Clear work procedures improve productivity and quality
First released April 2015
The latest addition to Mitsubishi Electric’s Nagoya Works, the E4 production site, leverages e-F@ctory technologies to take visualization of operations and energy saving to new levels. On the 5th floor, PLCs and HMIs are assembled using a cellular manufacturing system. When production began at E4, the focus was on improving quality and the productivity of new workers while reducing the burden on experienced operators.
Key points of this case study
- 1. Preventing mistakes in component selection by using system-linked boxes
- 2. System supports the selection of screwdrivers with pre-set torque values to stop quality failures
- 3. Collecting on-site data to identify areas for improvement
Introduction to the Nagoya Works – E4 cellular manufacturing line
To ensure high product quality and productivity, certain procedures must be strictly followed during the assembly process. Mitsubishi Electric produces many different types of PLCs and display units - each involving different methods and components - so a cellular manufacturing system has been preferred for over ten years. In contrast to a fully automated line, a cellular approach allows workers to flexibly change production methods according to instructions, making it suitable for manufacturing many different types and variations of products.
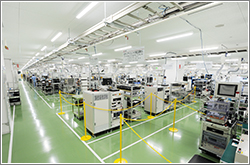
The 5th floor cellular manufacturing line improves efficiency with people and machines working together
However, the process involves checks by workers, which means that human error can impact on product quality. In the cellular manufacturing facility where PLCs and GOT HMIs are produced, incremental improvements have been made in an attempt to eliminate operator errors.
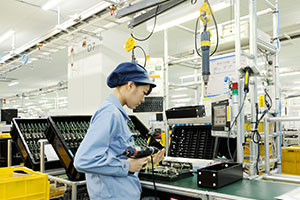
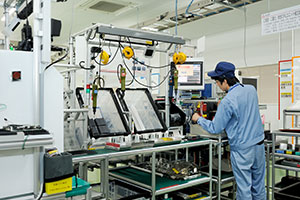
Cellular manufacturing facility producing PLCs and GOT HMIs
These efforts have succeeded in reducing the number of product failures caused by operator error to 1/10 over the past ten years. To bring this figure even closer to zero, the 5th floor of the E4 building has been upgraded by harnessing e-F@ctory technology.
Different screws and screwdrivers for different purposes
“In the assembly process for PLCs, some models use up to 16 screws of five different types, which need to be tightened using four separate screwdrivers. Workers are always worried about making mistakes because it’s so complicated,” says Mikio Iijima, Senior Manager of the Factory Automation (FA) Manufacturing Technology Section. This process might be fine for an expert technician, but the production site employs various categories of workers, some of whom are less experienced. As a result, skilled workers need to spend extra time providing guidance to new starters, and this training takes up a lot of time.
On the new production line, the company decided to set up a system to help inexperienced workers get started as quickly as possible. A priority was to reduce the amount of guidance that skilled personnel needed to provide. The system supports people in two main ways: “using the right components” and “mounting components correctly”.
Showing workers where to find components
Regarding “using the right components”, a system consisting of production instructions, display units and “Poka-Yoke” terminals to open the boxes of screws helps operators to pick components correctly. When a worker scans the barcode on the work instructions provided by the control system, the components to be prepared are shown on the screen in front of them. The lid of the box containing the right screws opens automatically, and the worker is prompted to take out the specified amount. This prevents mistakes during picking, even if someone does not check the work instructions.
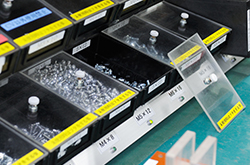
A light comes on to show which box components should be taken from
After the correct number of the appropriate screws are taken out, another function supports “mounting components correctly”. The procedure is again shown on the display, and a built-in light indicates which screwdriver is to be used. When the worker finishes using the screwdriver, another light indicates which should be used next. This prevents errors in the component mounting sequence and ensures operators use the right screwdrivers. Each screwdriver is pre-set to the optimum torque to ensure the correct tightening.
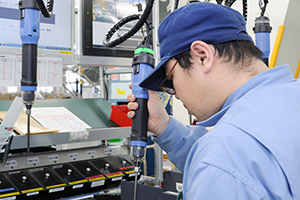
Lights on each screwdriver come on in the order in which they should be used
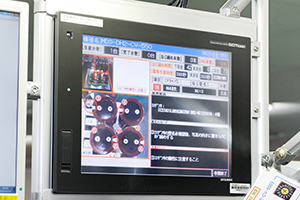
The display unit shows details of screw locations and sequence to prevent mistakes
“At factories in other locations, sometimes work is done without fully reading the procedures, which can adversely affect quality. This system will allow work to be unified, no matter where it is carried out,” says Iijima. Data from controllers is uploaded to the database, which also helps to ensure traceability in the unlikely event of a failure being identified after products have been shipped.
Improvements based on accurate data
By ensuring workers select the right parts and use them correctly, the system reduces the burden on experienced workers to train new workers. Another huge benefit is that the system has provided opportunities to make improvements on site.
“For example, if we find a lot of screw tightening failures on a specific product, by thinking about the cause and making improvements, we should be able to increase quality and reduce cycle times by preventing failures,” explains Iijima. If failures are appearing in proportion to how experienced workers are, then the issue can be addressed effectively by identifying skill gaps and then providing intensive training to newer personnel to address this.
If tightening failures are appearing on a certain product regardless of operator experience, it shows that there is something wrong with the work procedure for that part. This could provide evidence for enhancements beyond the factory floor, such as improving the jig used or even design changes to the components or mounting parts.
Such improvements are now possible because all data related to on-site work is automatically collected and stored in a database. On-site data is vital for the Kaizen process of continuous improvement. Without data, areas for improvement cannot be identified, and the effects of refinements cannot be verified. By linking FA and ICT equipment, e-F@ctory provides all the on-site data necessary to achieve this.
“Simply bringing in new production equipment from Japan does not necessarily improve productivity and quality at factories in other nations. I have also experienced situations where imposing Japanese Kaizen improvement techniques has had the opposite effect, because our methods do not suit how people work in that country. We need to leverage equipment, and that’s where e-F@ctory comes in,” says Iijima. The cellular manufacturing system at the E4 site shows the importance of this in actual operations.
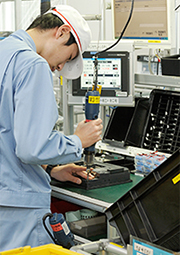
Identifying improvements from screw tightening failure data
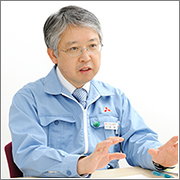
Mikio Iijima, Senior Manager of the FA Manufacturing Technology Section
An ever-evolving system
The E4 site has only been operating for a short time, but the system has already started evolving to its next stage. A primary development is a method for checking the quantity of screws in real time. The aim is to create a system that will weigh the box after screws are taken out to ascertain available stock, then combine this with order information to calculate the quantity required and automatically order more to make up any shortfall. This is only possible because the FA system managing on-site work is linked with the ICT systems controlling production planning and inventories.
Another new feature is the measurement and analysis of screw tightening times. Cameras are used for this, and information about the variation in tightening times is analyzed to improve jigs or determine whether design changes are required. Tightening times should be proportional to the worker’s proficiency - but if there is random variation with no correlation between the two - it indicates that efficiency is being adversely affected by another factor. e-F@ctory solutions allow all kinds of data to be measured and analyzed, so essentially, the development possibilities are endless.
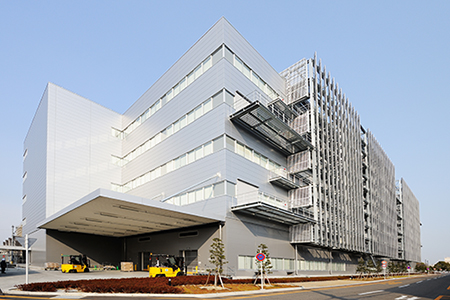
The latest E4 production site harnessing e-F@ctory technologies