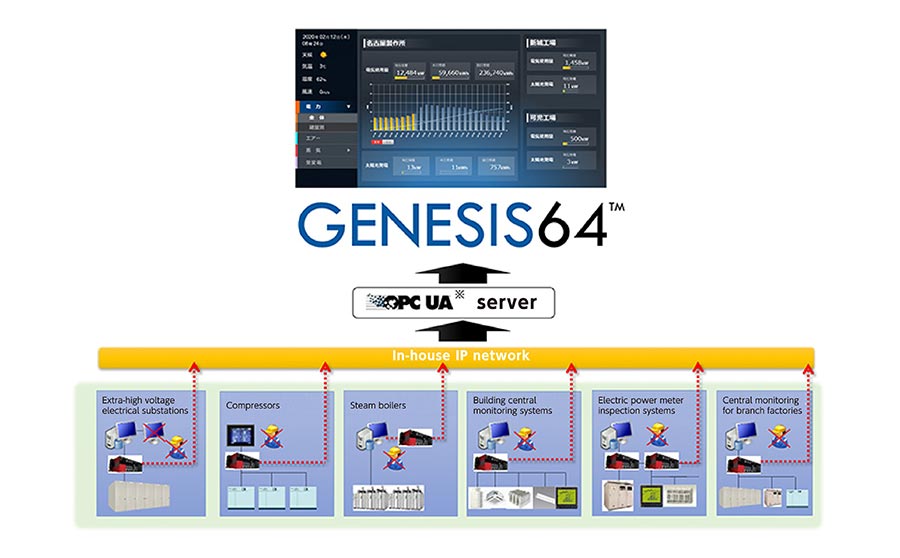
Monitoring the energy infrastructure throughout the Nagoya Works using GENESIS64™. The monitoring systems for every building and piece of equipment, including those at two branch factories, are connected to the works-wide LAN. The GENESIS64™ then creates visualizations based on the data collected.
* A trademark of the OPC Foundation.
The goal of unified monitoring of energy infrastructure throughout the entire works was efficiently accomplished. The power use for every building and equipment operating status is displayed on GENESIS64™ with update intervals as little as 10-seconds. Information about multiple pieces of equipment can also be reviewed systematically on a single screen. Kitada says, “Previously, we would have had to take down the figures from multiple monitoring systems and then put it into the system map we had at hand to check. Now, it has become possible to get all of that data in real time on a screen.”
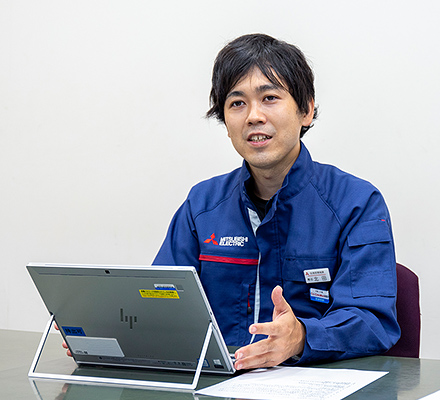
Ryohei Kitada of the Environment Promotion Section, Nagoya Works
Another benefit of monitoring infrastructure with GENESIS64™ is that the operating conditions of infrastructure equipment can be seen in near real-time, making it possible to react quickly on any equipment malfunctions. The equipment status can now be quickly understood without having to patrol the facility, which reduces downtime and improves productivity.
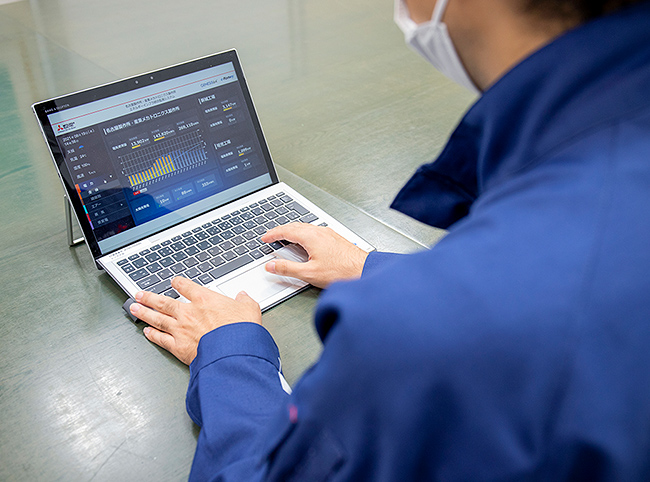
Because GENESIS64™ works online, it can be viewed on any internet browser-capable device whether it be a PC, a tablet, or smartphone.
At the Nagoya Works, the system was introduced without having to implement any major changes. This is because the monitoring systems for all the equipment were made with PLCs. They are connected to the Works’ network through an Ethernet module which communicates through the LAN to the equipment. “Only the steam boilers didn’t have PLCs, as they used monitoring systems that were unique to their manufacturers. However, if you connect PLCs to those monitoring systems, we can then monitor them with GENESIS64™ through Ethernet and the OPC UA server,” explains Kitada. The OPC UA is the industry-standard interface for linking the networks on manufacturing sites with information networks. The advantage of this system is the degree of freedom it offers – so long as a piece of equipment is OPC UA-compatible it can come from any manufacturer.
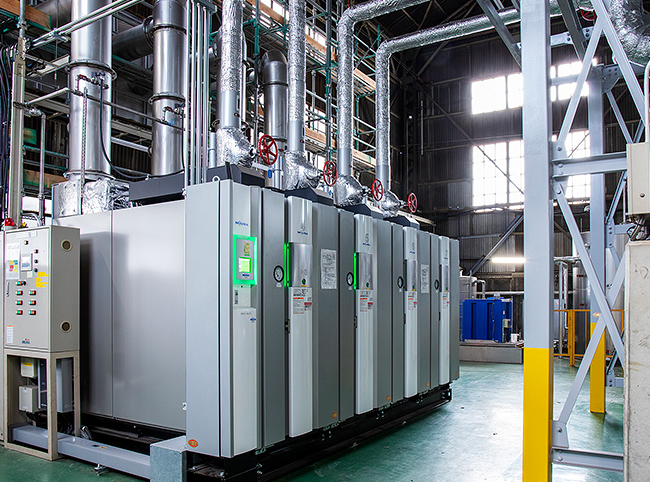
A steam boiler at the Nagoya Works. Manufacturer’s dedicated monitoring system was required, but connecting a PLC made it possible to easily collect the data.
A benefit of having implemented this system is that it was possible to simplify the monitoring systems specific to each device as it was possible to monitor all of them at the Environment Promotion Section. In particular, says Kitada, “The extra-high voltage electrical substations had been outfitted with multiple dedicated monitoring terminals and monitoring panels, but thanks to unified monitoring through the GENESIS64™ we were able to eliminate numerous devices and reduced operational costs by about ¥1 million annually.”
Agile shift to remote working
Use of GENESIS64™ to monitor the energy infrastructure of the entire Works began in 2020, yielding an unexpected benefit. With people being encouraged to work remotely due to the spread of Covid-19, use of GENESIS64™ enabled Kitada and his colleagues responsible for administering the infrastructure equipment to shift to remote working right from the start.
Whilst it had already been possible at the Environment Promotion Section to administer the equipment remotely, it was limited to some of the monitoring systems connected to the network. Due to security concerns, monitoring systems capable of controlling infrastructure equipment were not connected to the network. However, infrastructure monitoring with GENESIS64™ displays the data collected from PLCs connected to the LAN on an internet browser and does not have any control capabilities, therefor there is no need to login to a PC-based monitoring system. “If you just have something like a VPN to connect to the LAN from offsite, you can safely do the work of administering infrastructure equipment even remotely. When we implemented GENESIS64™, we didn’t think that remote working would be this important. Consequently, I really feel glad that we did so,” says Kitada.
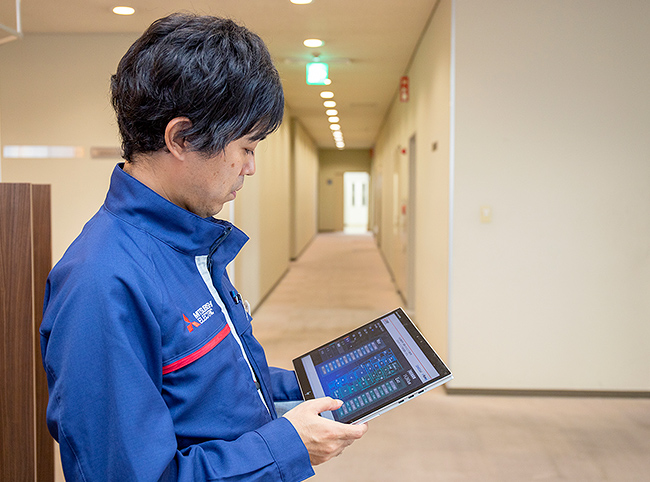
Thanks to the ease with which the system can be used remotely, they were able to quickly respond to the calls to shift to remote work due to the Covid-19 pandemic.
More than just being useful for working remotely from home, the system also enabled checking the status of infrastructure equipment at the Nagoya Works’ two branch facilities, the Kani Factory (Kani City, Gifu Prefecture) and the Shinshiro Factory (Shinshiro City, Aichi Prefecture). Furthermore, Kitada says, “When we used remote desktop computers only one person could access the systems at a time, but with GENESIS64™ presenting the information through an internet browser it’s now possible for multiple people to view the information simultaneously. It also made it possible for me to access the system at the same time as junior staffers and then instruct them on their duties and how to deal with things as we view the same data.”
“There are abundant examples of GENESIS64™ being introduced to monitor not only production lines but also the utilities and infrastructure equipment at a factory,” says Ikuto Matsuyuki from the Sales Department’s Software Section. “With this case, we were able to build and operate a system that made the most of GENESIS64™’s strengths, such as being able to administer and analyze information from a variety of systems and equipment in a unified fashion, and engage flexibly in remote monitoring, and so forth. In due course, we were able to verify its impact. Down the road, we want it to be able to administer energy usage in an even more detailed manner. More than that, we also want to expand the things it can monitor to include administering how much energy is being used for air-conditioning and lighting. Our goal is to establish it as the solution for a manufacturing industry that is seeking to become carbon neutral.”
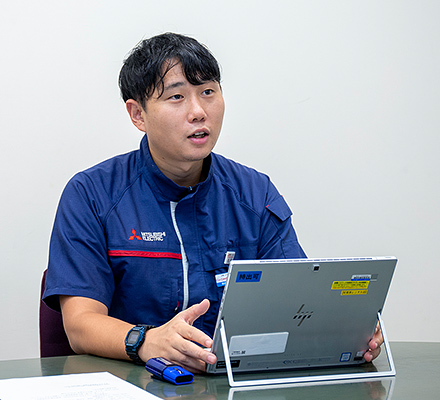
Ikuto Matsuyuki, Software Section, Sales Department, Nagoya Works