Motion ControllersRD78GHV Specifications
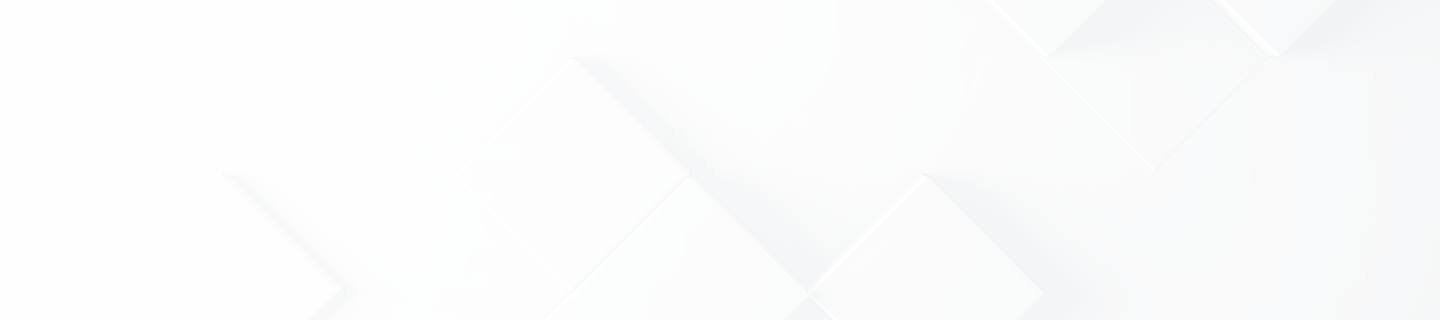
Performance specifications
[Control specifications] PLCopen® Motion Control FB Mode | |
Number of control axes | |
Operation cycle (operation cycle settings)*1 | |
Interpolation function | |
Control method | |
Acceleration/deceleration processing | |
Compensation function | |
Synchronous control | |
Control unit | |
Programming language | |
Backup | |
Home position return | |
Positioning control | |
Manual control | |
Direct control | Speed control |
Torque control | |
Absolute position system | |
Speed limit | |
Torque limit function | |
Forced stop | |
Software stroke limit function | |
Hardware stroke limit function | |
Speed change | |
Acceleration/deceleration processing change | |
Torque change function | |
Torque limit value change | |
Target position change function | |
Override | |
Event history function | |
Logging | |
Axis emulate (amplifier-less operation) | |
Touch probe (mark detection) | |
Monitoring of servo data | |
Servo system recorder function | |
CC-Link IE TSN safety communication function | |
Inter-module synchronization | |
Number of module occupied slots | |
5 V DC internal current consumption [A] | |
Servo amplifier connection method | |
CC-Link IE TSN Class | |
Number of occupied I/O points | |
Maximum distance between stations [m] | |
PERIPHERAL I/F | |
Extended memory | |
Memory capacity | Built-in memory |
SD memory card | |
Mass [kg] | |
Exterior dimensions [mm] |
Up to 128 axes |
31.25 μs, 62.5 μs, 125 μs, 250 μs, 500 μs, 1000 μs, 2000 μs, 4000 μs, 8000 μs |
Linear interpolation (up to 4 axes), 2-axis circular interpolation |
Positioning control, speed control, torque control, synchronous control, cam control |
Trapezoidal acceleration/deceleration, jerk acceleration/deceleration, acceleration/deceleration time fixed method |
Driver unit conversion |
• Module: master axis, cam, gear • Master axis: real drive axis, virtual drive axis, real encoder axis, virtual encoder axis, virtual linked axis |
Unit character string and decimal digit can be defined by users. (The following are given units: mm, inch, degree, pulse) |
• PLC CPU: ladder diagram, function block diagram/ladder diagram, structured text language • Motion module: structured text language |
Parameters and programs can be saved on a flash ROM (batteryless backup) |
Driver home position return*2 |
Linear interpolation control (up to 4 axes), 2-axis circular interpolation (border point-specified, central point-specified, radius-specified circular interpolation), speed control, current value change |
JOG operation |
Speed control not including position loop, speed control including position loop |
Torque control, continuous operation to torque control |
Provided (batteryless) |
Speed command range |
Torque limit value (positive/negative direction) |
Valid/invalid setting |
Movable range check with an address of the set position or the feed machine position. |
Provided |
Provided |
Acceleration/deceleration, acceleration/deceleration time |
Provided |
Provided |
Target position change, movement distance change |
0.00 to 10.00 (0 to 1000 %) |
Provided |
Data logging, real-time monitor |
Provided |
Provided |
Cyclic transmission, transient transmission |
Provided |
Provided |
Provided |
2 |
2.33 |
CC-Link IE TSN |
B |
48 points, 2 slots (I/O assignment: Empty 16 points + 32 points) |
CC-Link IE TSN: 100 |
Via a CPU module (USB, Ethernet) |
SD/SDHC memory card |
64 M bytes |
Up to 32 G bytes |
0.44 |
106.0 (H) x 56.0 (W) x 110.0 (D) |
(*1)The number of controllable axes varies depending on the operation cycle.
(*2)The home position return method set in a driver (a servo amplifier) is used.