Function expansion options MELFA Smart Plus
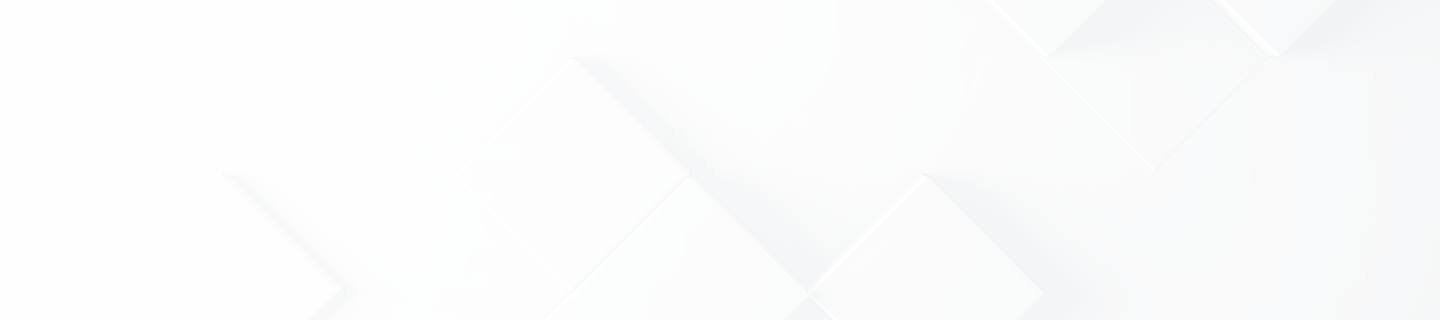
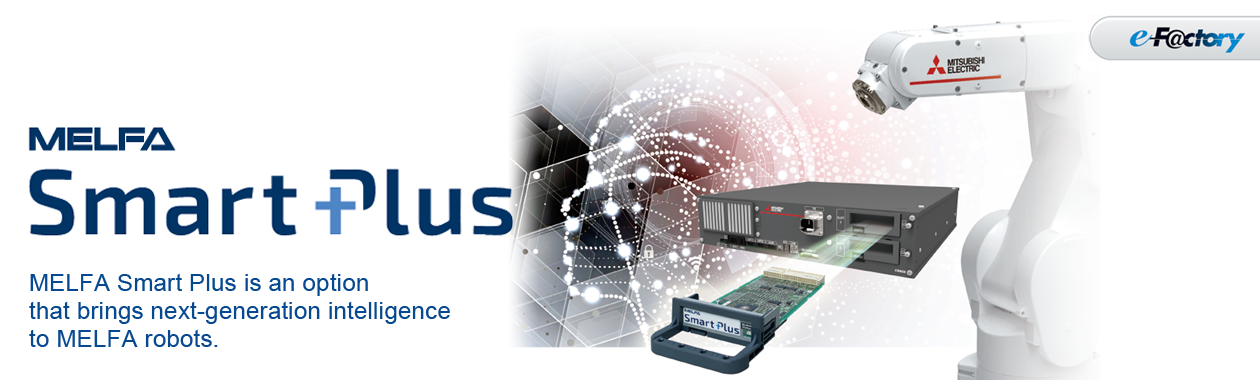
Calibration assistance function
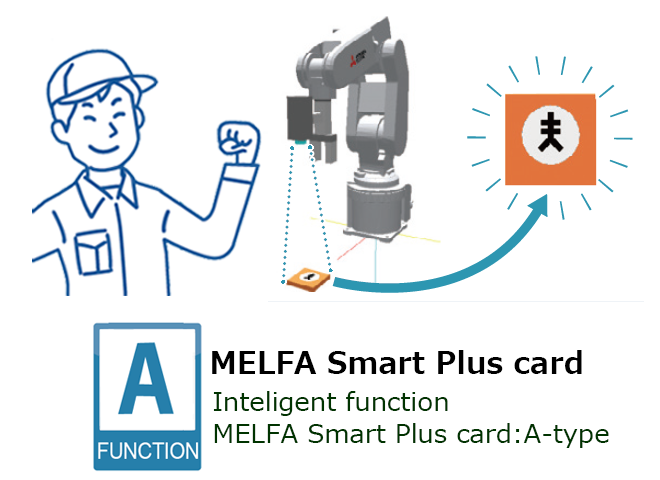
Time-consuming teaching a 2D vision sensor has been automated and accuracy improved.
Supported MELFA Smart Plus card type
Function name | Usefulness |
---|---|
Automatic calibratio | Robot/2D vision sensor integration |
Calibration of work coordinates | Robots and peripheral devices/jigs |
Relative position calibration | Robots working with robots |
For details on this function, please refer to the catalog "MELFA Smart Plus".
Automatic calibration

Simple set-up and improve accurancy
Time-consuming teaching has been automated and accuracy improved.
- Automating the teaching process has made set-up easier.
- Configure settings such as the camera position, FOV, and resolution in the automatic calibration window. Automatic teaching and automatic calibration is possible.
- With automatic calibration, operating conditions are stabilized and accuracy is increased.
Cameras can be mounted in three positions
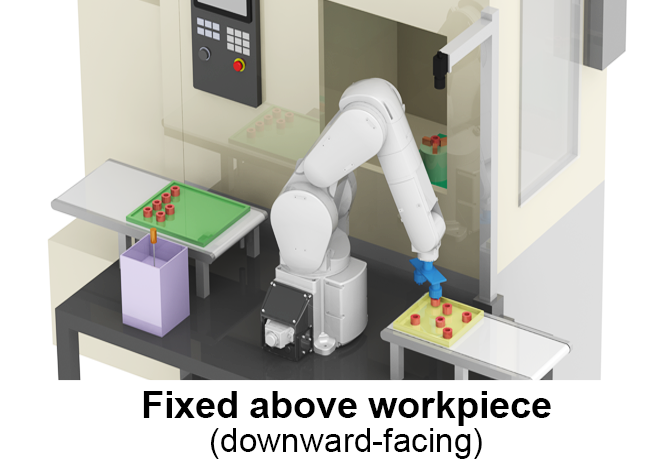
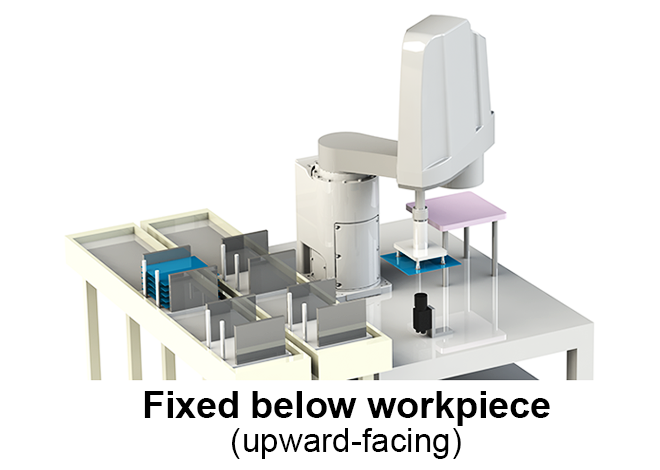
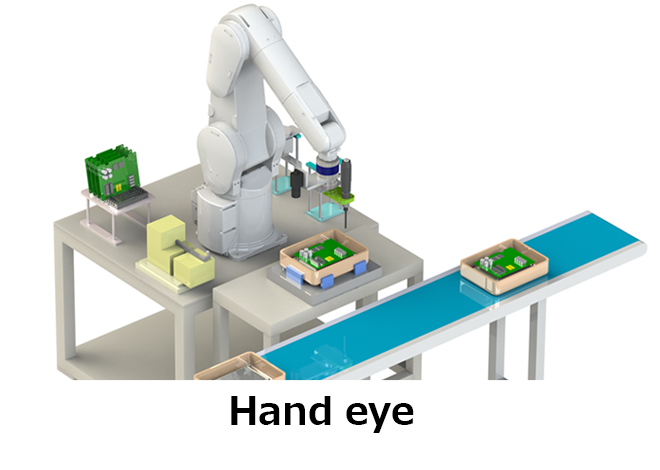
Calibration of work coordinates
Teaching is now automated. This makes calibration of the robot and peripheral devices extremely simple.
Note1) This function can only be used when a 2D vision sensor is used as a hand eye.
Note2) Horizontal articulated robot (4-axis) not supported.
Troublesome teaching work eliminated
Teaching of workpiece coordinates is automated. Set-up time and troublesome work reduced.
Automatic calibration is possible even in environments where the workpiece coordinates and the robot's relative position change.
Easy calibration of robots and pallets installed on automated guided vehicles (AGVs) or carts.
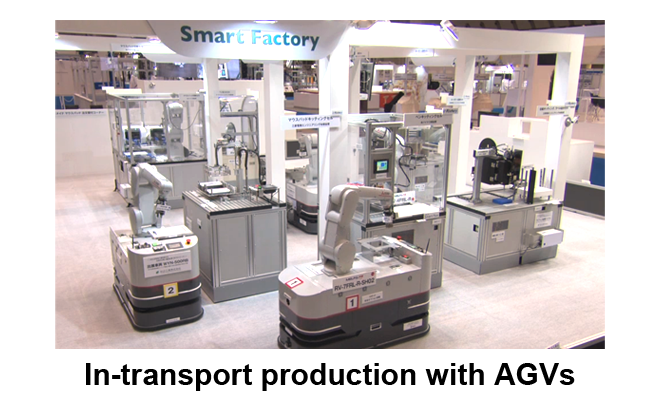
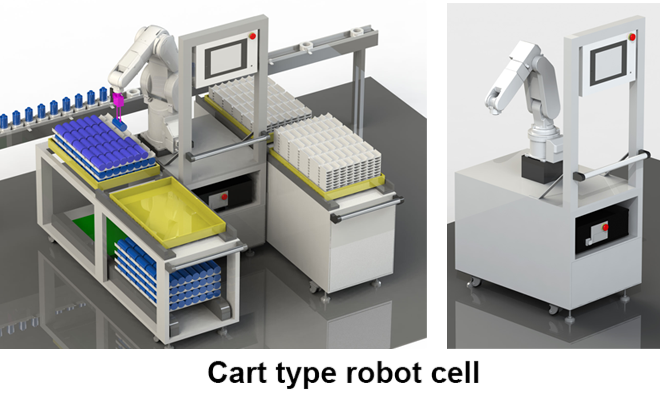
Relative position calibration
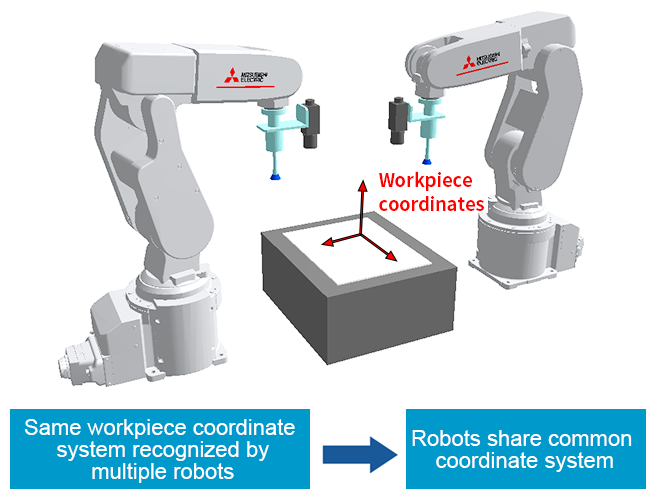
Intricate teaching of the robot is automated. Setting up interference avoidance and collaborative operation is now extremely simple!
Note1) MELFA FR series D type robots not supported.
Note2) Horizontal articulated robot (4-axis) not supported.
Reduce man-hours spent
Reduce man-hours spent improving accuracy and setting up interference avoidance and collaborative operation.
Calibration is automated so that the same work coordinates can be used by multiple robots. Reduce worker errors and workloads.
Example
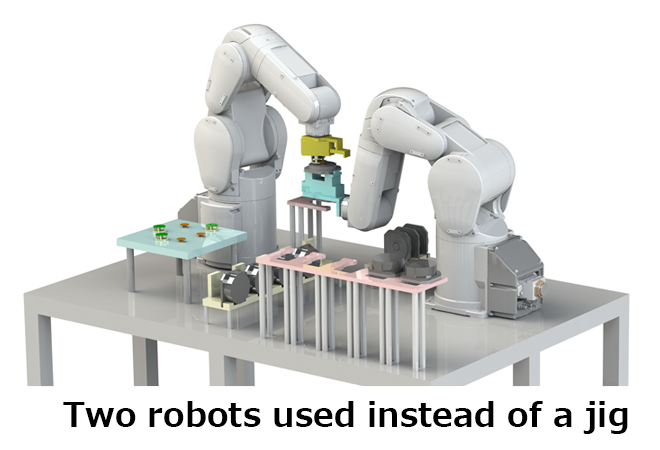
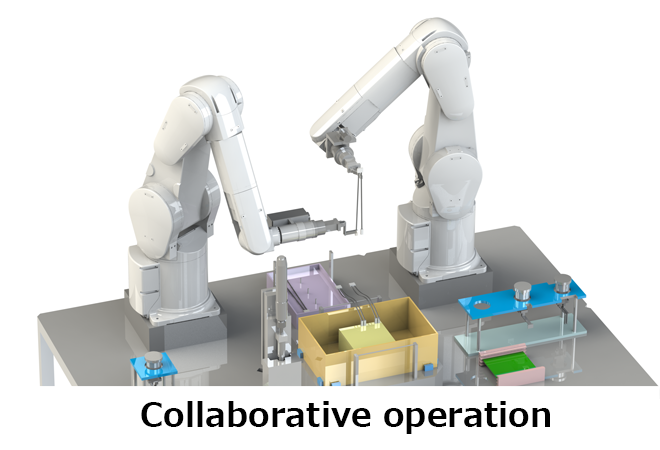
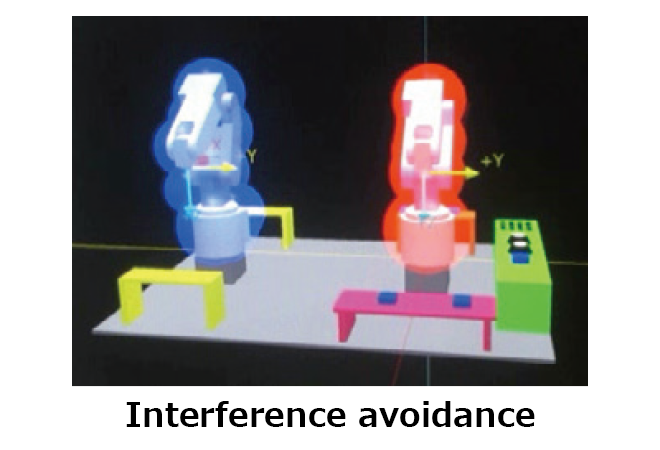
Supported devices
MELFA Smart Plus card type
Component name | Model name | |
---|---|---|
MELFA Smart Plus card | A-type | 2F-DQ511 |
MELFA Smart Plus card pack | A-type | 2F-DQ510 |
AB-type | 2F-DQ520 |
Robot
Function name | Robot Type | Robot controller | RT ToolBox3 |
---|---|---|---|
Automatic calibratio | FR series, CR series |
CR800-D/R/Q Ver.A3 or later. (MELFA Smart Plus cardpack [2F-DQ510]: Ver.A1 or later.) |
Ver.1.00 or later |
Calibration of work coordinates | RV-FR series, RV-CR series (*1) |
CR800-D/R/Q Ver.A3 or later. (MELFA Smart Plus cardpack [2F-DQ510]: Ver.A1 or later.) |
|
Relative position calibration | RV-FR series (*1) | CR800-R/Q Ver.A3 or later.(*2) (MELFA Smart Plus cardpack [2F-DQ510]: Ver.A1 or later.) |
*1) Horizontal articulated robot (4-axis) not supported.
*2) D type robots not supported.