Solutions
Logistics
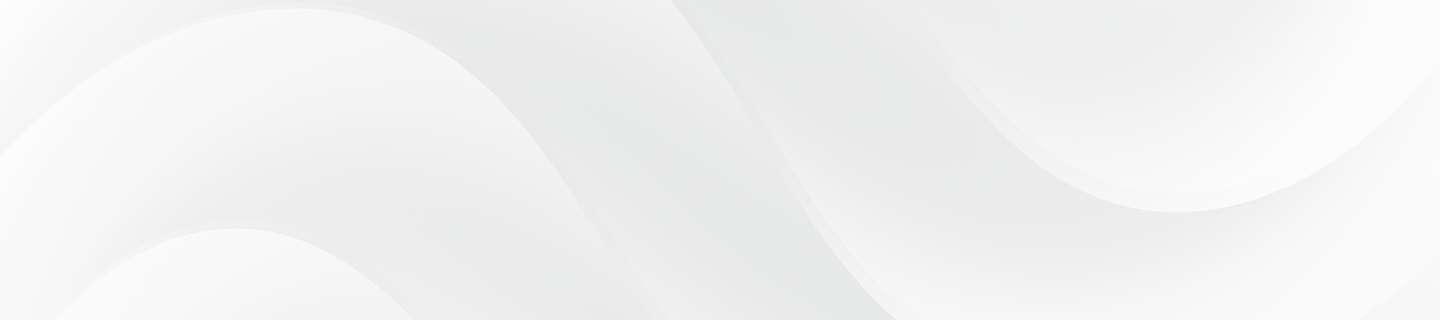
Stacker crane
Cycle time reduction and enhanced safety
- Efficient inbound/outbound logistics process
- Cost saving in design and development
- Short startup and maintenance times
- Enhanced safety
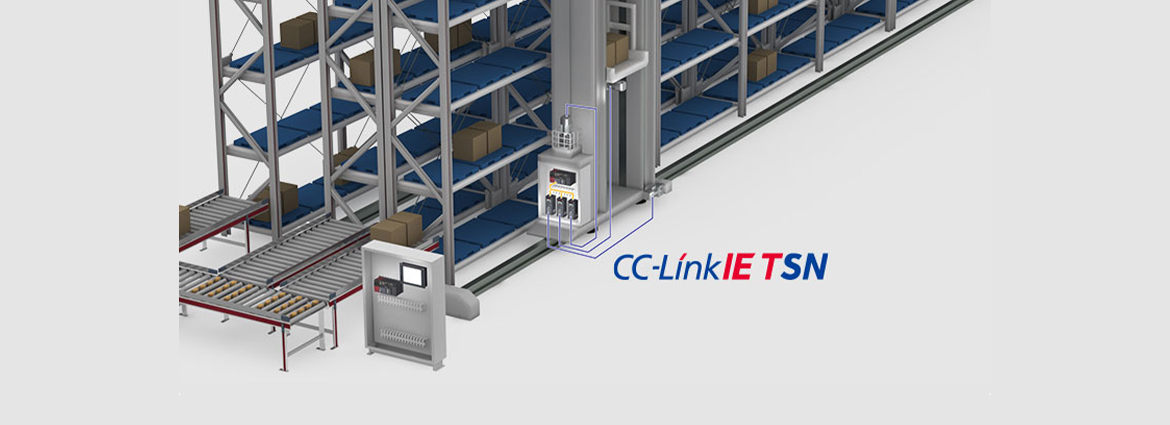
Solutions to the Issues
Issues | Solutions |
---|---|
Crane stability and high-speed operation | By vibration control, and position calibration functions faster and more stable load/unload |
Lowering engineering cost | Reduction of development cost by just setting parameters built-in inverter |
Crane fault avoidance | Using safety functions for cranes to avoid problems |
System Configuration
feature
Crane stability and high-speed operation
The position of the shuttle car is detected by a laser distance measuring device, and positioning control is performed.
Even if the condition of the machine changes, such as sliding or wear of the wheel, it can always stop at the target position accurately.
The anti-sway function minimizes the swinging of the crane frame while the shuttle car is traveling.
There is no waiting time for crane frame to stop swinging, thus the tact time is shortened.
Lowering engineering cost
The inverter itself automatically creates the operation pattern up to the stop position.
Controller programming is not required, and the processing load of the controller is reduced only by setting basic conditions for positioning in the inverter. In case of failure, positioning can be adjusted only by inverter parameters.
Crane fault avoidance
Equipped with various safety functions for stacker cranes in addition to standard inverter protection functions
Distributed safety control is possible without relying on only the PLC safety function. The operation can be stopped safely even in the event of an interruption of communication.