Inverters-FREQROL-E Series -FREQROL-E800- Higher added values
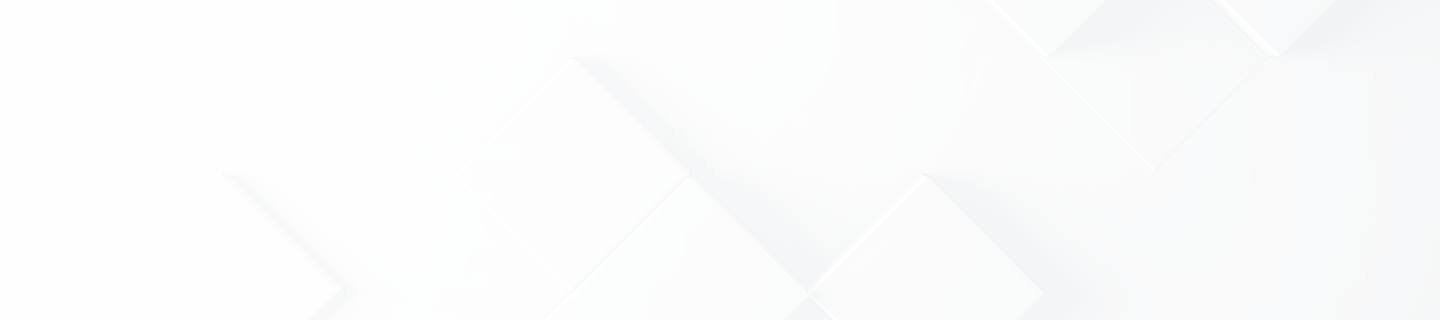
Higher added values
The outstanding drive performance and various functions create higher added values.
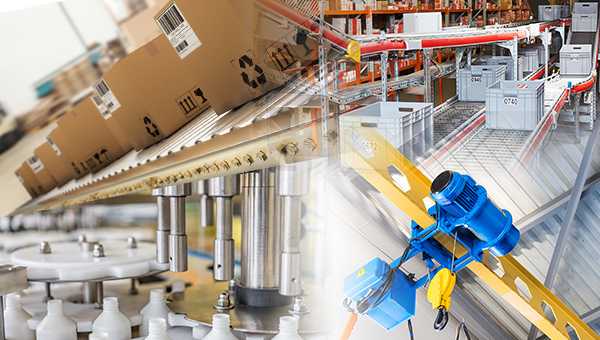
Customizing inverter operation for each machine E800E800-EE800-SCE
PLC function
In accordance with the machine specifications, users can set various operation patterns: inverter movements at signal inputs, signal outputs at particular inverter statuses, and monitor outputs, etc. Operation of the system can be customized by the inverter alone.
Parameters and setting frequency can be changed at the program. Control programs can be created in sequence ladders using the inverter setup software (FR Configurator2).
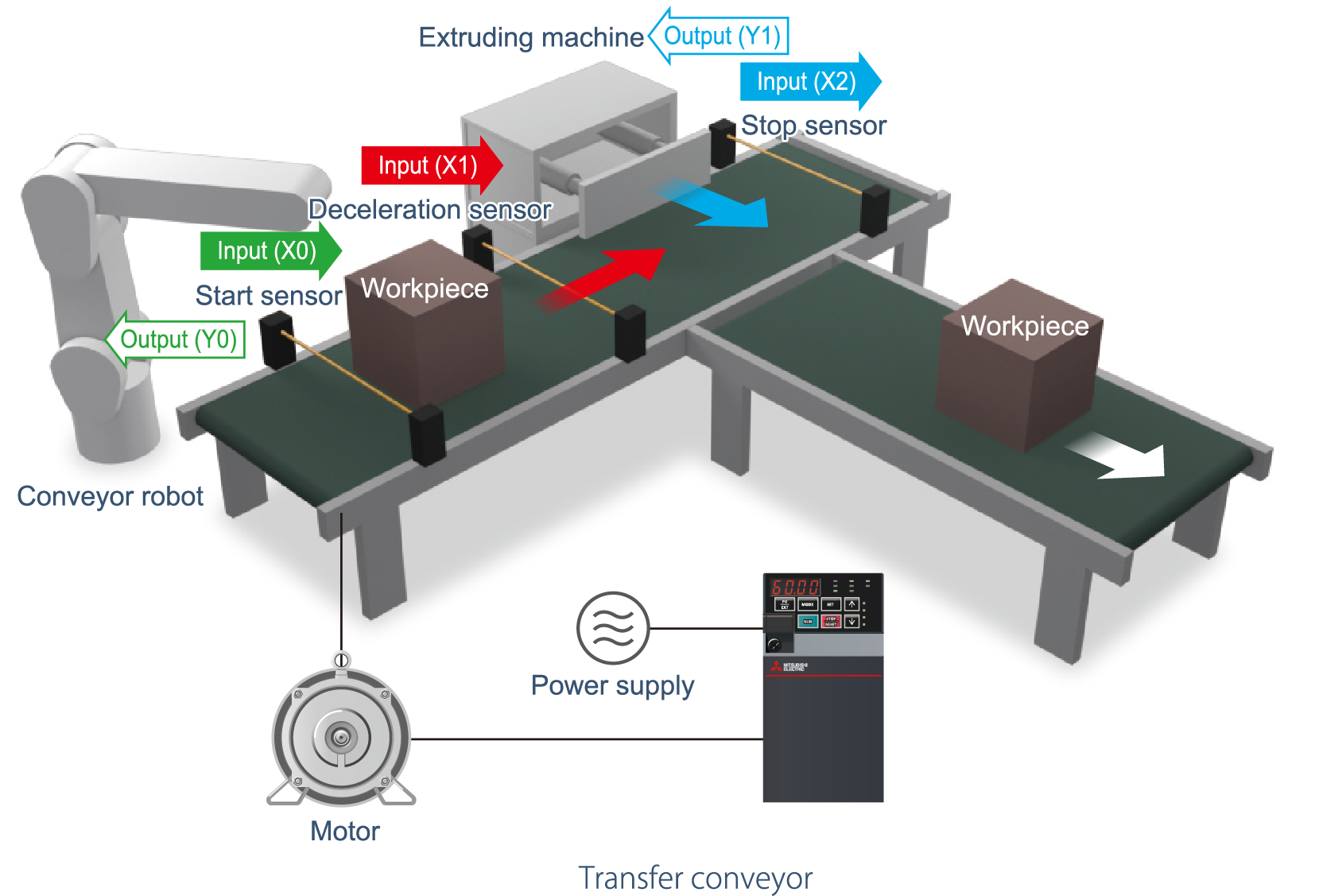
Same spare inverters for various applications E800E800-EE800-SCE
Control method
Switching between control methods with the FR-E800 inverter, Vector control for lift application (with the plug-in option), Advanced magnetic flux vector control for conveyors, etc., reduces the number of required spare inverters.
Control | Speed control |
Torque control |
Position control |
Motor | |
---|---|---|---|---|---|
Easy ↑ ↓ High- performance |
V/F control | ● | ─ | ─ | Induction motor (SF-PR, etc.) |
Advanced magnetic flux vector control | ● | ─ | ─ | ||
Real sensorless vector control | ● | ● | ─ | ||
PM sensorless vector control | ● | ─ | ● | PM motor (MM-GKR, EM-A) |
|
Vector control (with plug-in option FR-A8AP E kit used) |
● | ● | ● | Induction motor (SF-PR-SC, SF-V5RU) |
●: Supported
Accurate and stable transfer
Position control
Positioning under Vector control is available.
The cumulative pulse can be monitored, enabling accurate transfer of glass or PET bottles to the filling position.
Positioning function (point table method)
Position data (target position, speed, acceleration/deceleration time) and so on can be set in the parameters.
Positioning is possible for up to 7 points.
Positioning operation is performed by selecting point table numbers with external interface signals.
Continuous positioning is possible.
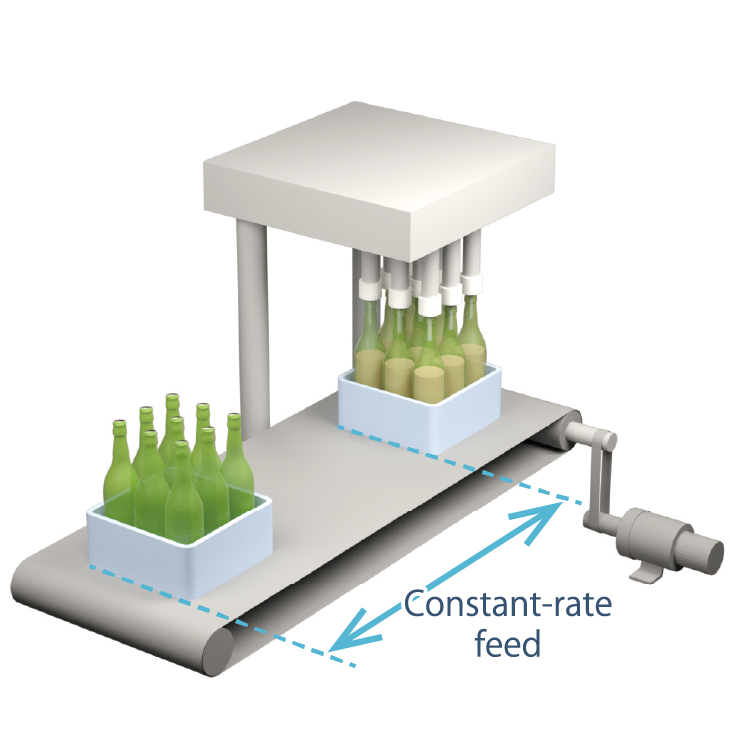
Improving work efficiency by powerful high-speed operation E800E800-EE800-SCE
PM sensorless vector control
The torque is not reduced in the high-speed range (up to the rated speed) during PM sensorless vector control as compared with operation using a stepper motor.
High-speed system operation improves the tact time.
PM sensorless vector control is available when inverters are used with PM motors. High-level control such aspositioning control is enabled without using an encoder.
The PM motor offline auto tuning enables sensorless operation of other manufacturers' permanent magnet (PM) motors. (Tuning may be disabled depending on the motor characteristics.)
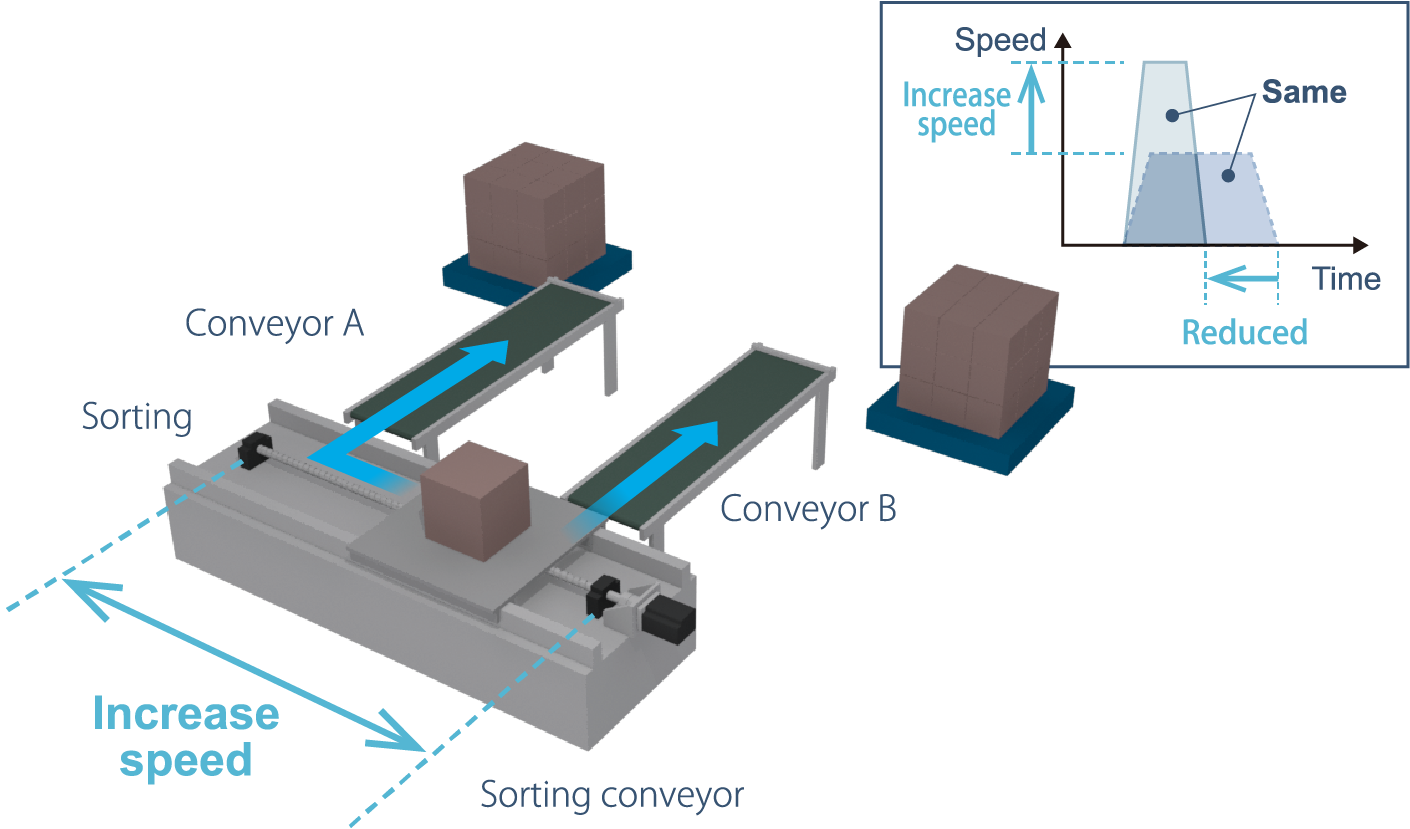
Expanding the range of applications E800 E800-E E800-SCE using
inverter options
E800E800-EE800-SCE
Plug-in options
In addition to the existing plug-in options to add digital inputs / analog outputs and to support different communication standards, the Vector control compatible option FR-A8AP E kit is supported. Among our compact inverters, the FR-E800 inverter is the first to support Vector control.
FR-E800 inverter options
Model | Description |
---|---|
FR-A8AX E kit | 16-bit digital input |
FR-A8AY E kit | Digital output, additional analog output |
FR-A8AR E kit | Relay output |
FR-A8AP E kit | Vector control, encoder feedback control |
FR-E8DS E kit | 24VDC input |
FR-A8NC E kit | CC-Link |
FR-A8ND E kit | DeviceNet |
FR-A8NP E kit | PROFIBUS-DP |