Inverters-FREQROL-F Series -FREQROL-F800- Energy Saving
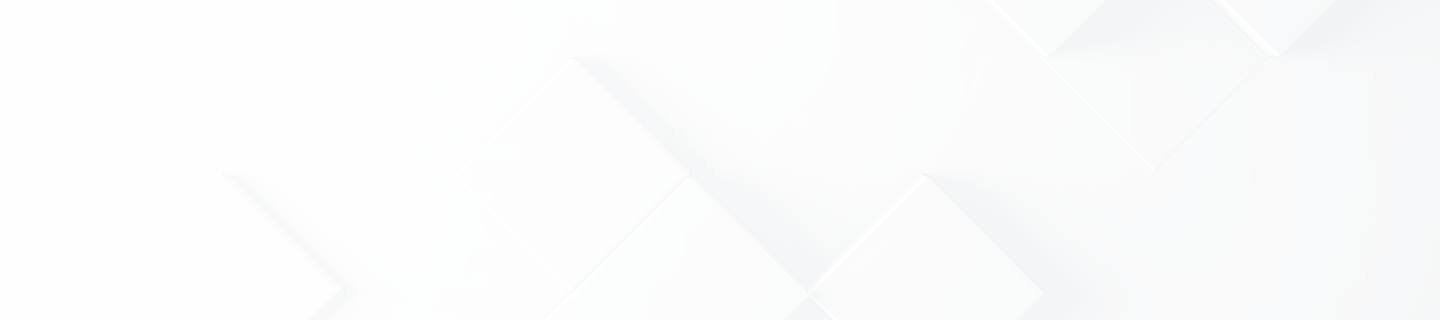
Energy Saving with Inverters
The consumed power of a variable-torque load, such as fans, pumps, and blowers, is proportional to the cube of its rotation speed.
Adjusting the air volume by the inverter rotation speed control can lead to energy savings.
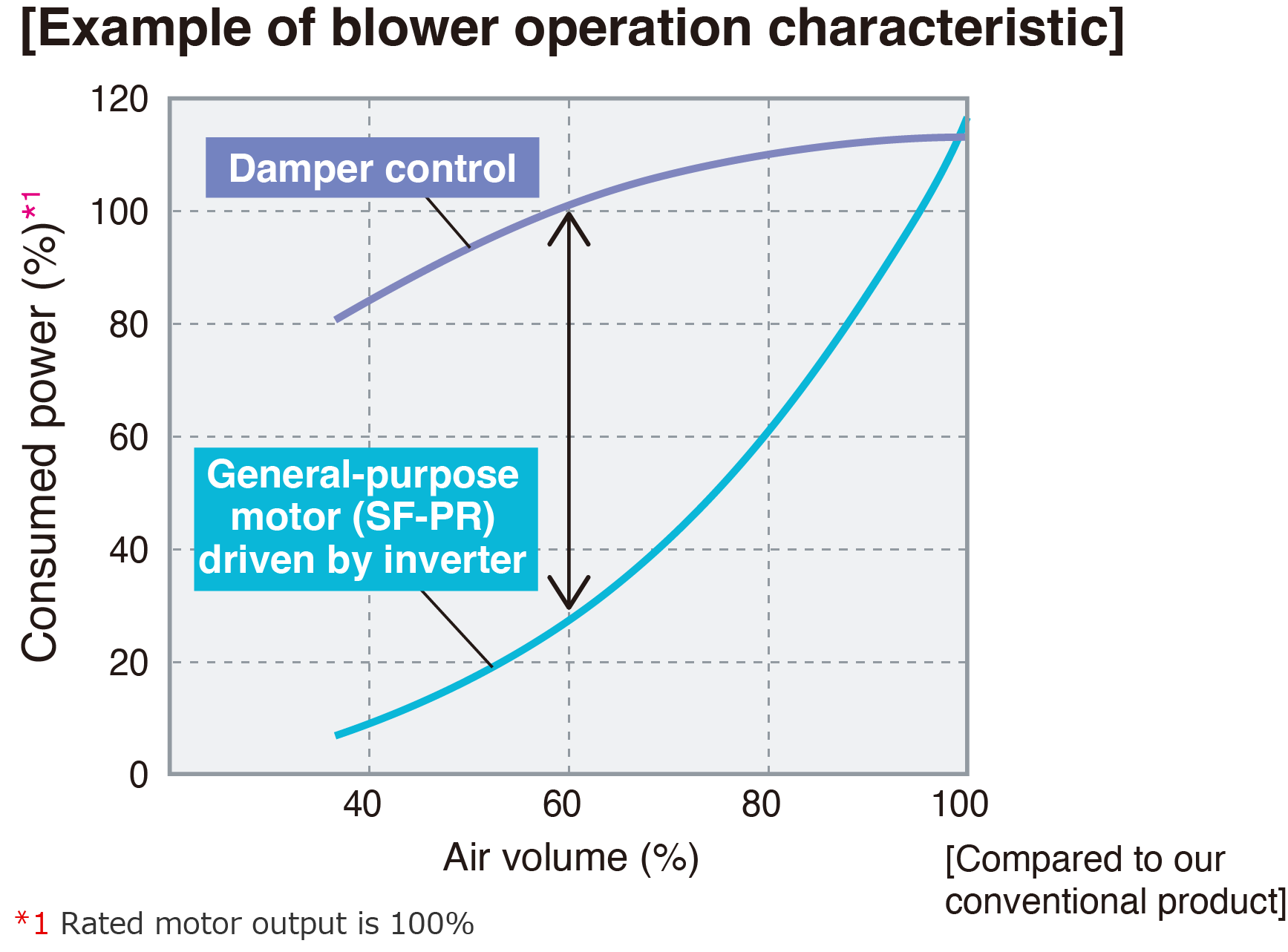
Utilizing the motor capability to the full
Optimum excitation control
- Optimum excitation control continuously adjusts the excitation current to an optimum level to provide the highest motor efficiency. With a small load torque, a substantial energy saving can be achieved.
For example, at 4% motor load torque for a general-purpose motor, the motor efficiency under Optimum excitation control is about 30% higher than the motor efficiency under V/F control.
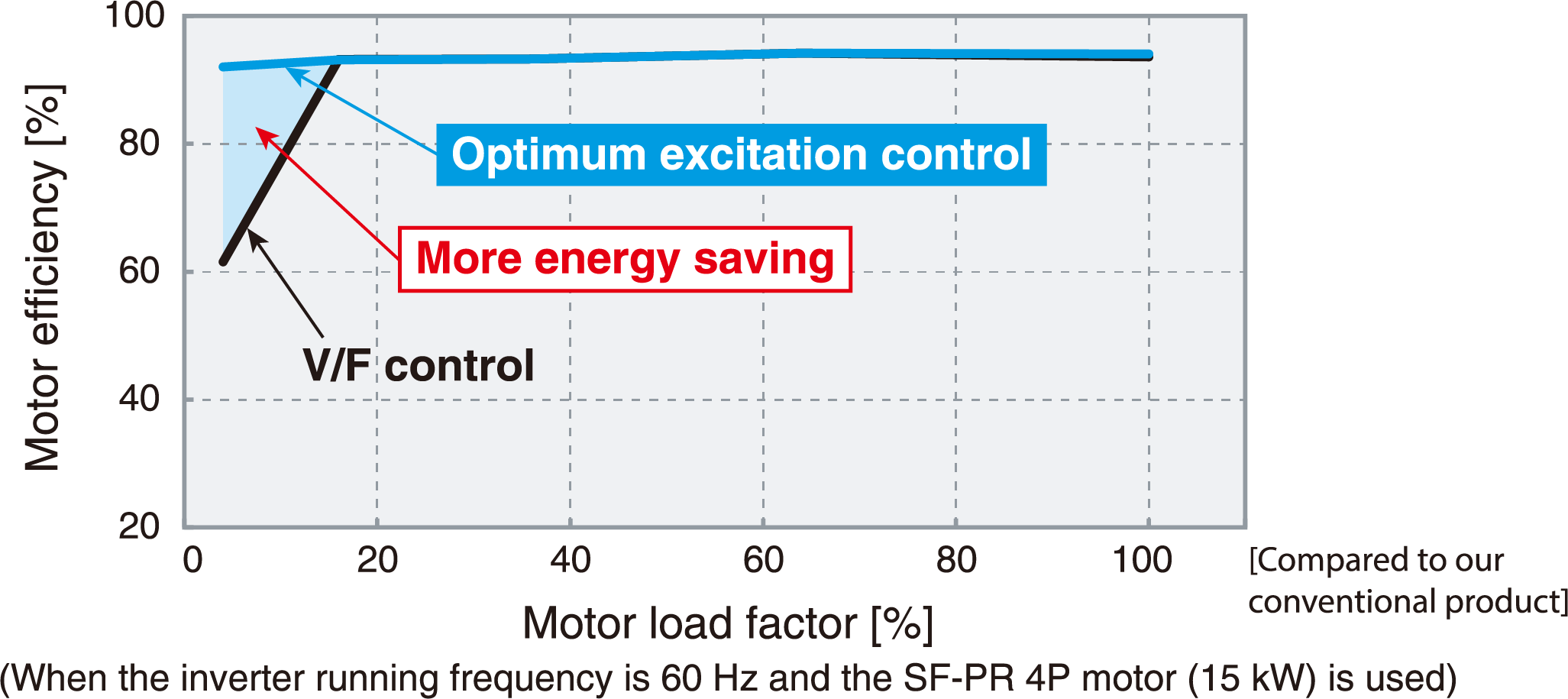
Improving starting torque and saving energy at the same time
Advanced optimum excitation control
Advanced optimum excitation control, which has been newly developed, provides a large starting torque while maintaining the motor efficiency under the conventional Optimum excitation control.
Without the need of troublesome adjustment of parameters (acceleration/deceleration time, torque boost, etc.), acceleration is done in a short time. Also, energy saving operation with the utmost improved motor efficiency is performed during constant-speed operation.
To use Advanced optimum excitation control, set the energy saving control selection parameter (Pr.60) = "9" under Advanced magnetic flux vector control.
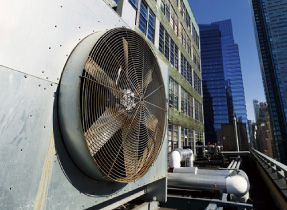
Supporting operations of various motors
Offline auto tuning
The offline auto tuning function to measure circuit constants of the motor enables optimal operation of motors even when motor constants vary, when a non-Mitsubishi Electric motor is used, or when the wiring distance is long. Sensorless operation can be performed with Mitsubishi Electric general-purpose (induction) and PM motors (MM-EFS, MM-THE4) as well as non-Mitsubishi Electric general-purpose (induction) and PM motors*2. The tuning function enables the Advanced optimum excitation control of non-Mitsubishi Electric general-purpose (induction) motors*2, which increases the usability in energy saving applications.
*2Depending on the motor characteristics, tuning may not be available.
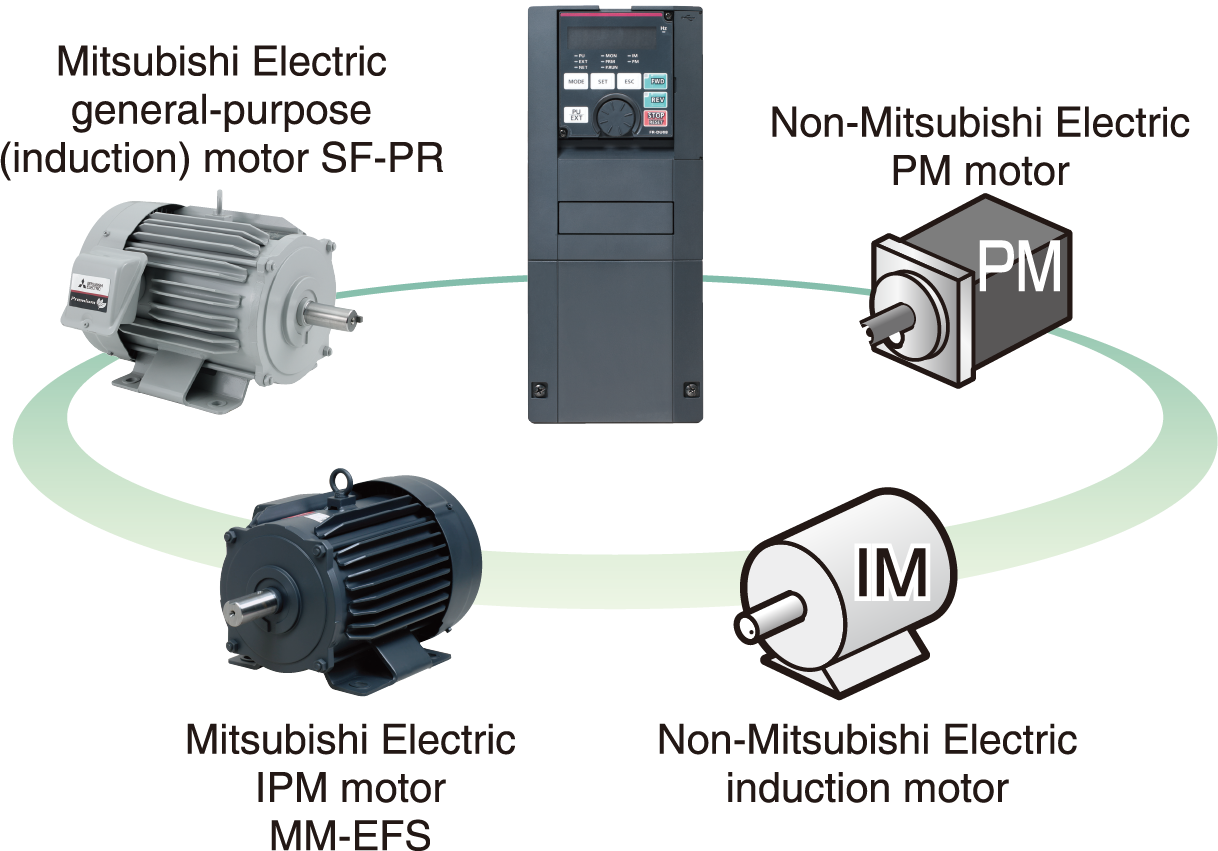
Energy Saving with High-Efficiency Motor
In the international context of global warming prevention, many countries in the world have started to introduce laws and regulations to mandate manufacturing and sales of high-efficiency motors. With the use of high-efficiency motors, further energy saving is achieved.
[IE code]
As an international standard of the efficiency, IEC60034-30 (energy-efficiency classes for single- speed, three-phase, cage-induction motors) was formulated in October 2008. The efficiency is classified into four classes from IE1 to IE4. The larger number means the higher efficiency.

*3The details of IE4 are specified in IEC 60034-31.
Further energy saving with the premium high-efficiency IPM motor
MM-EFS / MM-THE4
- The IPM motor, with permanent magnets embedded in the rotor, achieves even higher efficiency as compared to the general-purpose motor (SF-PR/SF-THE3).
- The IM driving setting can be switched to IPM driving setting by only one setting. ("12" (MM-EFS/MM-THE4) in the parameter [IPM]. Refer to page 124 for details.)
Do not drive an IPM motor in the induction motor control settings.
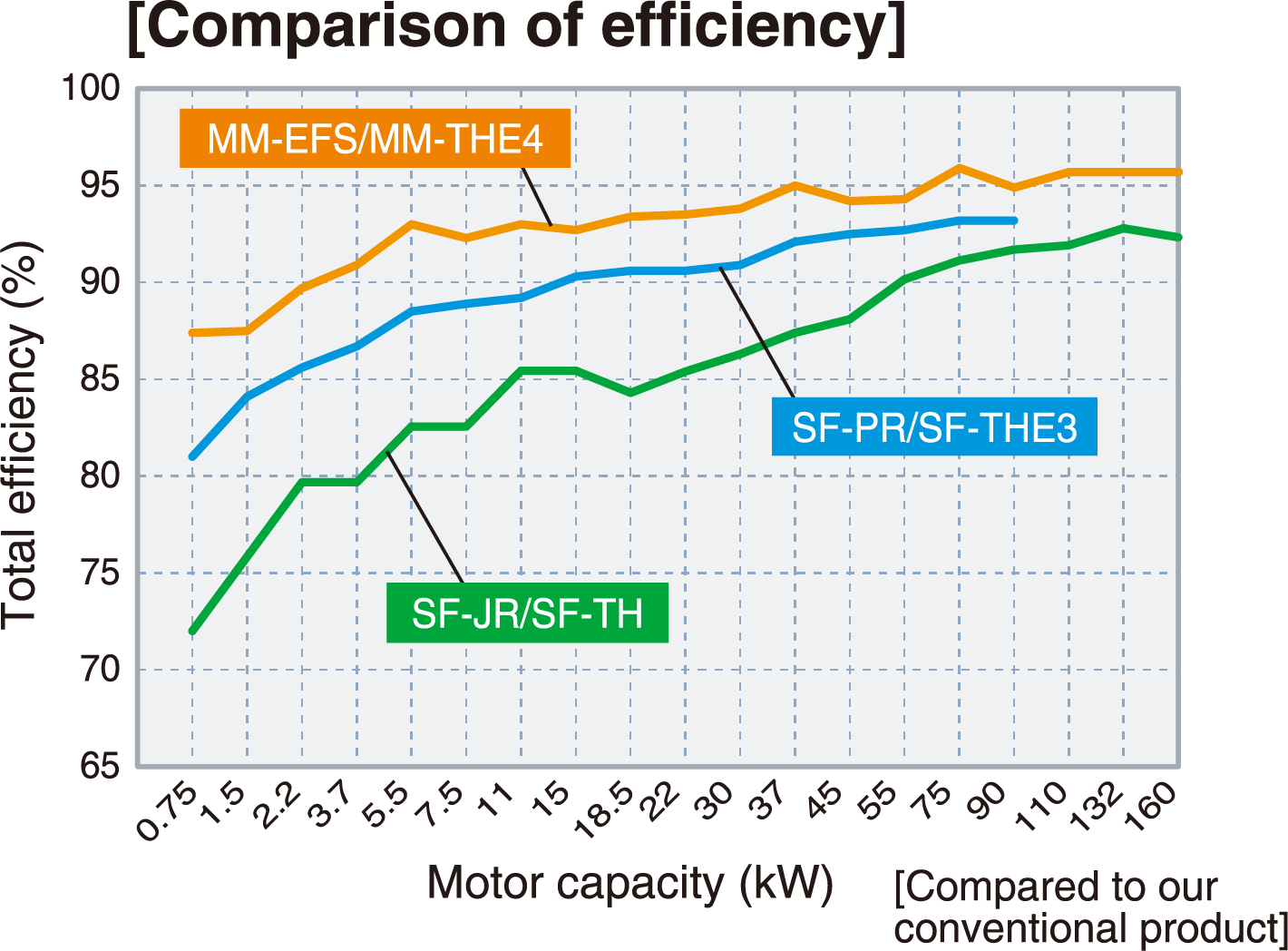
Why is an IPM motor more efficient?
- No current flows to the rotor (secondary side), and no secondary copper loss is generated.
- Magnetic flux is generated with permanent magnets, and less motor current is required.
- Embedded magnets provide reluctance torque*4, and the reluctance torque can be applied.
*4Reluctance torque occurs due to magnetic imbalance on the rotor.
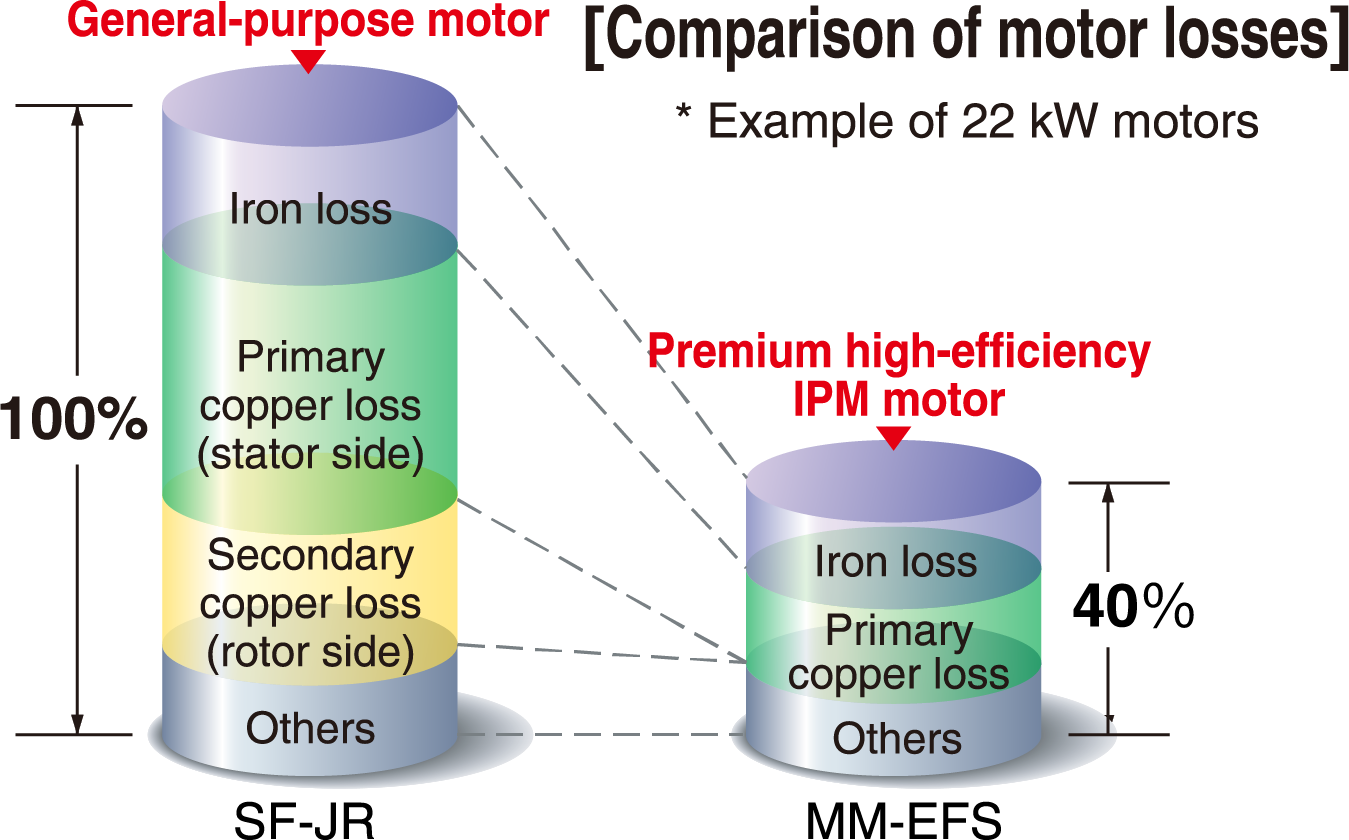
Excellent compatibility with the high-performance energy-saving motor
SF-PR
Motor constants are stored in the inverter. Energy-saving operation can be started just by setting parameters. The SF-PR motor conforms to the Japanese domestic Top Runner Standard (IE3 equivalent). Its energy-saving operation contributes reduction in the electricity charges, which in turn lowers the running cost.
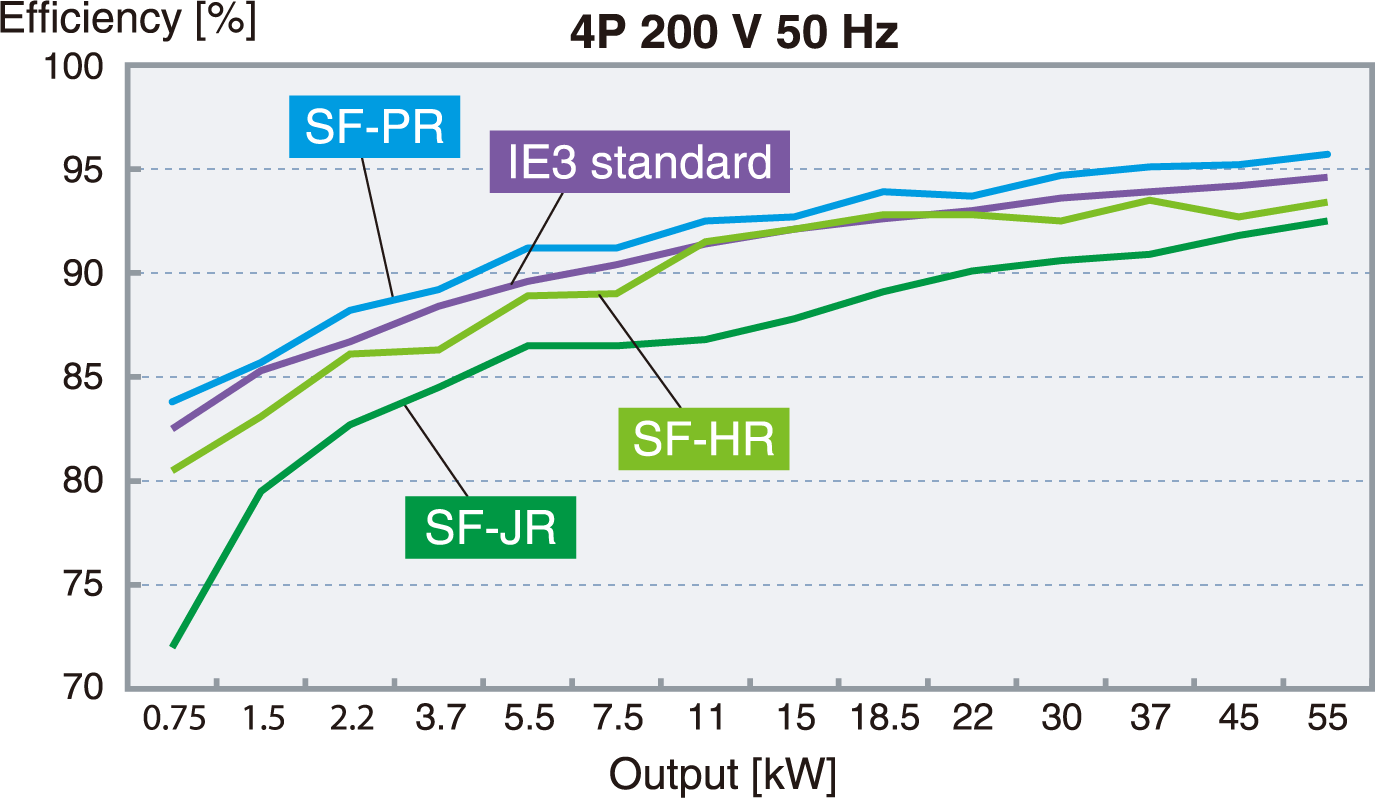
Energy-Saving Functions Suitable for Various Systems
Standby power reduction
- With the 24 VDC external power supply, the input MC signal can be turned OFF after the motor is stopped, and turned ON before activating the motor. The inverter enables self power management to reduce standby power.
- The inverter cooling fan can be controlled depending on the temperature of the inverter heatsink. Also, signals can be output in accordance with the inverter cooling fan operation. When the fan is installed on the enclosure, the enclosure fan can be synchronized with the inverter cooling fan. Extra power consumption when the motor is stopped can be reduced.
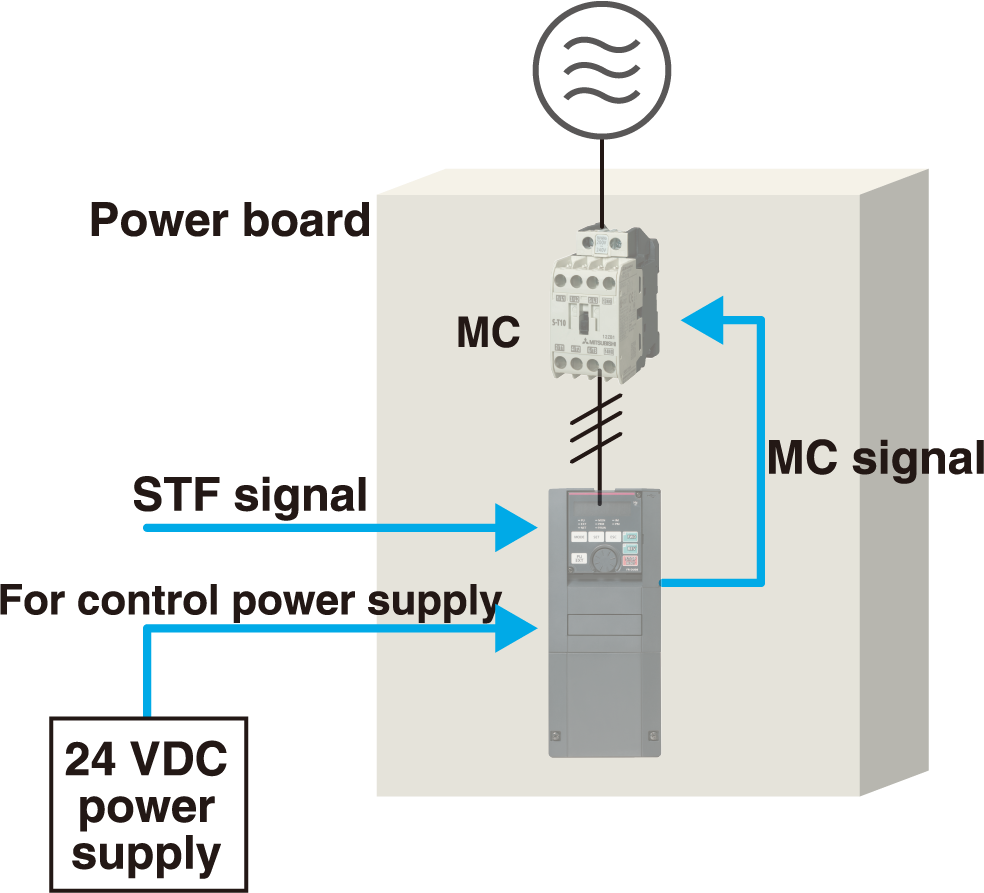
Energy saving at a glance
Energy saving monitor / Pulse train output of output power
- Energy saving monitor is available. The energy saving effect can be checked using an operation panel, output terminal, or network.
- The output power amount measured by the inverter can be output in pulses. The cumulative power amount can be easily checked.("12" (MM-EFS/MM-THE4) in the parameter [IPM]. Refer to page 116 for details.)
[Furthermore]
With the Mitsubishi energy measuring module, the energy saving effect can be displayed, measured, and collected.
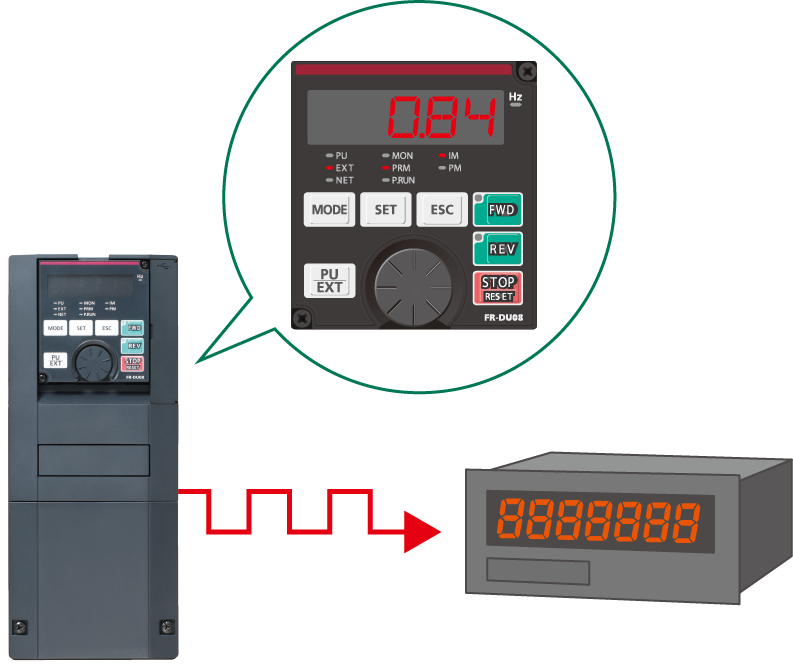
Effective use of the regenerative energy (Option)
FR-XC / FR-HC2
Multiple inverters can be connected to the power regeneration common converter (FR-XC) or the high power factor converter (FR-HC2) through a common PN bus. The regenerated energy is used by another inverter, and if there is still an excess, it is returned to the power supply, saving on the energy consumption.
The 355K or higher models are inverter-converter separated types, which are suitable for power regeneration.
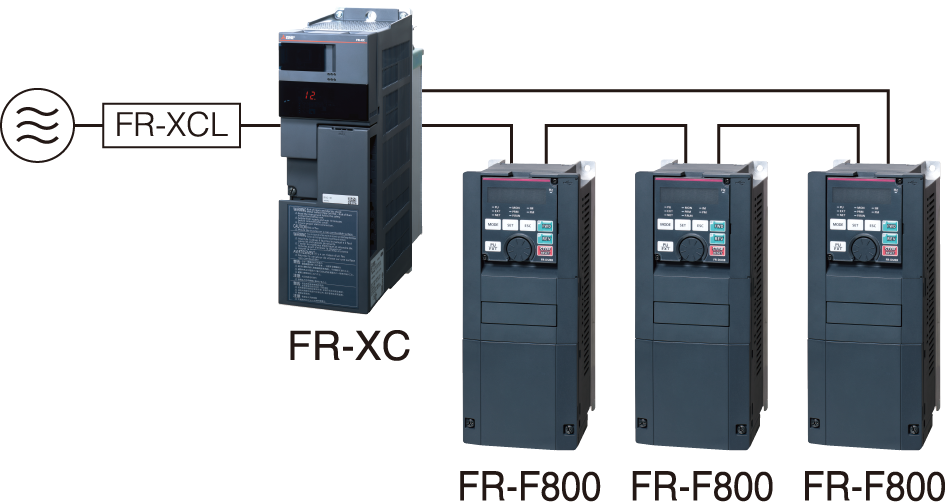