Solutions
Oil and Gas
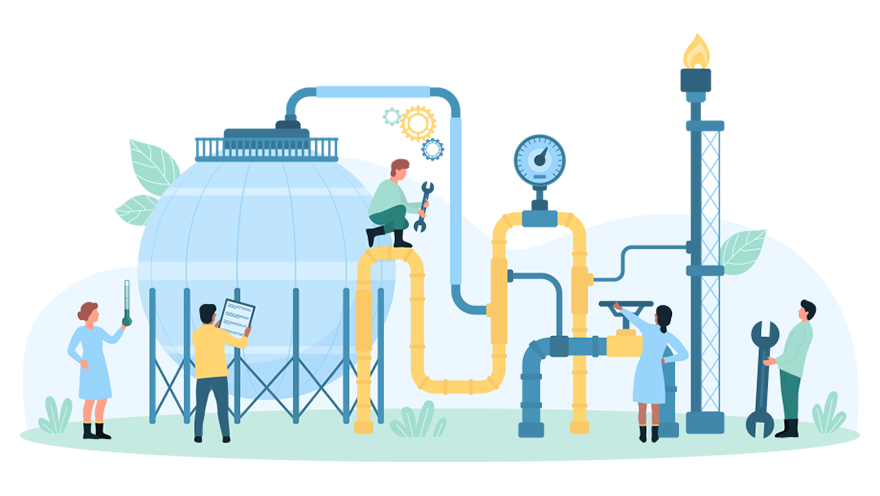
Mitsubishi Electric provides the rich functionality and proven reliability to help optimise standard automation in the oil and gas industry.
Technology for the oil and gas production and processing industry is always evolving. The same is true of Mitsubishi Electric's world-class electrical and automation products. We offer a range of technologies to help address the complex challenges faced by the industry, such as optimisation of technical processes, energy-efficiency, and increases in the level of plant automation at oil and gas facilities.
Local Automation
Local automation stations for different process units are widely used in the SCADA systems of the oil and gas industry, but the local stations, with limited number of I/O channels, are often located hundreds of kilometers away from the central control room.
Mitsubishi Electric offers an extensive lineup of equipment to provide the ideal local automation solution for a variety of needs. For example, our compact PLC for systems with limited signal scoring helps reduce system costs. We also offer highly reliable communications equipment optimized for remote monitoring.
Major Applications of Our Products:
- - Gas and oil well sites
- - Test separators
- - Chemical injection skids
- - Water intake facilities and reservoir pressure maintenance systems
- - Pump and compressor stations
- - Transformer substations
- - Independent boiler facilities
- - Controlled facilities for pipeline telemetry
- - Cathode protection stations for pipelines
Characteristics of Local Automation Stations
- - Limited number of I/O channels, usually not more than 200
- - Cost-effective hardware platform
- - Seamless integration of local control systems into host automation system and CCR by open communication protocols
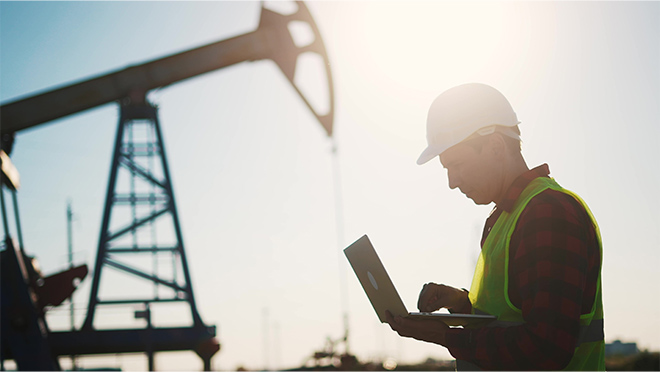
System Configuration
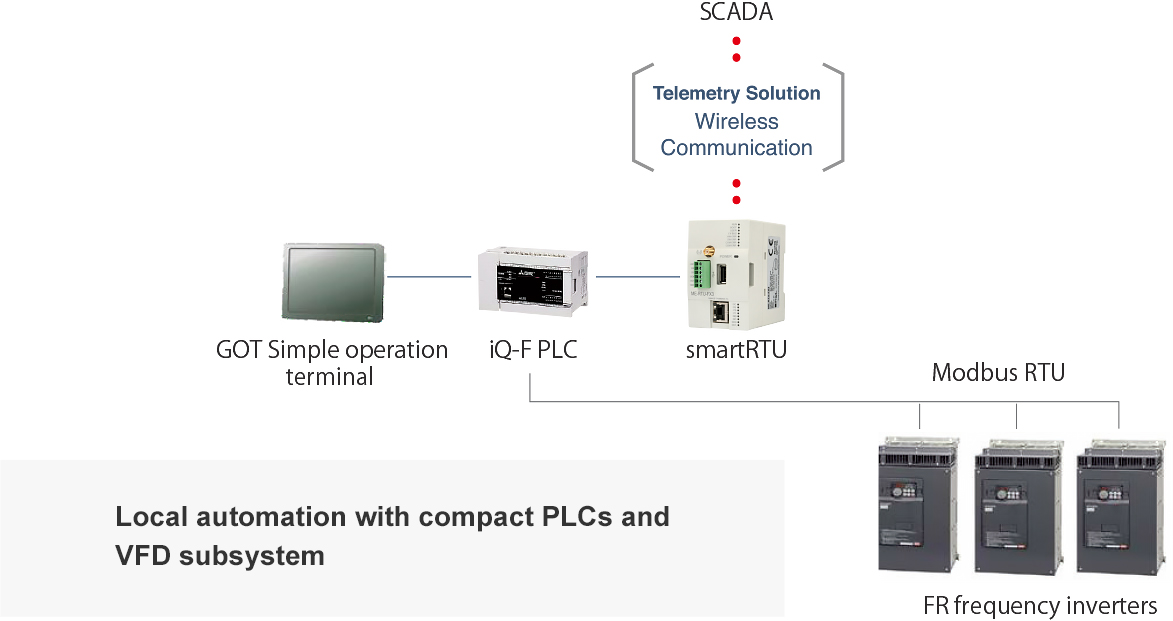
Site Automation
Oil and gas complexes contain a number of interlinked process units and stations that are located in individual processing areas. The site objects incorporate a large amount of control equipment and actuators. Their signals are routed directly to the I/O system of the central controller.
Normally, the process is continuous; therefore, the automation hardware platform must conform to high performance, scalability and reliability requirements our products meet the demands of the control system.
Major Applications of Our Products:
- - Booster pump stations
- - Initial water separation units
- - Oil treatment units
- - Central collecting stations
- - Gas treatment units
- - Oil pumping stations
- - Tank farms
- - Gas compressor stations
Characteristics of Local Automation Stations
- - Large number of I/O signals in the control system – from hundreds to thousands
- - In addition, large number of analog signals (pressure, temperature, flow and level sensors)
- - Large number of PID control loops (e.g. for level control in separators)
- - Continuous operation of the process thanks to hardware redundancy of the system elements
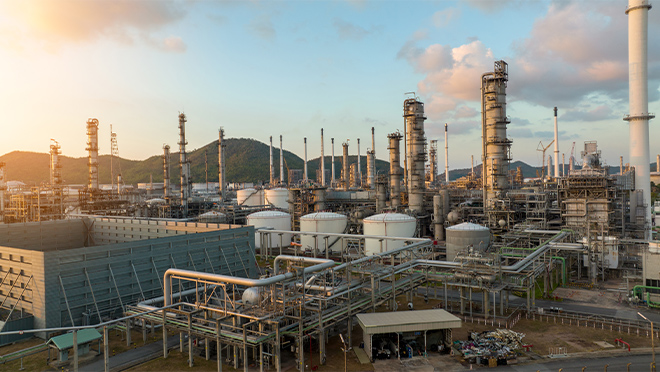
System Configuration
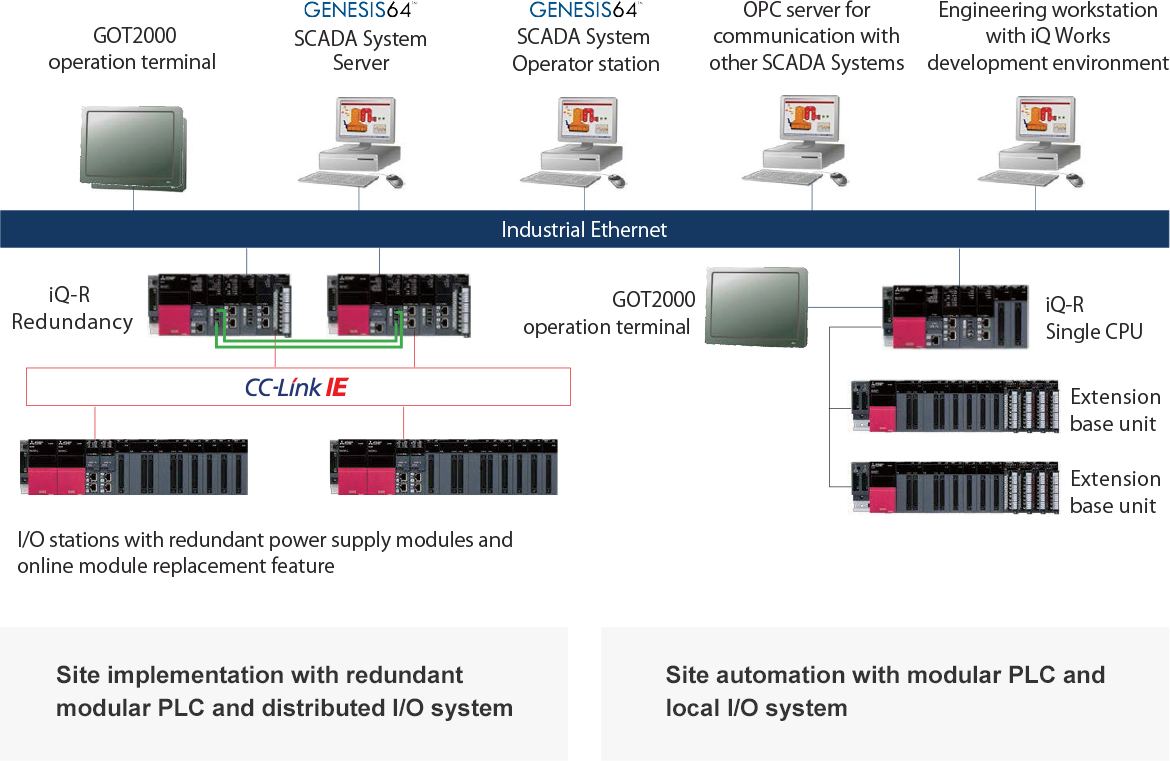
Why Mitsubishi Electric?
Mitsubishi Electric's total solutions for oil and gas offer unparalleled benefits. These advantages bring comfort andease-of-use to customers, while ensuring the smooth operation of their business.
- 1.Understanding Equipment Status
- 2.Highly Reliable Equipment
- 3.Low Energy Consumption
- 4.Monitoring of Remote Equipment
1.Understanding Equipment Status
Implementation of the right control system ensures the stability of process parameters during unloading and on-site transfers, leading to a significant reduction in the possibility of operator errors. Implementation of a modern control system permits expanded diagnostics of the equipment, as well as clear indication and recording of system failures and emergency situations. Our automation solution for storage depots has proved to be reliable, functional and universal.
2.Highly Reliable Equipment
For plants that operate for long hours, we provide high-reliability products, including redundant PLCs for critical equipment that must not stop operating. We also offer redundant PLCs that have achieved IEC 61508 SIL 2*1 international safety standard certification from TÜV Rheinland®, making it possible to build more stable and highly reliable systems.
3.Low Energy Consumption
Energy saving performance is a key factor for improving the efficiency of production equipment. We offer inverters with advanced optimum excitation control, an offline auto tuning function and similar energy-saving features to optimize the operation of pumps, compressors and other equipment. It is possible to combine them with various kinds of motor, including IPM motors, for a broad range of uses within the oil and gas industry.
4.Monitoring of Remote Equipment
Oil and gas production equipment exists in a wide area of activity, from upstream to downstream. To provide a solution, our Remote Terminal Unit allows central monitoring of scattered and distant oil wells or pipeline subsystems. Compatible with DNP3.0 and IEC60870, as well as other protocols needed when handling remote equipment, by integrating subsystems with centralized monitoring, it helps users achieve greater efficiency in remote management.