AC Servos-MELSERVOMR-J5-G-RJ CC-Link IE TSN Interface 200 V Specifications
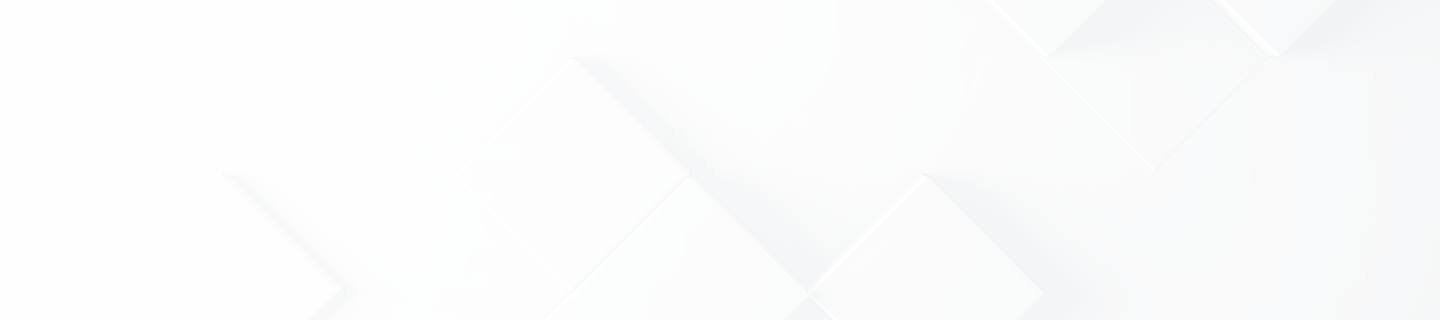
Specifications
Series | ||
Power class | ||
Model name | ||
Capacity [kW] | ||
Command interface*18 | ||
Output | Voltage | |
Rated current [A] | ||
Main circuit power supply input | Voltage/frequency*1 | AC input |
DC input*8 | ||
Rated current [A]*6 | ||
Permissible voltage fluctuation | AC input | |
DC input*8 | ||
Permissible frequency fluctuation | ||
Control circuit power supply input | Voltage/frequency | AC input |
DC input*8 | ||
Rated current [A] | ||
Permissible voltage fluctuation | AC input | |
DC input*8 | ||
Permissible frequency fluctuation | ||
Power consumption [W] | ||
Interface power supply | ||
Control method | ||
Permissible regenerative power*2 *3 | Built-in regenerative resistor [W] | |
Dynamic brake*4 | ||
Command communication cycle | ||
Communication function | ||
Encoder output pulse | ||
Analog monitor | ||
Positioning mode*5 *12 | ||
Fully closed loop control*5 *12 | ||
Load-side encoder interface | ||
Servo functions | ||
Protective functions | ||
Safety sub-function | ||
Safety performance | Satisfied standards*15 | |
Mean time to dangerous failure (MTTFd) | ||
Diagnostic coverage (DC) | ||
Probability of dangerous Failure per Hour (PFH) | ||
Mission time (TM)*16 | ||
Satisfied standards | ||
Structure (IP rating) | ||
Close mounting | 3-phase power supply input | |
1-phase power supply input | ||
Environment | Ambient temperature | Operation |
Transportation | ||
Storage | ||
Ambient humidity | ||
Ambience | ||
Altitude/atmospheric pressure | Operation | |
Transportation | ||
Storage | ||
Vibration resistance | Operation | |
Transportation | ||
Storage | ||
Mass [kg] |
MELSERVO-J5 series |
|||||||||
200 V AC |
|||||||||
0.1 |
0.2 |
0.4 |
0.6 |
0.75 |
1 |
2 |
3.5 |
5 |
7 |
CC-Link IE TSN |
|||||||||
3-phase 0 V AC to 240 V AC |
|||||||||
1.3 |
1.8 |
2.8 |
3.2 |
5.8 |
6.0 |
11.0 |
17.0 |
28.0 |
37.0 |
3-phase or 1-phase 200 V AC to 240 V AC, 50 Hz/60 Hz |
3-phase or 1-phase 200 V AC to 240 V AC, 50 Hz/60 Hz*7 |
3-phase 200 V AC to 240 V AC, 50 Hz/60 Hz |
|||||||
283 V DC to 340 V DC |
|||||||||
0.9 |
1.5 |
2.6 |
3.2 |
3.8 |
5.0 |
10.5 |
16.0 |
21.7 |
28.9 |
3-phase or 1-phase 170 V AC to 264 V AC |
3-phase or 1-phase 170 V AC to 264 V AC*7 |
3-phase 170 V AC to 264 V AC |
|||||||
241 V DC to 374 V DC |
|||||||||
±5 % maximum |
|||||||||
1-phase 200 V AC to 240 V AC, 50 Hz/60 Hz |
|||||||||
283 V DC to 340 V DC |
|||||||||
0.2 |
0.3 |
||||||||
1-phase 170 V AC to 264 V AC |
|||||||||
241 V DC to 374 V DC |
|||||||||
±5 % maximum |
|||||||||
30 |
|||||||||
24 V DC ± 10 % (required current capacity: 0.3 A (including CN8 connector signals)) |
|||||||||
Sine-wave PWM control/current control method |
|||||||||
- |
10 |
30 |
100 |
130 |
170 |
||||
Built-in |
|||||||||
· CC-Link IE TSN Class B*13 Communication cycle*10*12: 31.25 μs, 62.5 μs, 125 μs, 250 μs, 500 μs, 1 ms, 1.5 ms, 2 ms, 2.5 ms, 3 ms, 3.5 ms, 4 ms, 4.5 ms, 5 ms, 5.5 ms, 6 ms, 6.5 ms, 7 ms, 7.5 ms, 8 ms Protocol version: 1.0/2.0*5 · CC-Link IE TSN Class A*5*13*17 Communication cycle*10: 500 μs to 500 ms Protocol version: 2.0 |
|||||||||
USB: Connect a personal computer (MR Configurator2 compatible) |
|||||||||
Compatible (A/B/Z-phase pulse) |
|||||||||
2 channels |
|||||||||
Point table method |
|||||||||
Two-wire/four-wire type communication method |
|||||||||
Mitsubishi Electric high-speed serial communication, A/B/Z-phase differential input signal |
|||||||||
Advanced vibration suppression control II, adaptive filter II, robust filter, quick tuning, auto tuning, one-touch tuning, tough drive function, drive recorder function, machine diagnosis function (including failure prediction), power monitoring function, lost motion compensation function, scale measurement function*5*12, super trace control*5, continuous operation to torque control mode*5*12, driver communication function*5*12 |
|||||||||
Overcurrent shut-off, regenerative overvoltage shut-off, overload shut-off (electronic thermal), servo motor overheat protection, encoder error protection, regenerative error protection, undervoltage protection, instantaneous power failure protection, overspeed protection, error excessive protection, magnetic pole detection protection, linear servo control fault protection |
|||||||||
Refer to "Safety Sub-Functions" for safety sub-functions. |
|||||||||
EN ISO 13849-1:2015 Category 4 PL e, IEC 61508 SIL 3, EN IEC 62061 maximum SIL 3, EN 61800-5-2 |
|||||||||
MTTFd ≥ 100 [years] (750a) |
|||||||||
DC = Medium, 96.5 % |
|||||||||
PFH = 3 × 10-9 [1/h] |
|||||||||
TM = 20 [years] |
|||||||||
Refer to "Standards and certifications (by product) Products" for compliance with global standards and regulations. |
|||||||||
Natural cooling, open (IP20) |
Force cooling, open (IP20) |
Force cooling, open (IP20)*9 |
|||||||
Possible*11 |
|||||||||
Possible*11 |
Not possible |
- |
|||||||
0 °C to 60 °C (non-freezing), Class 3K3 (IEC 60721-3-3) |
|||||||||
-25 °C to 70 °C (non-freezing), Class 2K12 (IEC 60721-3-2) |
|||||||||
-25 °C to 70 °C (non-freezing), Class 1K4 (IEC 60721-3-1) |
|||||||||
5 %RH to 95 %RH (non-condensing) |
|||||||||
Indoors (no direct sunlight); no corrosive gas, inflammable gas, oil mist or dust |
|||||||||
Altitude: 2000 m or less*14 |
|||||||||
Overland/sea transportation, or transporting on an airplane whose cargo compartment is pressurized at 700 hPa or higher |
|||||||||
Atmospheric pressure: 700 hPa to 1060 hPa (Equivalent to altitudes from -400 m to 3000 m) |
|||||||||
Under intermittent vibration: 10 Hz to 57 Hz, displacement amplitude 0.075 mm 57 Hz to 150 Hz, acceleration amplitude 9.8 m/s2 Class 3M1 (IEC 60721-3-3) Under continuous vibration (directions of X, Y, and Z axes): 10 Hz to 55 Hz, acceleration amplitude 5.9 m/s2 |
|||||||||
2 Hz to 9 Hz, displacement amplitude (single amplitude) 7.5 mm 9 Hz to 200 Hz, acceleration amplitude 20 m/s2 Class 2M3 (IEC 60721-3-2) |
|||||||||
2 Hz to 9 Hz, displacement amplitude (single amplitude) 1.5 mm 9 Hz to 200 Hz, acceleration amplitude 5 m/s2 Class 1M2 (IEC 60721-3-1) |
|||||||||
0.8 |
1.0 |
1.4 |
2.2 |
3.7 |
6.2 |
(*1)Rated output and speed of a rotary servo motor and a direct drive motor; and continuous thrust and maximum speed of a linear servo motor are applicable when the servo amplifier is operated within the specified power supply voltage and frequency.
(*2)Select the most suitable regenerative option for your system with our drive system sizing software Motorizer.
(*3)Refer to "Regenerative Option" in "MELSERVO-J5 catalog" for the permissible regenerative power [W] when a regenerative option is used.
(*4)When using the dynamic brake, refer to "MR-J5 User's Manual" for the permissible load to motor inertia ratio and the permissible load to mass ratio.
(*5)For the servo amplifier firmware version supporting this function, refer to "MR-J5 User's Manual".
(*6)This value is applicable when a 3-phase power supply is used.
(*7)When the servo amplifier is used with a 1-phase power supply and combined with a servo motor of over 750 W, use the servo amplifiers at 75 % or less of the effective load ratio.
(*8)For a connection example of power supply circuit with DC input, refer to "MR-J5 User's Manual".
(*9)The connector part is excluded.
(*10)The communication cycle depends on the controller specifications and the number of device stations connected.
(*11)When the servo amplifiers are closely mounted, keep the ambient temperature within 0 °C to 45 °C, or use the servo amplifiers at 75 % or less of the effective load ratio.
(*12)For the restrictions on the communication cycle, refer to "Restrictions" in "MELSERVO-J5 catalog".
(*13)A communication speed of 1 Gbps/100 Mbps can be selected. When 100 Mbps is selected, the minimum communication cycle is 500 μs.
(*14)Refer to User's Manuals of each servo amplifier, drive unit, and power regeneration converter unit for the restrictions on using the servo amplifiers, the drive units, and the power regeneration converter units at an altitude exceeding 1000 m and up to 2000 m.
(*15)When DI/O connection (CN8) is used, a diagnosis using test pulses is required to meet Category 4 PL e, SIL 3.
(*16)The performance of special proof tests within the mission time of the product is regarded as not necessary, however, the diagnostic interval is suggested as at least one test per three months for Category 3 PL e, SIL 3 on IEC 61800-5-2:2016.
(*17)For the restrictions on the network, refer to "MR-J5 User's Manual".
(*18)CC-Link IE Field Network Basic is also supported. For the supported firmware version of the servo amplifier and restrictions, refer to "MR-J5 User's Manual".