World roundup
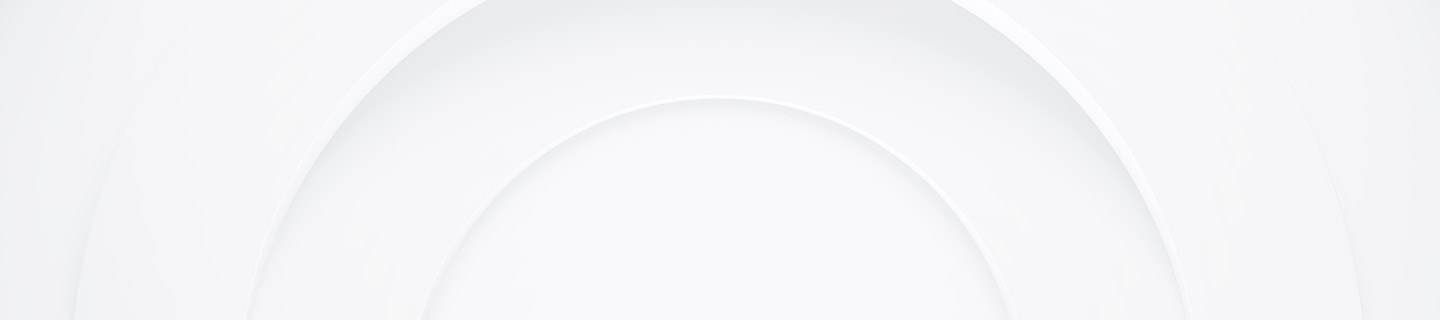
Flexible engineering to meet the demanding requirements of snack food makers.
Published in September 2024
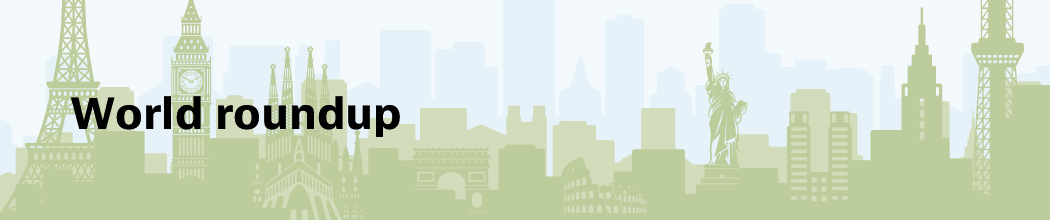
Siddhi Vinayak Agri Processing Pvt., Ltd. uses Mitsubishi Electric's FA products, such as programmable controllers, servo's and displays, to build machines and conveying systems for producing snack foods from a variety of ingredients such as pulses, maize, millet, and potato derivatives. Based in Pune, India the company is expanding its business all over the world from the United Arab Emirates to Germany and the Philippines.
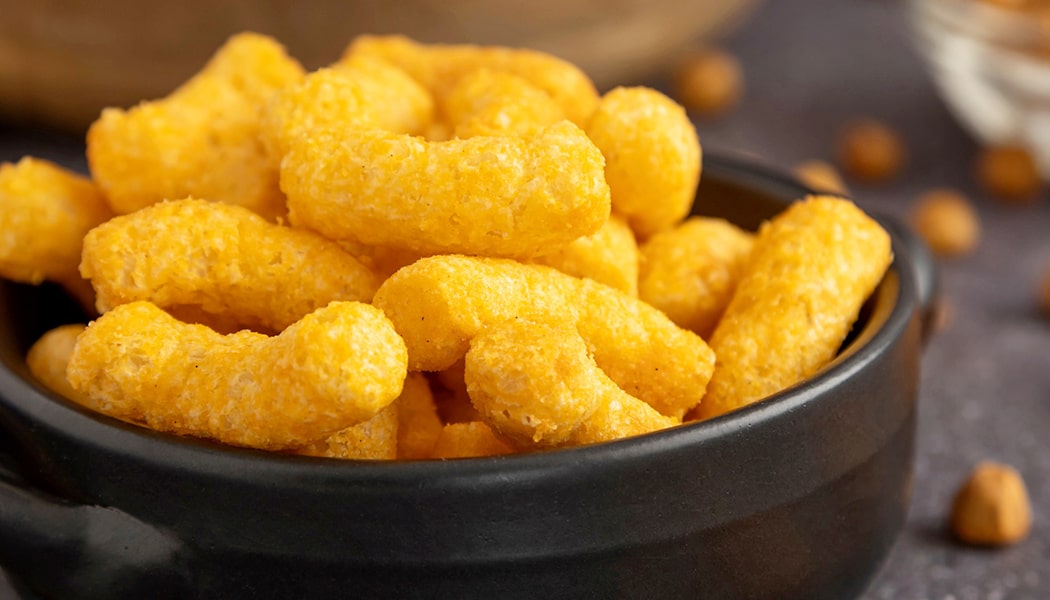
More than a supplier, a collaboration partner
Siddhi Vinayak Agri Processing Pvt., Ltd. is a multi-discipline company, comprising of agriculture support, snack production and engineering services, based in India. The company was founded in 2008, but the engineering division started operations in 2012 offering consultancy and sharing know-how with food production companies. Over time the engineering division expanded their scope to provide engineering and systems services that are focused on the snack food manufacturing industry.
Mr. Ram Manohar Singh, the head of the company’s engineering division, noted that the relationship with Mitsubishi Electric factory automation started during the COVID pandemic, when SV Agri were searching for an alternative automation supplier. Mr. Singh explained "We finally settled on Mitsubishi Electric due to its high-quality products, friendly technical support, and accurate PID control (feedback control)."
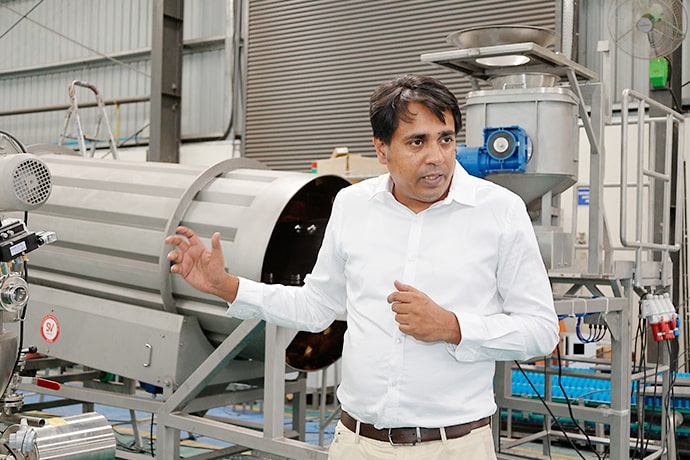
Mr. Ram Manohar Singh is head of engineering at SV Agri’s engineering division. He is passionate about snack food production.
There was a steep learning curve for SV Agri as they started to use Mitsubishi Electric's FA products. However, Mitsubishi Electric India's engineers supported them through every step, resulting in a strong bond of trust and collaboration between the two companies.
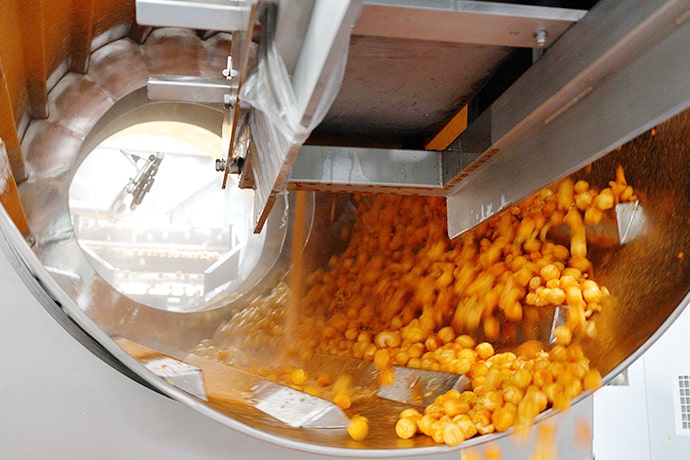
A scene capturing process control on a seasoning line. As the automatically fed extruded snacks dance in the rotating drum, the right amount of oil and seasoning are sprayed at the right time and mixed together
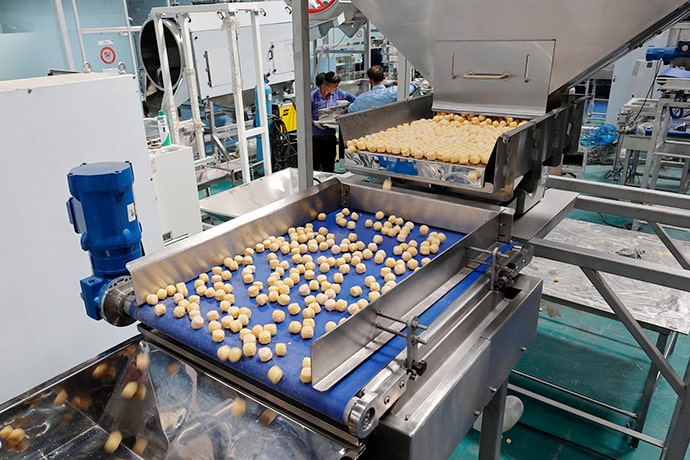
Seasoning line
Feedback control improved roast quality
Singh explained, "one of the first areas that SV Agri's engineers applied Mitsubishi Electric's controllers and interfaces on was the roasting line".
Before installation, the heating temperature of the roasting line was set at a static 100 degrees Celsius. However, this did not reflect the real operational needs which had to cope with varying production volumes from 200kg per hour to 1000kg per hour. Singh put this challenge in context, "the changing volumes can affect the roasting time and thoroughness of the applied roast."
Furthermore, a variety of ingredients also needed to be catered for as the roasting qualities and parameters for nuts are different to those of beans and pulses.
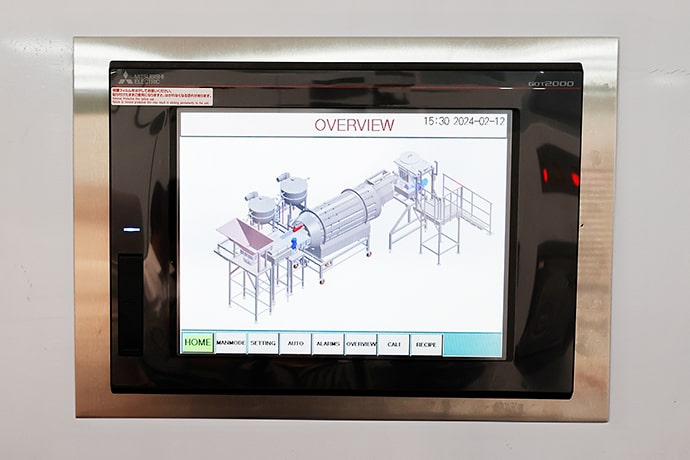
Despite the steep learning curve, the engineering team at SV Agri have put a lot of effort and diligence in creating their control systems.
The application of programmable logic controllers and servo systems have now helped overcome these issues. With a combination of research and development, automated feedback control using PID, now the roasting line can flexibly adjust timings and temperatures to deliver the perfect produce with the required color, texture, and crispiness regardless of the volume, raw material, or environmental conditions.
"Through our collaboration with Mitsubishi Electric, we could adjust the heating cycles to the required levels and provide our clients with the results they wanted, " commented Singh.
Added benefits
In addition, the new control methodology has also stabilized product quality, and lowered energy consumption, which for a roasting line is a high proportion of the operating costs. These added benefits are significant for operators in the food industry where low margins per unit produced are the norm.
The next challenge
Looking forward, Singh explained that his team was now investigating the use of robots in combination with the company’s equipment, but Mr. Singh clearly stated, "I’m looking to create a unique robot application dedicated to the needs of the snack food industry. I’m not interested in anything else, only producing snack foods."
Interview cooperation: Global Industry Solution Division
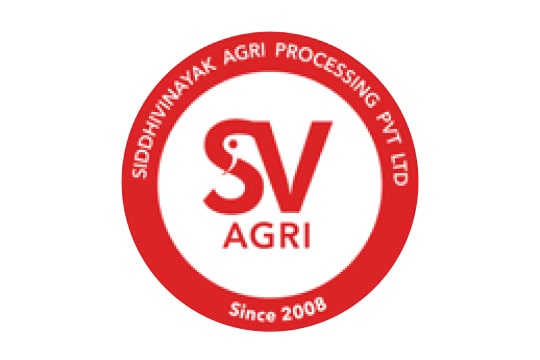
Siddhivinayak Agri Processing Pvt. Ltd.
- Founded: 2008
- Business: SV Agri engaged in manufacturing, exporting and supplying the best array of Organic Fertilizers, Heat Exchanger, Potato Seeds, Potato Starch, Dried Potato Chips, Extruder Machine, Potato Storage System, Water Treatment Plant, Bio Methanation Plant, etc.
- URL:https://www.svagri.co.in/