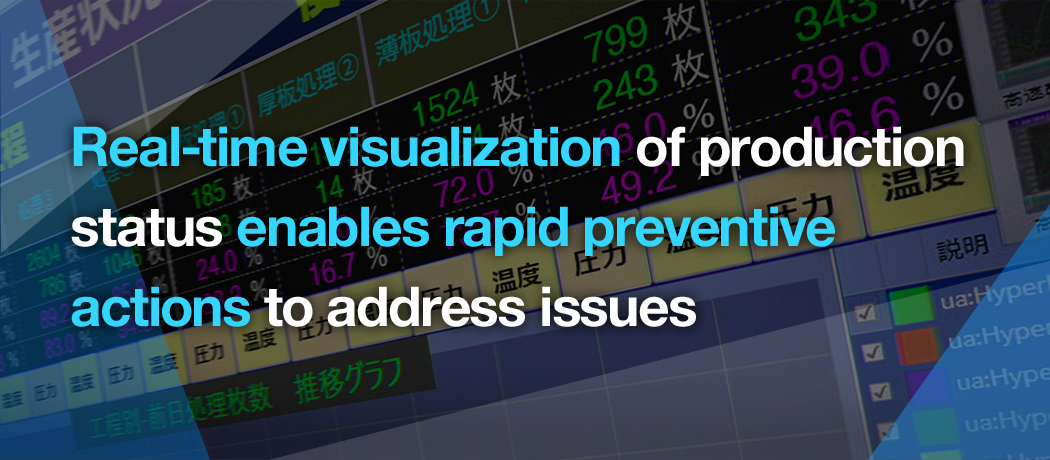
First released March, 2024
Lincstech visualized its real-time production status using Mitsubishi Electric’s GENESIS64™ SCADA software.
Printed wiring board manufacturer Lincstech Co., Ltd., part of Hitachi Chemical Company, Ltd. (now since 2023, Resonac Corporation), introduced Mitsubishi Electric’s SCADA solution GENESIS64™ to visualize the production status at its Shimodate Plant in Chikusei city, Ibaraki prefecture, Japan. As well as providing real-time monitoring to enable predictive maintenance, the deciding factor in the selection of this platform was that GENESIS64™ allowed the team at Lincstech to build and customize their own control system to the company’s operational requirements.
Key Points:
- 1. Lincstech’s Shimodate Plant implemented real-time monitoring of its production status, which previously was a manual operation.
- 2. Highly flexible software allowed the plant to build and run its own control system.
- 3. By monitoring pH levels of wastewater, measures can be proactively taken before issues arise.
Lincstech Co., Ltd., Shimodate Plant
Hitachi Chemical Company, Ltd. first started producing printed wiring boards in 1964, and now, since 2021, operates independently as Lincstech Co., Ltd. manufacturing a wide range of products, from ultra-multilayer to ultra-thin substrates.
The company has also developed its own unique technology, the “Multi-wire Board,” which uses copper wire to achieve high-density wiring through cross-linking. By supplying reliable, high-performance wiring boards to sectors including smartphones, automotive and robotics, the company is committed to bringing added value to such manufacturers.
In a drive to shorten lead times, the company has been working to visualize its production status. Previously, operational data was collected from machines by scanning work slips as each task was completed on site. However, manually compiling data one day at a time did not provide sufficient information to understand the production status in detail.
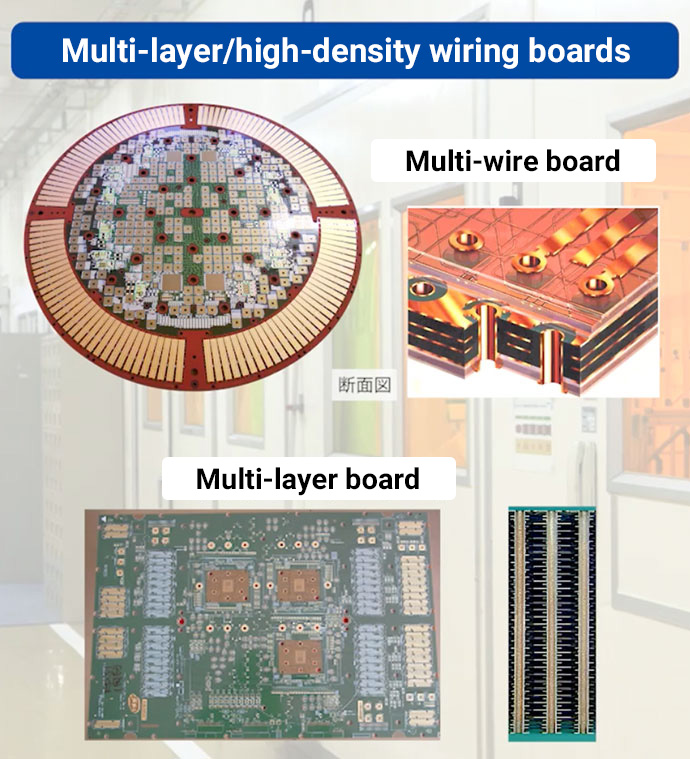
Lincstech manufactures multi-layer and high-density wiring boards for manufacturers of smartphones, vehicles, and robots
“We want to build our own visualization platform and enhance
our in-house skills.”
In 2017, as solutions based on the Industrial Internet of Things (IIoT) gained momentum throughout the company, Lincstech decided to update the workflows at its Shimodate Plant using digital technologies. One aspect of this was introducing SCADA to visualize production information. After reviewing proposals from several vendors, Lincstech selected Mitsubishi Electric’s GENESIS64™. The factory was already using Mitsubishi Electric’s PLCs, so compatibility with this system was one important reason, but the deciding factor was the ability for the company to build and operate its own control system.
“We could have simply subcontracted everything to an integrator, from the development to the implementation of the system, but it would have been difficult for a third party to understand and meet our specific requirements. However, if the system failed to align with our requirements, it's likely that we would not have utilized it. That is why we wanted to build it ourselves, and at the same time enhance our in-house skills. GENESIS64™ allowed us to do that,” explains Hideaki Kawashima, General Manager of Facilities Section, Technical Division at the Shimodate Plant.
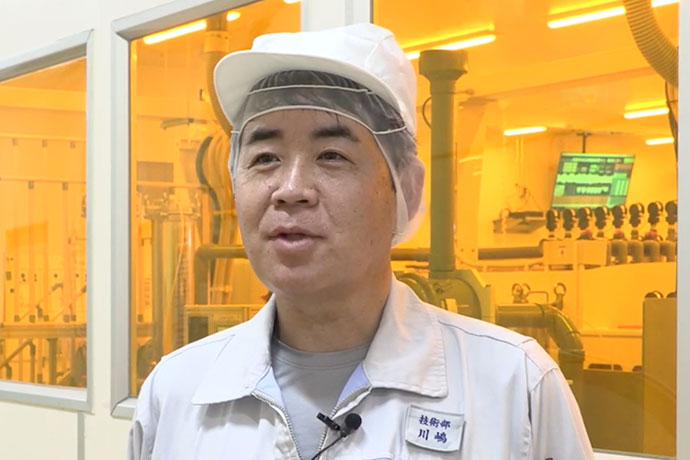
Hideaki Kawashima, General Manager of Facilities Section, Technical Division at Lincstech Co., Ltd. Shimodate Plant
In contrast with other SCADA systems that require installation in combination with hardware, GENESIS64™ can function as a stand-alone software solution. This means it is possible to start small, without requiring a major initial investment. “It may have taken some additional time for our in-house team, but I think it was good that we could install and run it ourselves, trying out different ideas,” says Naoyuki Matsumoto, Senior Engineer in the Facilities Section, Technical Division at the Shimodate Plant.
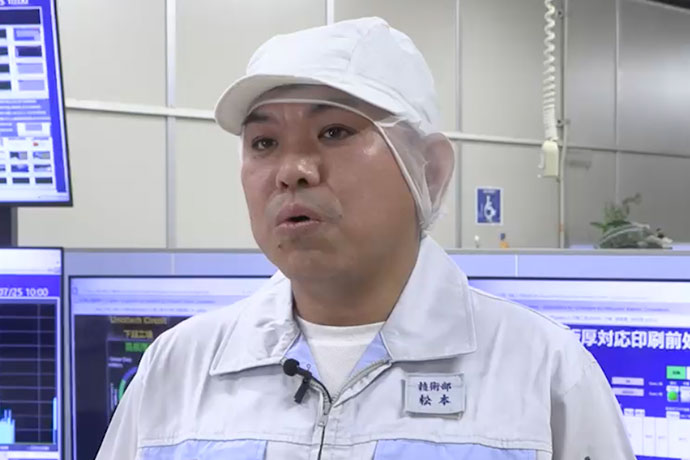
Naoyuki Matsumoto, Senior Engineer, Facilities Section, Technical Division, at Lincstech Co., Ltd. Shimodate Plant
“I can develop a dashboard screen in a single day.”
The project to visualize the production status using GENESIS64™ began in 2018. As well as two software development engineers based at the facility, the project team included engineers from other factories, with the goal of rolling out the system throughout the company. The overall aim was to build an integrated monitoring system to collect information from on-site equipment.
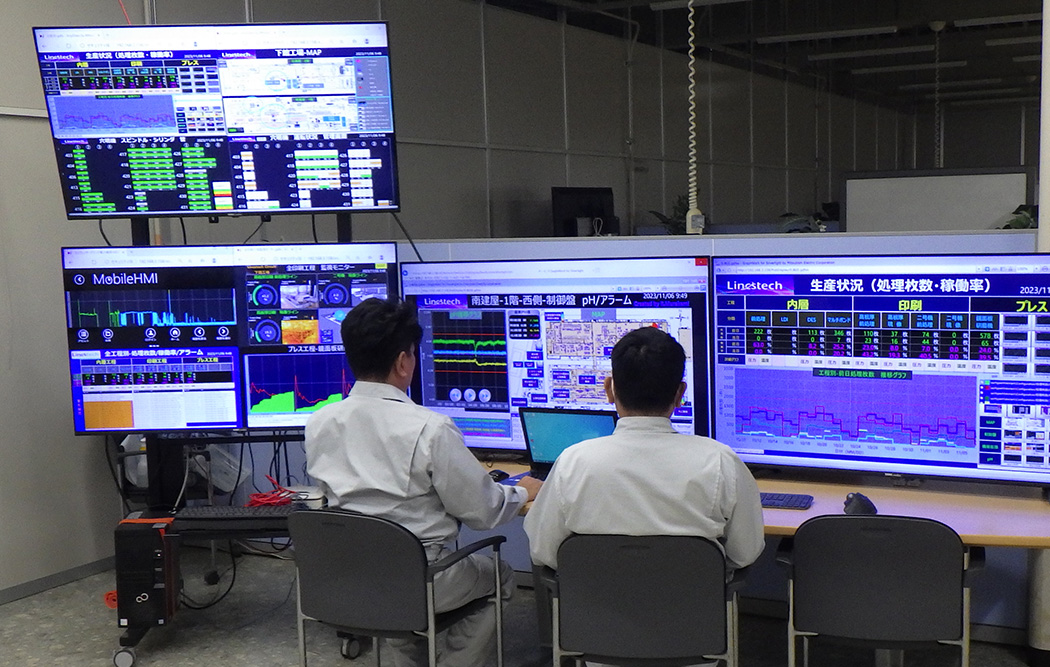
Lincstech used GENESIS64™ to develop its own dashboards and screens
The production lines at the Shimodate Plant were already equipped with numerous sensors and meters to control production quantity and quality, however, these were solely intended for visual monitoring by operators on site. As part of the project, these instruments were substituted with devices that had additional digital outputs, enabling the collection and logging of their data by PLCs.
When using a SCADA system such as GENESIS64™, it is important to design dashboards and screens so that they are intuitive and easy-to-understand. By deciding to develop the system by themselves, the team at the Shimodate Plant also took the design and development tasks in-house, too. Tsuneo Kato, an engineer from the Facilities Section, was responsible for the development. “There is a high degree of flexibility in screen design, making it simple to create your own dashboards. I can now develop a dashboard screen in a single day,” he says. GENESIS64™ includes wide-area monitoring functions that can utilize maps, and if combined with data such as the production status or alarms, easy-to-understand visuals can be created. “By using CAD data of the factory layout, we were able to create screens that met our requirements,” says Kato.
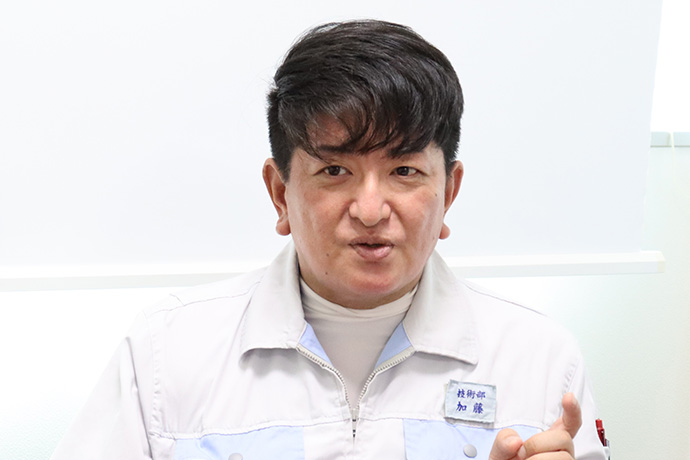
Tsuneo Kato, Engineer, Facilities Section, Technical Division, at Lincstech Co., Ltd. Shimodate Plant
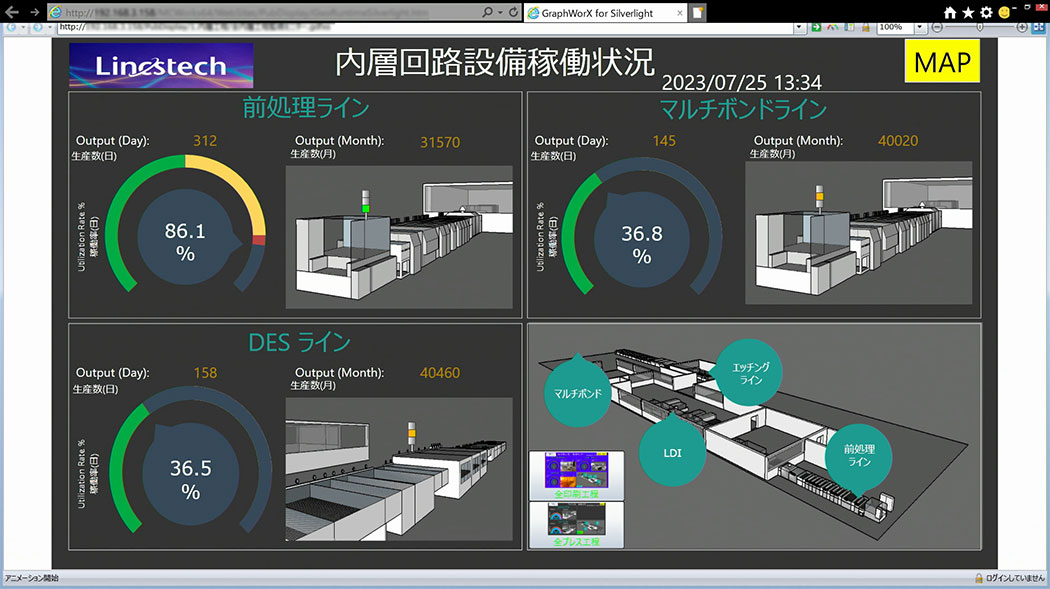
By integrating factory layout data into the dashboards, visually intuitive and easy-to-understand screens were created.
Helping to improve on-site work efficiency
Through a process of continuous improvement visualizing the Shimodate Plant using GENESIS64™ has delivered highly customized results. One of the main benefits is the company’s ability to manage the quality of wastewater discharged from the factory. It is important to control the pH value of the wastewater to minimize the environmental impact of industrial operations. Previously, alerts were only issued when the pH exceeded the pre-set threshold value, but with GENESIS64™, the pH values are monitored in real time and tracked. “We now set alarm points before the pH reaches the threshold value, produce graphs showing the changes in the pH value over time, and display trends on a screen in real-time. As a result, preventative measures can be swiftly implemented to avoid reaching the threshold, And in the event of a problem, we can use the collected historical data from the database to help us investigate what went wrong,” explains Kato.
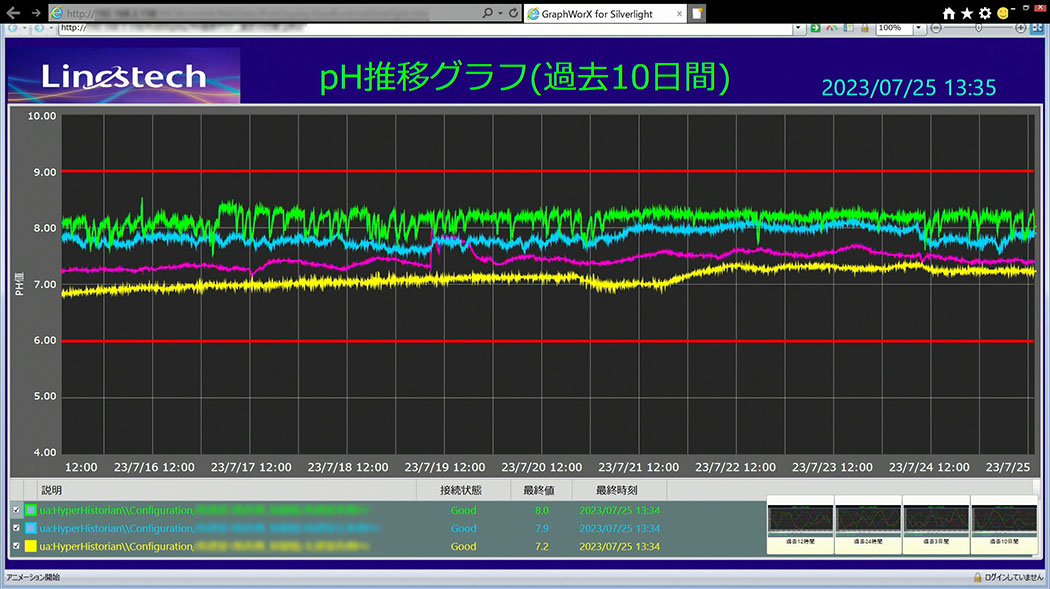
Screen showing the pH of wastewater over time. Any potential anomaly can be quickly spotted.
Another major advantage is the ability to check data from anywhere. The Shimodate Plant has several cleanrooms for manufacturing precision parts. Previously, staff working in these facilities would have to leave them to check the status of equipment located outside the cleanroom, however, now, monitors displaying GENESIS64™ screens have been installed inside these workspaces. “We can check the operation status of equipment from inside the cleanroom, which has improved work efficiency,” says Ryuichi Murakami of the Manufacturing Division at the Shimodate Plant. Monitors strategically placed in the corridors connecting buildings help create an environment where data can be checked from anywhere, resulting in faster response times – another important benefit.
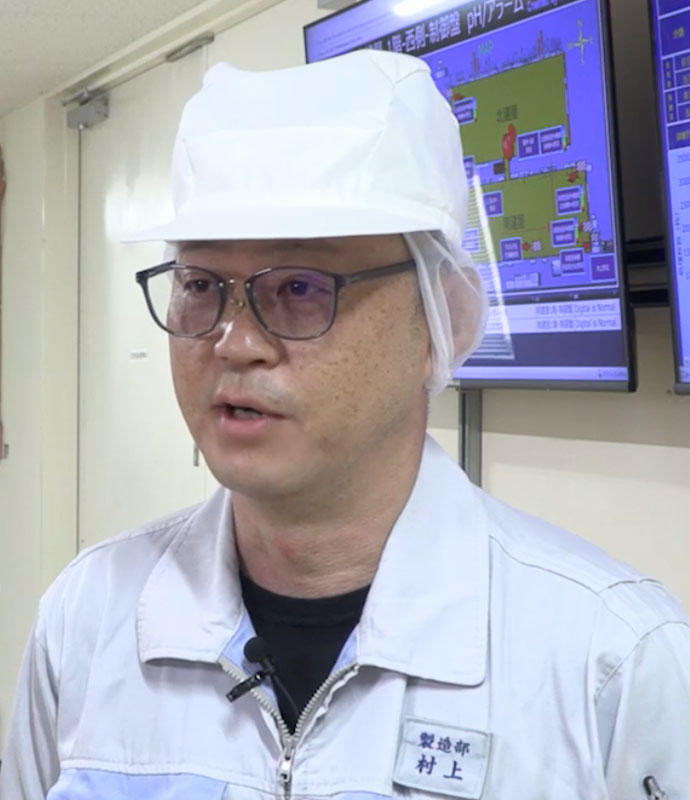
Ryuichi Murakami, Manufacturing Division, Shimodate Plant
At present, data visualization using GENESIS64™ is focused on the operating status of equipment, but there are plans to expand the scope to include electricity, water, steam, and air. “We will continue to develop our skills in applying SCADA so that we can add more on-site data targets and leverage the resulting insights to improve our manufacturing capabilities even further,” explains Kawashima.
Products and Solutions
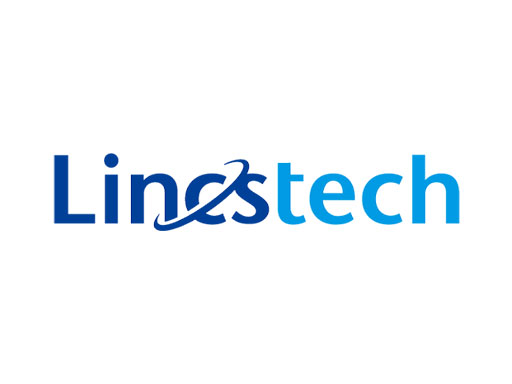
Lincstech Co., Ltd.
- Founded: 1964
- Business: Manufacture & sales of printed wiring boards
- URL : https://www.lincstech.com/english/