The Inside View
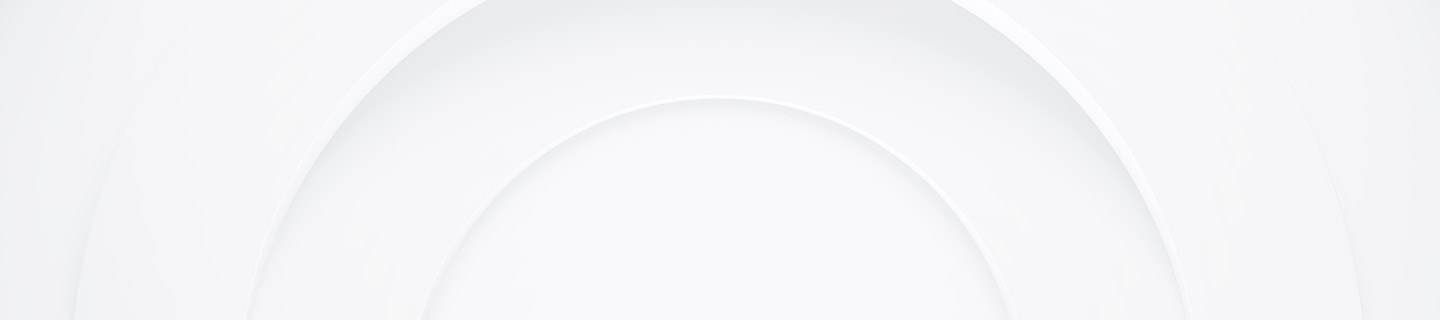
Hiroshi Nishiyuki highlights how IloT applications can deliver ‘visible’ results
First Published in Japanese in May 2021 [3 parts]
Summary
"The Inside View" provides perspectives and insights into today’s manufacturing industry, reflecting current social and industry trends in Japan and the rest of the world. Our experts, who have been deeply involved in factory automation (FA), often in product development for example, share tips for manufacturers that could lead to new insights.
In this three-part series, Hiroshi Nishiyuki, Head of Mitsubishi Electric’s FA System Solutions Department, explores how industrial internet-of-things (IIoT) applications can deliver ‘visible’ results.
Every factory is different, especially when it comes to applying IIoT to manufacturing operations, however, applications like "tool wear diagnosis", "visualization" and "predictive maintenance" can be deployed to solve common problems. Here, Nishiyuki introduces each of these IloT-driven applications and the benefits they bring to the factory floor.
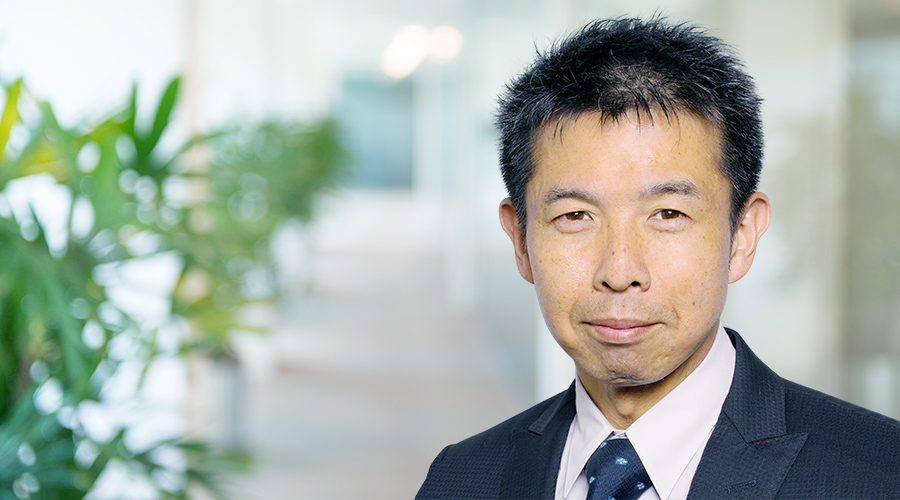
Hiroshi Nishiyuki
Hiroshi Nishiyuki was born in Mie Prefecture, Japan in 1970. He completed his master’s degree in information systems at the Graduate School of Information Engineering, Kyushu Institute of Technology (Japan), and joined Mitsubishi Electric Corporation in 1994. Initially working at the company’s Nagoya Works, FA Systems Department, he was engaged in the development of PLCs. In 2017, he transferred to Mitsubishi Electric Europe B.V. (Germany), belonging to the FA-European Development Center, where he was involved in research on market trends related to industrial automation in Europe and the development of products for the European market. In 2020, he returned to Nagoya Works, FA Solution Systems Department, where he worked on the deployment of e-F@ctory solutions based on Industrial Internet of Things (IIoT) using products from Mitsubishi Electric and its partners. Currently, Hiroshi Nishiyuki is the Head of FA System Solutions Department.