Energy saving control system for air conditioning and lighting
First released September 2015
The E4 manufacturing site at Mitsubishi Electric’s Nagoya Works employs the latest e-F@ctory technologies to boost productivity and quality. Beyond this, the solutions have also unlocked new energy savings – a vital advantage in manufacturing. Energy consumption is visualized via PLCs linked to an open network, and flexibility is built into the system to achieve even greater efficiency gains.
Key points of this case study
- 1. Air conditioning and lighting controlled by PLCs to provide visualization of energy usage
- 2. Use of general-purpose PLCs allows easy maintenance and improvement
- 3. Total energy saving of 30% achieved in combination with high-efficiency equipment
Introduction to the Nagoya Works – E4 Building
The E4 Building at the Nagoya Works, which manufactures PLCs and HMIs, acts as a real-world implementation model for e-F@ctory technologies. It has shown that putting the e-F@ctory concept into practice delivers benefits in terms of energy saving, as well as improved productivity and quality.
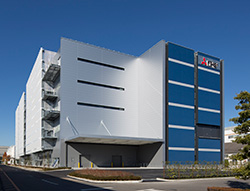
Along with enhancing the efficiency of its manufacturing operations, Mitsubishi Electric focused on saving energy across its office buildings. “At E4, we wanted to save energy on air conditioning and lighting by leveraging e-F@ctory technologies,” says Toshinobu Kishi, Production Planning Section Manager at the Production System Promotion Department, Nagoya Works.
Reduced energy consumption in this type of setting is best achieved with the visualization of power usage and precise control of air conditioning and lighting. An office building or factory would normally use dedicated controllers for this, usually provided by the building management system or air conditioning equipment vendor. However, at the E4 Building, instead of dedicated controllers, facility managers decided to use e-F@ctory technologies: specifically, the PLCs typically used to control the production line.
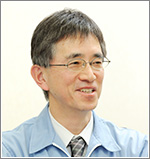
Toshinobu Kishi, Production Planning Section Manager, Production System Promotion Department, Nagoya Works
A flexible, low-cost solution based on general-purpose products
The first step in the project was to review the air conditioning system. A conventional setup uses dedicated control equipment to heat or cool air taken from outside. However, at E4, PLCs were introduced to carry out this task. Sensors are used to monitor the temperature and humidity levels inside the building, and this information is gathered and sent to the PLC. If the indoor temperature rises or the exhaust volume grows due to increased operation of production equipment, the PLCs adjust the amount of air supplied by the outdoor units, maintaining an appropriate temperature and humidity inside the building. This allows optimal management of both air volume and temperature/humidity. Outdoor air conditioning units and PLCs are installed on each of the building’s six floors. The controllers are connected to a CC-Link IE open field network and managed by a central PLC.
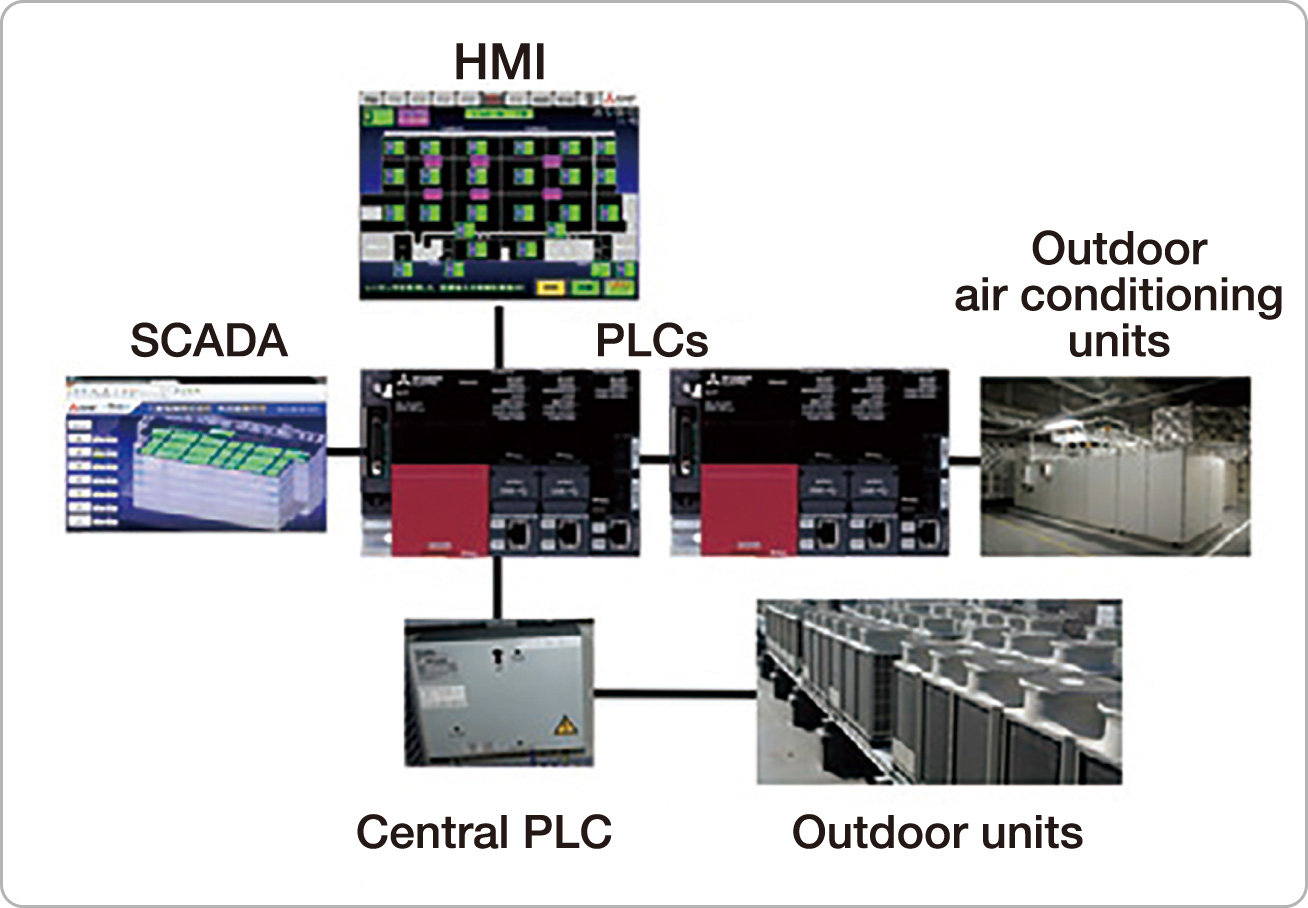
Air conditioning control system in the E4 building. PLCs control external air conditioning units, which can be operated using an HMI or MC Works
The central PLC can be operated via the SCADA software MC Works. This controls the PLCs and external air conditioning units on each floor as well as the dampers of the air inlets, among other systems. It also monitors changes in power consumption. When e-F@ctory technologies, such as PLCs, are deployed at a production site, data can be collected from equipment and analyzed as well as visualized by the ICT system to drive improvements. At the E4 building, this approach has been used to control the air conditioning systems, resulting in an application of the e-F@ctory concept that promotes energy saving activities.
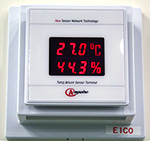
Temperature and humidity sensors installed throughout the E4 building for air conditioning control
One of the reasons for constructing this centralized control system with PLCs instead of dedicated controllers was to ensure ease of maintenance. “The solution consists of general-purpose PLCs and a CC-Link IE open network, which means on-site production engineers can perform maintenance work themselves without relying on specialist engineers,” explains Atsushi Kojima of the Environmental Promotion Section, Production System Promotion Department, Nagoya Works.
If the air conditioning setup used dedicated controllers, maintenance work would require specialized expertise. Vendor technician call-outs would be necessary every time the layout was changed. By building the system with PLCs, it can be maintained by on-site production engineers who are already familiar with using the components to operate and maintain production equipment. This improves flexibility and allows system improvements at any time. Utilizing general-purpose products and technology also has the advantage of reducing the cost of the system.
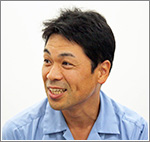
Atsushi Kojima, Environmental Promotion Section, Production System Promotion Department, Nagoya Works
Program modules jointly developed with the Air Conditioning Division
However, PLCs are intended for use with production equipment, so it is complex task to have them deliver the same functionality as a dedicated air conditioning controller. Consequently, the working group overseeing the introduction of the e-F@ctory concept at the E4 Building collaborated with Mitsubishi Electric’s Air-Conditioning & Refrigeration Systems Works to equip the PLCs with a program for air conditioning control. This delivered functionality equivalent to a dedicated controller.
The Air-Conditioning & Refrigeration Systems Works, a development center for commercial air conditioning systems, has a high level of technical expertise. Leveraging this, they jointly developed a program allowing precise air conditioning system control with general-purpose PLCs.
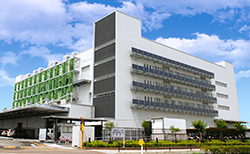
Mitsubishi Electric Air-Conditioning & Refrigeration Systems Works
Providing only the necessary brightness
PLCs also provide precise control for lighting, another important area for energy saving. Lights are turned on and off, with brightness controlled from a PLC via a gateway installed between it and the lighting equipment. The controllers are equipped with a specially developed lighting program, similar to its air conditioning equivalent. Sensors in each area of the building detect the ambient brightness and provide the necessary levels of light.
Within the E4 Building, which manufactures PLCs and other equipment, different brightness levels are required depending on the work performed in each area. The lighting gateway calculates how much light is needed, taking external sources into account, and only the necessary amount is provided, minimizing power consumption.
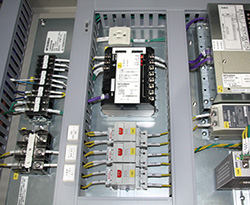
Lighting control panel. The lighting control gateway is located in the center.
“Because of the way lighting is controlled, we can get information for each area and turn it on and off from the HMI that is connected to the PLC. This data is also collected by a central controller and can be used to indicate areas for improvement,” says Masato Hibi of the Sales Engineering Division, Central Facilities Department, Mitsubishi Electric Building Techno Service, who designed the system. As a result, lighting is another area where the e-F@ctory approach has enabled visualization and ongoing improvements.
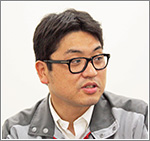
Masato Hibi, Sales Engineering Section, Central Facilities Department, Mitsubishi Electric Building Techno Service
Pursuing even greater energy efficiencies
The team is currently in the process of collecting and analyzing data on the energy savings that have been realized by the implementation of e-F@ctory technologies at the E4 Building. Power consumption is already estimated to have been reduced by around 10% by using PLCs for precise control.
Along with the integration of PLCs, motors in the external air conditioning units have been replaced with energy-efficient premium IPM motors that feature high-efficiency top-runner transformers, delivering further power savings. An estimated 30% reduction in energy usage has been achieved due to these combined measures.
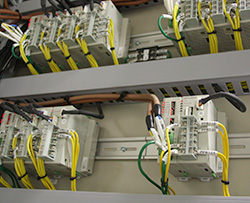
Energy saving effects are verified with the EcoMonitorPro energy measurement unit
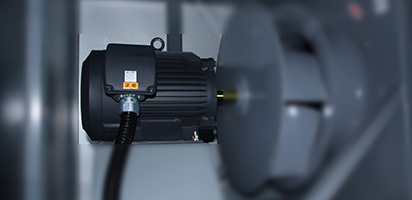
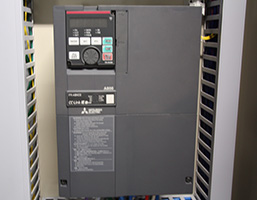
Energy-efficient equipment includes premium high-efficiency IPM motors in external air conditioning units (Left) and CC-Link IE compatible FR-F800 inverters (Right)
Improvements are ongoing at the E4 Building, as the team trials various new techniques in pursuit of even greater energy efficiency. This involves verifying different approaches and then implementing effective methods in the live system. Because the production engineers are familiar with PLCs, they can modify the setup themselves as required, which is a huge advantage in terms of achieving continuous energy savings.
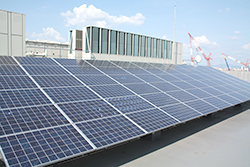
Sunlight is actively incorporated as an energy source in the E4 Building