Reducing operating and maintenance costs to 1/6 by improving durability
First released October 2015
Not only does Mitsubishi Electric manufacture C Controllers at its Nagoya Works, it also uses them in applications throughout the facility. For example, these devices have replaced the PCs that controlled product pre-shipment testing equipment, improving durability and maintainability. This has resulted in a reduction of operating and servicing costs to 1/6 of the previous expenditure. Furthermore, this switchover has illustrated how big data can be effectively leveraged in the manufacturing industry.
Key points of this case study
- 1. Less failure response work; significantly reduced operating and maintenance costs
- 2. Factory automation (FA) equipment suitable for the production site provides long-term reliability and better resistance to environmental conditions, ensuring a stable system
- 3. Reduced wiring ensures a compact solution with a minimized footprint
Mitsubishi Electric’s Nagoya Works is a key production facility for FA products. Many of the company’s GOTs, inverters, and PLCs, including C Controllers, are assembled and shipped from here.
A manufacturing process common to all products is pre-shipment testing after assembly. Once components are mounted and assembled, every single board is thoroughly checked to make sure it functions correctly. For CPU units, there are more than 30 test items to be assessed, and these checks differ for each product, so an automated process is essential.
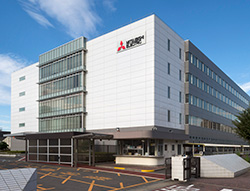
Test equipment developed in-house at the Nagoya Works and partner factories is used to achieve this. Equipment consists of a Windows-based PC and custom developed applications. Although the fundamental configuration has not changed for over twenty years, as the number of products has increased, more pieces of test equipment are required, resulting in additional system management and maintenance work.

System configuration of existing PC-based test equipment
Impossible to source the same PC
One of the main reasons behind an increased need for management and maintenance work on the test equipment was PC failure. Unlike in a normal office, computers at a production site continuously operate at high loads in a harsh environment where they are subjected to vibrations and dust. Hard disks are particularly prone to failure in these conditions. Spares are kept on site, but the test equipment must be stopped to replace the hard disk and perform start-up adjustments.
Another problem was the short product lifecycle of PCs. “It is sometimes impossible to get hold of the same PC that is currently being used, for example if the model is discontinued or the OS is no longer supported,” explains Hirofumi Kita of the Equipment Development Department, FA Manufacturing Section at the Nagoya Works. The PC does not need to be the latest model, so long as it can fulfil the specific purpose of pre-shipment testing. In fact, introducing a new PC involves extra work, such as confirming operation and so on. However, due to the short product lifecycle of PCs, there had been no choice but to introduce new models. In particular: “OS updates took as much time and effort as creating a new system,” says Kita.
The higher the variety of products manufactured at the site, the more test equipment is required, so there was a risk that these issues would continue to grow. Ultimately, that’s why the team decided to replace the PCs with C Controllers.
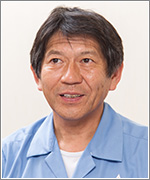
Hirofumi Kita, Equipment Development Department, FA Manufacturing Section, Nagoya Works
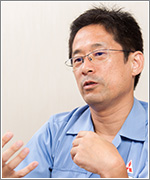
Hiroshi Kato, Equipment Development Department, FA Manufacturing Section, Nagoya Works
Seamless connection of peripheral devices
The C Controller is a CPU unit installed in the PLC base unit to enable the device to be controlled using C language. Since 2010, the Nagoya Works has been gradually replacing PCs in test equipment with C Controllers. In the conventional system, the PC was connected to a keyboard, display, printer, and LAN as well as the PLC. The LAN connects to the production control database, storing test results information from the PLC.
The C Controller can simply replace the PC in this setup. As it has USB, LAN and VGA interfaces, the same peripheral devices can be connected, with hardly any changes to the system configuration.
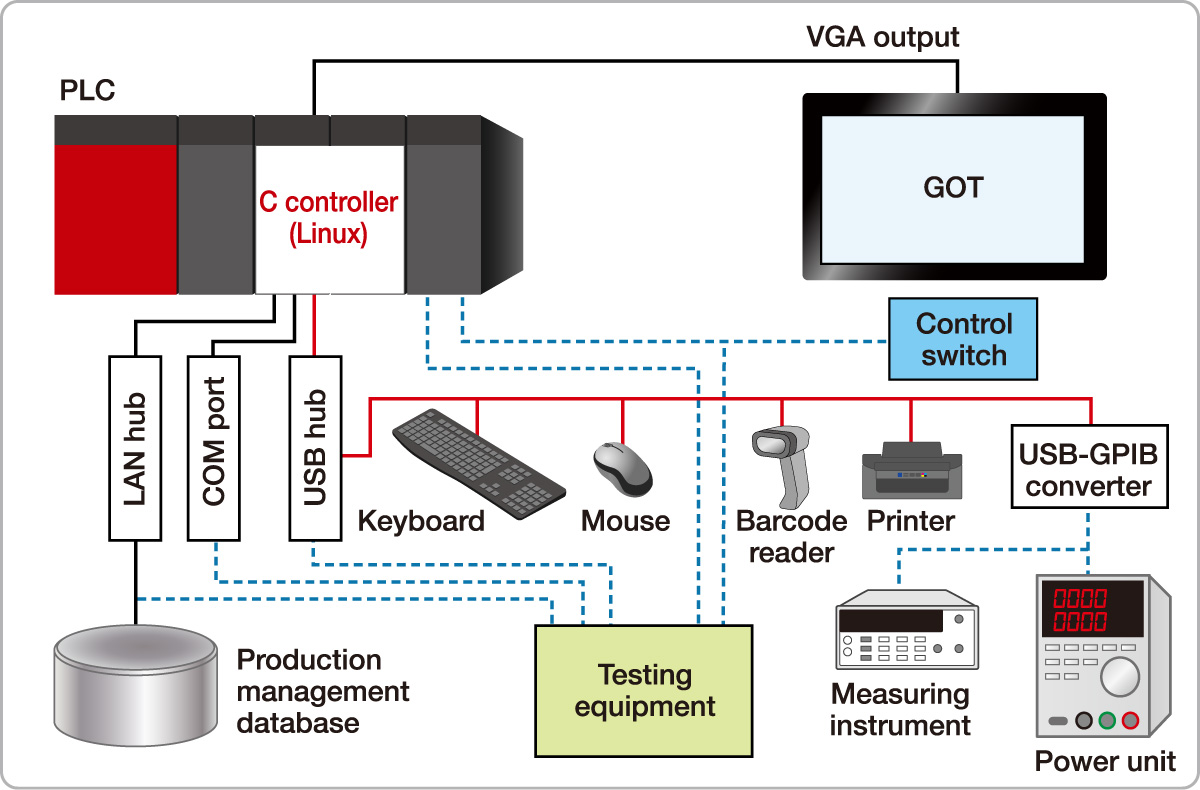
System configuration of test equipment after introducing C Controller
A primary reason why the C Controller is so effective in solving the PC-related issues is that it is made for factory automation applications. Since it has been developed for use in production sites, it does not have a hard drive (a common failure point for PCs), which significantly improves reliability. Long-term product supply is essential for FA equipment, allowing operators to avoid the disadvantages of the short product lifecycles associated with PCs. This means it is less likely to be discontinued – making the C Controller an effective PC replacement.
The Nagoya Works began the transition from PCs to C Controllers on the test equipment for PLCs. At first, the migration was done by using C Controllers alongside PCs. However, as the lineup of these devices and their available functions has expanded, almost all application requirements can now be covered by them, which has accelerated the replacement process.
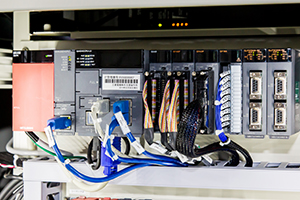
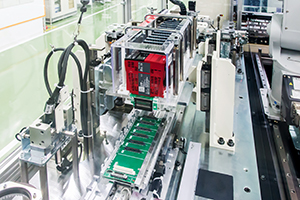
Base unit test equipment: one of the systems using the C Controller. The C Controller is used to control the test to check the input/output of the base unit and store test results in the production control database
No complicated wiring
Replacing PCs with C Controllers has had other benefits in addition to durability and supply. “Reduced wiring has made the system more compact,” says Hiroshi Kato of the Equipment Development Department, FA Manufacturing Section at the Nagoya Works. The C Controller is integrated with the base unit, which means no complicated wiring and no additional space is required as it was for the PC.
Offering 10 years of continuous use
Kita’s team calculated the effects of replacing the PCs with C Controllers. According to their studies, with conventional PC-based test equipment, the computer needs to be replaced approximately every four years. This involves complicated changeover adjustments such as modifying the system to the new PC and verifying operation.
In contrast, the C Controller boasts excellent durability as it is made for factory automation applications, so it is expected to last at least ten years. In addition, the test software only requires minor modifications for updates. “On an annual basis, we have calculated that operating and maintenance costs can be reduced to 1/6 of that of the PC-based system,” says Kita.
Previously, a total of around 700 units of pre-shipment test equipment were used in the manufacturing process of FA-related products at the Nagoya Works, partner and overseas factories. This number is increasing at a rate of around 20 units per year as the product lineup expands. In future, production information is expected to become big data, which will only increase management requirements. However, this concern is also being addressed by the replacement of PCs with C Controllers. The Nagoya Works is continuing this changeover, which will reduce operation and maintenance costs, leading to further TCO enhancements for all associated equipment.