Keeping cool pays dividends
First released September, 2022
“With GENESIS64™ we were able to specifically verify the effects and established the night-purge as a new measure against the heat.”
Fumitaka Yamada, Environmental Promotion Section, Nakatsugawa Works.
MITSUBISHI ELECTRIC NAKATSUGAWA WORKS- Manufacturing, Japan -
SCADA software GENESIS64™ helps control high temperatures on-site Improvements made with cause analysis and ventilation fan control
The Mitsubishi Electric Nakatsugawa Works uses GENESIS64™ SCADA software to control ventilation fans and prevent high temperatures at production sites. Not only does the GENESIS64™ continuously monitor on-site temperatures to expose the factors that cause high temperatures, but it also controls ventilation fans with temperature data obtained in real-time. This means that even on sites with extremely high temperatures, efficient environmental improvements can be made without having to rely solely on extra equipment, such as air conditioners, which requires added investment.
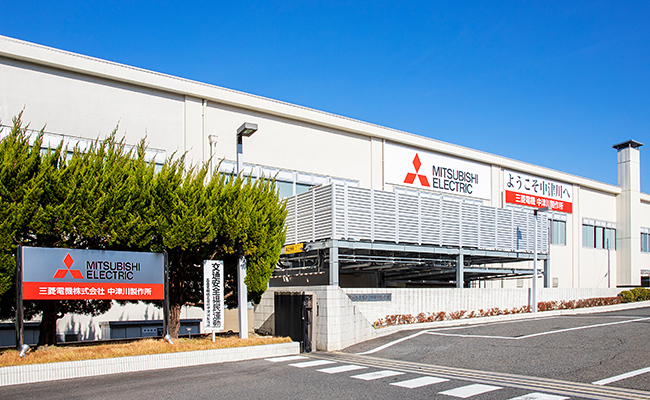
Key Points:
- 1.Examines the causes of temperature change at production sites
- 2.Controls ventilation fans based on visualized temperature data
- 3.Temperature improvements made clear in numbers, leading to better understanding of the production site
Mitsubishi Electric Nakatsugawa Works
Mitsubishi Electric Nakatsugawa Works in Nakatsugawa City, Gifu Prefecture is a facility that develops and manufactures air-related equipment such as ventilation fans, the Lossnay (full heat exchange ventilator), and Jet Towel hand dryers. These first two products can be used in a wide variety of settings as ventilation not only for homes, but also for industrial use in manufacturing plants and factories. The Daiichi Factory, the main plant at Nakatsugawa Works, produces industrial ventilators such as pressure ventilation fans and air transfer fans.
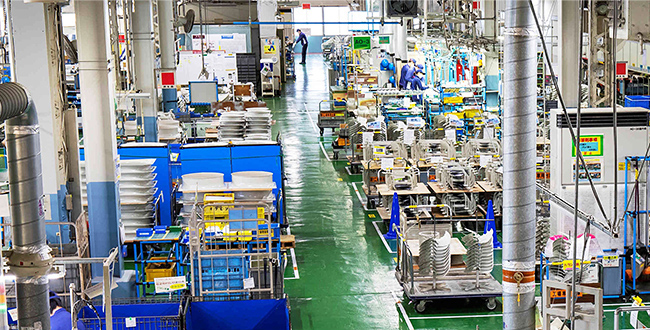
The Daiichi Factory at the Mitsubishi Electric Nakatsugawa Works which manufactures pressure ventilation fans and air transfer fans.
High temperatures have long been a problem on the production floor at the Daiichi Factory. Due to the heat generated by the drying process used in painting the blades of the ventilation fans, on-site temperatures can exceed 30 degrees Celsius in the summer. “High temperatures can affect not only work efficiency and worker motivation, but can also impact safety,” explains Takayoshi Suzuki, machining subsection chief, Ventilator Manufacturing Department.
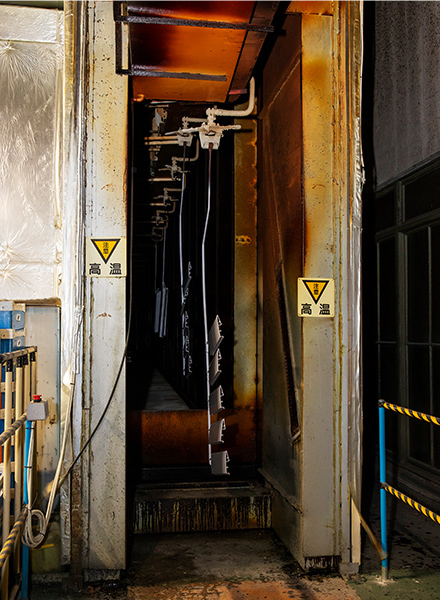
The drying process after painting. Heat from the gas furnace used for drying is a major cause of high temperatures at the site.
Since 2017, efforts have been made to release excess heat, including introducing an exhaust system and installing spot coolers. Due to the Covid-19 pandemic, workers had to wear masks, which had compounded the issue and so more robust measures were required. Visualization of the on-site environment and control of ventilation fans using GENESIS 64™ SCADA software solved this problem.
Night-purge effects tested and implemented
“We had been looking at how to improve the workplace environment by installing thermometers in various places around the factory, but we could only see changes in room temperature over time at certain places. We couldn’t get a picture of overall heat distribution. So, we decided to install 30 heat sensors in various places, aggregating them all into a sensor via the master unit (wirelessly), and visualizing the data with the GENESIS64™,” says Fumitaka Yamada of the Environmental Promotion Section, Manufacturing Control Department. Since the ventilation fans in the factory are also connected to a Programmable Logic Controller (PLC), they can be operated and controlled with the GENESIS64™.
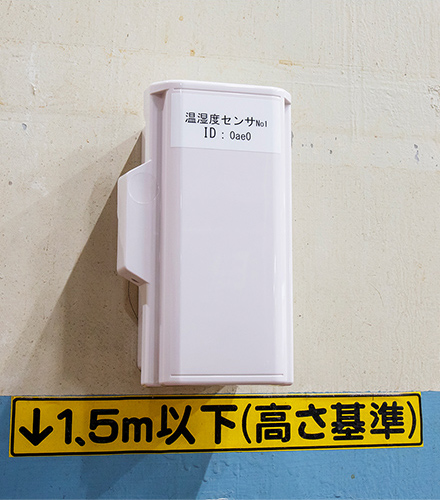
30 heat sensors have been installed in the Daiichi Factory.
Data is sent to the PLC over a wireless network.
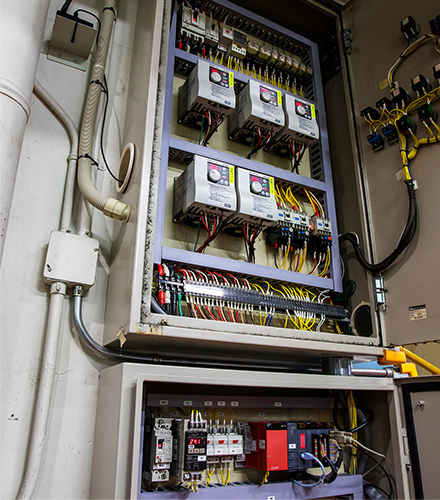
Data from the heat sensors is received wirelessly by the master unit (top left) and aggregated in the PLC (below).
Temperature monitoring with the GENESIS64™ revealed that external factors played a surprisingly large role. “Since a lot of heat is produced from the painting equipment in the drying process, we were convinced that whether the drying process was in operation or not had a predominant effect on the temperature of the whole production site. However, when analyzing temperature data collected by the GENESIS64™ over several months, we found out that the heat which had built up in the building from all the sunshine and from the equipment in use the previous day had a huge impact on site temperature the next day,” explains Shota Komori of the Development Planning Section, Ventilator Manufacturing Department.
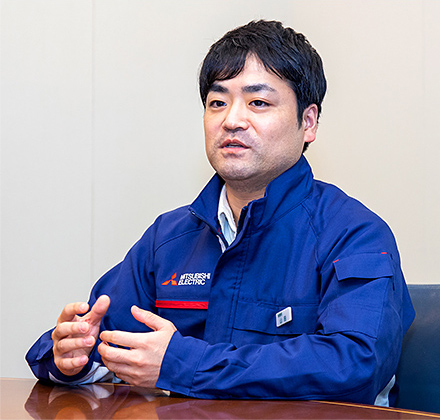
Fumitaka Yamada of the Environmental Promotion Section, Manufacturing Control Department, Nakatsugawa Works.
Due to the cumulative effects of the drying process and the heat accumulated in the whole building causing continuous high temperatures, Komori and his team, working on measures to combat this issue, decided to review how the ventilation fans operated. In particular, how to utilize the cold outside night air to directly cool the heat accumulated in the building to lower the next-day room temperatures by using a night-purge*, as well as operating ventilation fans close to the drying process (another source of heat) for daytime vents. “We’d had the night-purge idea, of using the outside air at night, for a long time, but it was difficult for us to verify its effects, so we never implemented it. But with the GENESIS64™ we were able to specifically verify the effects and so we established the night-purge as a new measure against the heat,” says Yamada.
* A method of taking in cooler outside air at night to cool inside areas for the next day
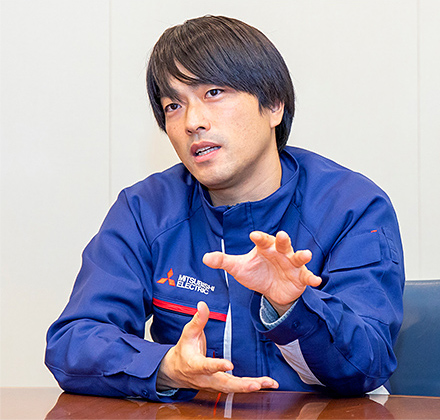
Shota Komori of the Development Planning Section, Ventilator Manufacturing Department, Nakatsugawa Works.
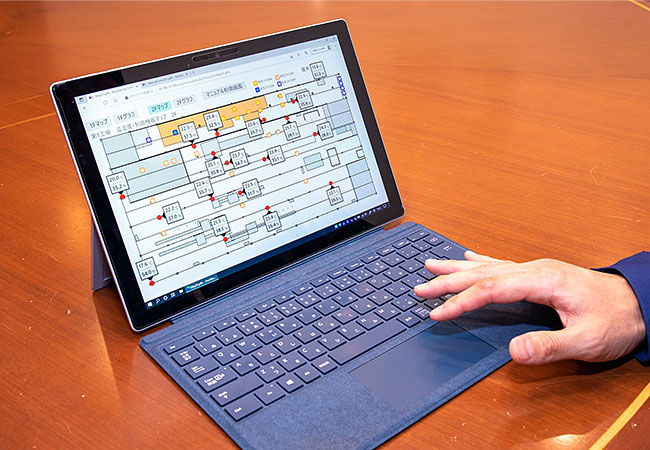
High temperatures can be avoided by understanding temperatures at the production site in real-time with the GENESIS64™ and properly controlling ventilation fans.
As well as ventilation technologies for various products being developed at the Nakatsugawa Works, airflow consultation takes place here with the aim of improving indoor environments for client companies. Based on this expertise, analysis is done on what kind of airflow should be created in the Daiichi Factory to release heat build-up in the whole building. By moving individual ventilation fans accordingly and not moving those that do not need to be moved, we have created a system that can seek energy savings while improving measures taken against high temperatures.
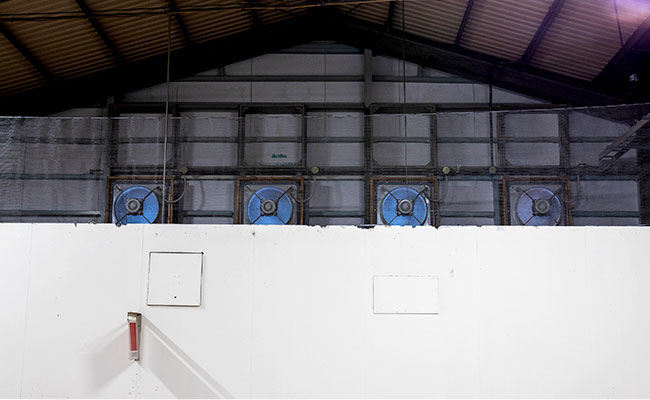
Ventilation fans in the Daiichi Factory are lined up on the back wall. Power to these fans can be controlled from the GENESIS64™ screen.
The effect of 3 air conditioners
One of the considerable benefits of using GENESIS64™ to visualize the on-site environment and controlling the ventilation fans, is that there is less need for additional investment in air conditioners. “At first, we were thinking to add air conditioners as a way to counteract high temperatures. According to the results from our airflow analysis, if three additional 10-horsepower air conditioners were installed, the temperature inside the factory would fall by about 0.7 degrees on average across the entire floor. But by using GENESIS64™ to visualize the on-site environment, we found that the same effect can be obtained by doing a night-purge. Night purging requires the installation of pressure ventilation fans for air supply, but they are cheaper than air conditioners so less investment is needed,” says Komori.
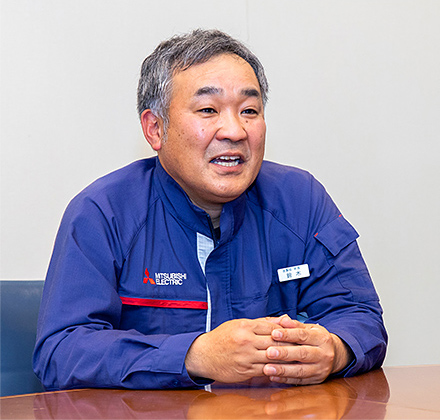
Takayoshi Suzuki, machining subsection chief, Ventilator Manufacturing Department, Nakatsugawa Works.
People on-site have been able to work with greater peace of mind as measures against high temperatures have begun to improve. “We had been working on ways to reduce high temperatures on-site through various improvement activities, but the effects were not quantitatively understood. Improvements made with the GENESIS64™ however, show the effects in concrete numbers, so people on-site can see how the factory is taking measures to combat high temperatures,” says Suzuki.
Plans are being made to further install pressure ventilation fans and air transfer fans at the Daiichi Factory based on factory temperature distribution visualized with GENESIS64™. After this successful implementation, the plan is to expand the scope of monitoring with GENESIS64™ to the installed equipment to promote further energy-savings at the same time as combating high temperatures.
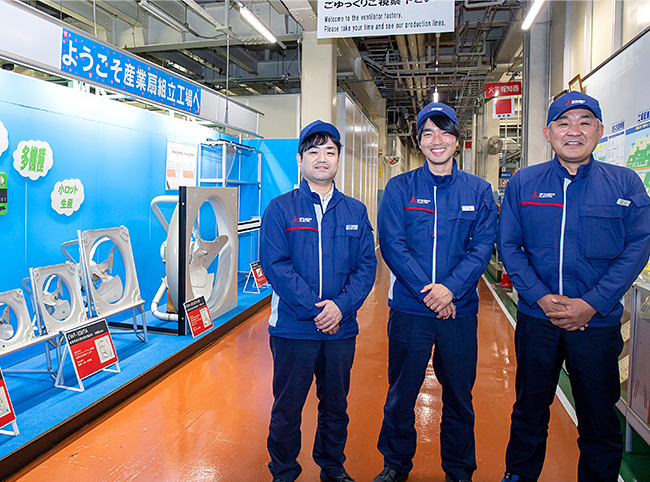