Solutions
Logistics
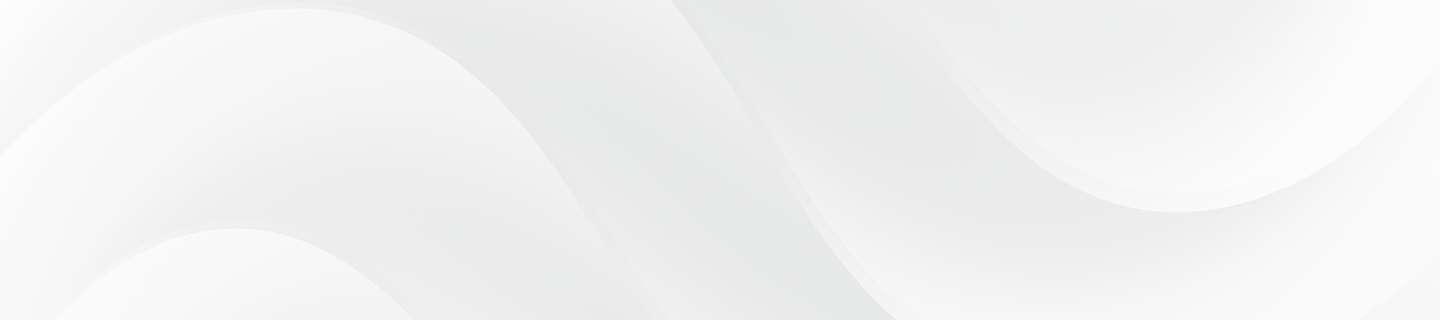
Robot
Promotion of automation
- Smart picking achieved by robot-mounted AGVs and next-generation intelligent robots equipped with a vision sensor
- Operation monitoring and preventive maintenance realized by networking FA devices equipped on AGV
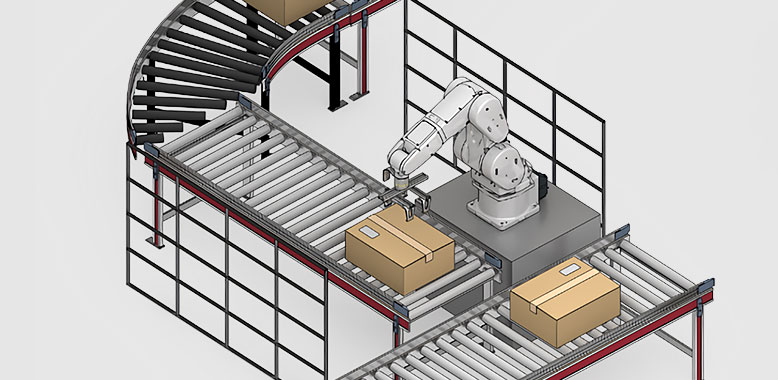
Solutions to the Issues
Issues | Solutions |
---|---|
Automation of lines with large transport volumes, simple transport and boxing tasks | High-speed vision picking system. Automation with industrial robots including peripheral sensor equipment |
Prediction of robot failure time | Preventive and predictive maintenance function |
Collaboration between humans and robots | Optimum layout by collaborative robot |
Loading and Unloading cargo to AGV | Automation by mounting robot on AGV |
System Configuration
feature
Automation of lines with large transport volumes, simple transport and boxing tasks
Realization of Pick & Place and Boxing system by MELFA-FR series robot
In addition to automating the high-speed transfer and alignment of workpieces by a scalar robot, Boxing by vertical robot is realized by utilizing peripheral sensor equipment such as vision sensor.
Pick and place packing
Prediction of robot failure time
Preventive and Predictive Maintenance Functions with the MELFA SmartPlus Option Card
Health management of robots through status tracking
■ Early detection of abnormalities through continuous monitoring (Abnormality detection function)
Using proprietary technology to detect signs of failure before a serious failure occurs. Enable maintenance and prevent equipment shutdowns (Reduction Gear and Encoder)
■ Check the wear rate of the drive parts (wear calculation function).
The degree of wear of the driving parts is estimated from the operating state of the robot. Notification of maintenance timing (dedicated signal output and warning output), Support for efficient maintenance, including prioritization of maintenance (grease, belt, reduction gear, ball screw, bearing)
■ Simulation of wear and tear (maintenance simulation)
Estimation of the replacement timing of maintenance parts and maintenance of overhauled parts, the maintenance cycle can be planned beforehand. It can also be used to verify the operation to extend the life of the robot
■ Supports construction of maintenance systems
Various types of maintenance data can be used on robot programs, and can also be output to IT systems and GOT, supporting construction of maintenance systems suitable for customer equipment.
Collaboration between humans and robots
Collaborative Robots
Collaborative solutions that are easy to deploy by anyone, anywhere quickly
- Rounded appearance for intrinsically safe design that prevents hands and fingers from being pinched and for reducing pressure in case of collision
- Operation button mounted on arm instead of teaching box
- Arm-mounted LEDs facilitate robot status monitoring
- Visual programming on tablet screen makes robot programming unnecessary
Loading and Unloading cargo to AGV
Collaborative Robots
Efficient inter-process transportation can be realized by mounting a robot on AGV
Collaborative robots installed on AGVs to reduce labor costs for loading and unloading work. Production and quality information can be collected and managed in an integrated manner through the cooperation of high-level management systems.
AGV + Robot Exhibition
Image of cooperation between host systems and the field
AGV + Robot Inter-process Conveyance
AGV + robots in each process
Production status monitor screen