Low cost traceability system with general-purpose software improves productivity
First released March 2020
The Mitsubishi Electric Nakatsugawa Works Iida Factory is a production base for domestic ventilation fans and motors. The factory has achieved exacting quality standards, thanks to a traceability system that automatically collects equipment information at each step of the manufacturing process and then registers it in a database. This system is also used for production progress management, worker notifications, and process improvement via data analysis. It is built and operated using familiar spreadsheet software and free business intelligent (BI) tools, resulting in a cost-effective solution with excellent return on investment.
Key points of this case study
- 1. Traceability system automatically registers data from production line equipment to the database
- 2. An alert is issued when a quality issue occurs, helping to minimize downtime
- 3. System built and operated at low cost using general-purpose spreadsheet software and free BI tools
Introduction to the Mitsubishi Electric Nakatsugawa Works, Iida Factory
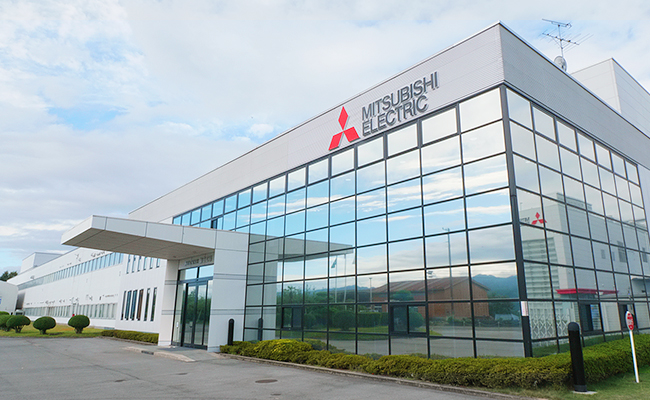
The Iida Factory is a production base for domestic ventilation fans, a core product of Nakatsugawa Works
The Iida Factory at the Nakatsugawa Works performs the complete production process for domestic ventilation fans, from component manufacturing to assembly. The motor inside a ventilation fan requires millimeter-precision processing for parts like the iron core and shaft. Some motors require even greater accuracy of 0.01 mm.
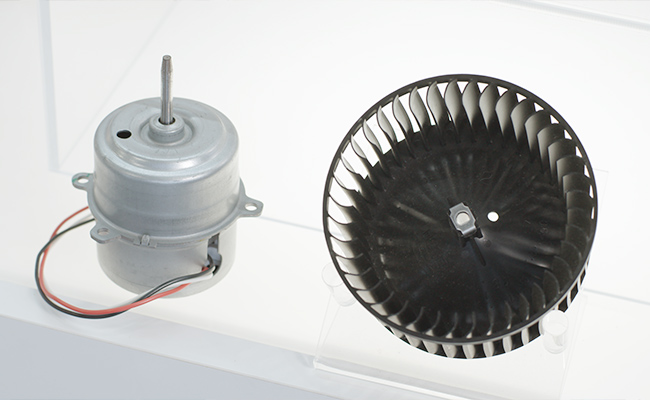
The Iida Factory at the Nakatsugawa Works manufactures ventilation fans and motors
At the Iida Factory, in addition to measuring the dimensions of components and detecting equipment errors, traceability was achieved using QR codes. Processing and measurement data from each piece of equipment in the production line is collected by PLCs and automatically sent from the MES Interface Unit to the database, allowing central management. When a quality issue occurs, an alert is immediately sent to the shop floor supervisor’s wearable device. In this way, the system helps to minimize downtime.
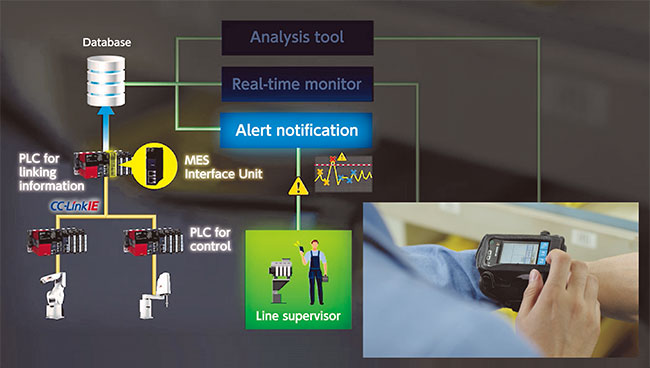
Errors are quickly detected based on information from equipment, and alerts are sent to wearable devices
A key feature of this system is that it uses general-purpose software for production progress monitoring and data analysis. Processing and measurement data from each piece of equipment are registered in the database via the PLC and MES interface unit. Using general-purpose spreadsheet software, the team at the Iida Factory developed a system to acquire data on equipment and production status, so only the necessary information is monitored.
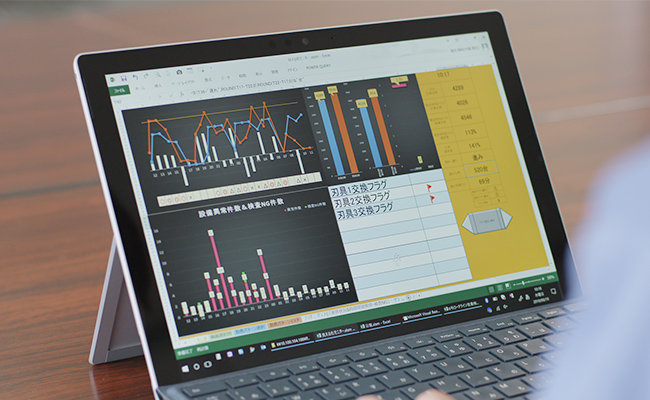
Monitoring and alert system developed with general-purpose spreadsheet software
The system for sending alerts was also developed in-house by Mitsubishi Electric using an add-on to the general-purpose spreadsheet software. This enables operators to make data driven decisions on when to replace jigs, or monitor signs of failure, without learning to use expensive dedicated software. Using a general-purpose solution also meant that the system could be designed with a view to rolling it out to other processes.
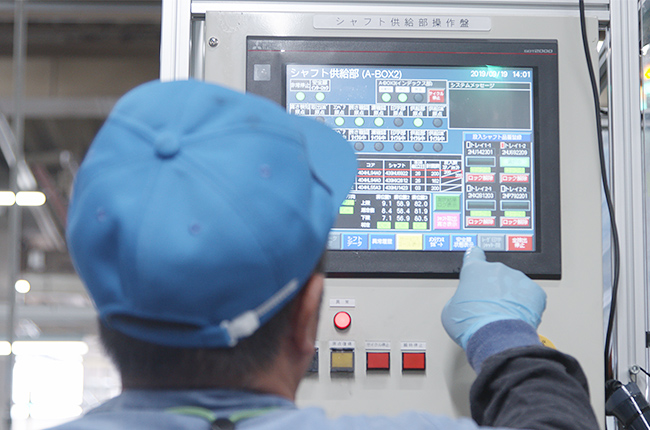
Alert system developed using spreadsheet software
Reducing cycle times using free BI tools
The Iida Factory also uses free BI tools as analysis software to reduce cycle times. A huge amount of data is created from each step in the manufacturing process for around 4,000 products, including the cycle time of each unit, the number of cycles, time required to change between lots, and so on. Collecting this data, then accessing and analyzing it with BI tools, allows the team to identify factors which could extend cycle times, so that improvements can be made. The challenging task of efficiently extracting the critical information needed from a mountain of data can now be achieved at a lower cost.
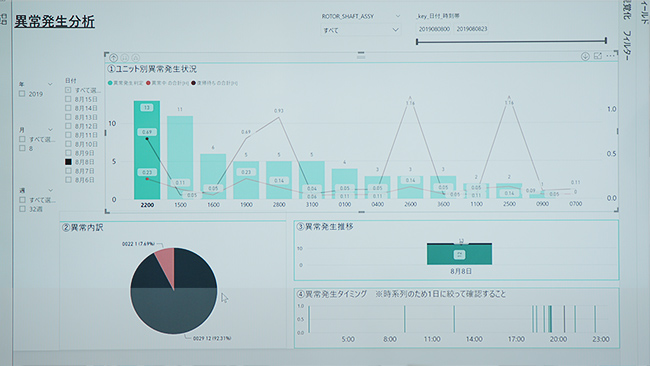
Free BI tools used as analysis software to reduce cycle times
Going forward, the Iida factory aims to move from ‘visualization’ to a system that can diagnose issues and suggest targeted actions. As the next step in leveraging the available data, the goal is to progress from only analyzing the metrics to the automatic control of equipment.