Support
Manual
-
FR-E800 GUIDELINE
-
FR-E860 GUIDELINE
-
FR-E800-SCE GUIDELINE
-
FR-E860-SCE GUIDELINE
-
FR-E800(-E) Instruction Manual(Connection)
-
FR-E860 Instruction Manual(Connection)
-
FR-E800(-E) Instruction Manual(Function)
-
FR-E800(-E) Instruction Manual(Communication)
-
FR-E800(-E) Instruction Manual(Maintenance)
-
FR-E800(-E) Instruction Manual(Functional Safety)
-
FR-E800-SCE Instruction Manual(Functional Safety)
-
FR-E800(-E) Options
English
-
Quick start guide for FR-E800
Technical News
-
Branch Circuit Protection for FR-E800 drives Acceptable fuses and circuit breakers for FR-E800 drives
Network
Faults
Warning
Operation panel indication |
Name |
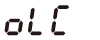 |
OLC |
Stall prevention (overcurrent) |
more |
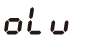 |
OLV |
Stall prevention (overvoltage) |
more |
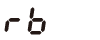 |
RB |
Regenerative brake pre-alarm |
more |
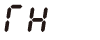 |
TH |
Electronic thermal relay function prealarm |
more |
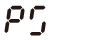 |
PS |
PU stop |
more |
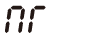 |
MT |
Maintenance timer |
more |
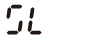 |
SL |
Speed limit indication |
more |
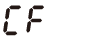 |
CF |
Continuous operation during communication |
more |
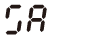 |
SA |
Safety stop |
more |
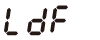 |
LDF |
Load fault warning |
more |
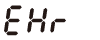 |
EHR |
Ethernet communication fault |
more |
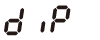 |
DIP |
Duplicate IP address |
more |
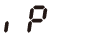 |
IP |
IP address fault |
more |
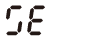 |
SE |
Incorrect parameter setting |
more |
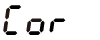 |
Cor |
Corrosion warning |
more |
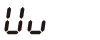 |
UV |
Undervoltage |
more |
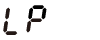 |
LP |
Stroke limit warning |
more |
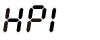 |
HP1 |
Home position return error |
more |
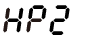 |
HP2 |
Home position return error |
more |
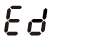 |
ED |
Emergency drive in operation (Standard model / Ethernet model) |
more |
Alarm
Operation panel indication |
Name |
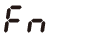 |
FN |
Fan alarm |
more |
Fault
Operation panel indication |
Name |
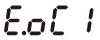 |
E.OC1 |
Overcurrent trip during acceleration |
more |
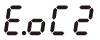 |
E.OC2 |
Overcurrent trip during constant |
more |
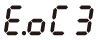 |
E.OC3 |
Overcurrent trip during deceleration |
more |
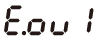 |
E.OV1 |
Regenerative overvoltage trip |
more |
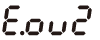 |
E.OV2 |
Regenerative overvoltage trip |
more |
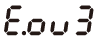 |
E.OV3 |
Regenerative overvoltage trip |
more |
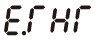 |
E.THT |
Inverter overload trip (electronic |
more |
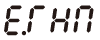 |
E.THM |
Motor overload trip (electronic thermal |
more |
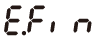 |
E.FIN |
Heat sink overheat |
more |
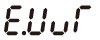 |
E.UVT |
Undervoltage |
more |
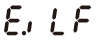 |
E.ILF |
Input phase loss |
more |
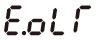 |
E.OLT |
Stall prevention stop |
more |
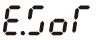 |
E.SOT |
Loss of synchronism |
more |
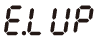 |
E.LUP |
Upper limit fault detection |
more |
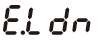 |
E.LDN |
Lower limit fault detection |
more |
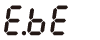 |
E.BE |
Brake transistor alarm detection |
more |
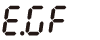 |
E.GF |
Output side earth (ground) fault |
more |
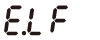 |
E.LF |
Output phase loss |
more |
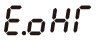 |
E.OHT |
External thermal relay operation |
more |
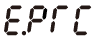 |
E.PTC |
PTC thermistor operation |
more |
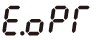 |
E.OPT |
Option fault |
more |
Operation panel indication |
Name |
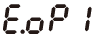 |
E.OP1 |
Communication option fault |
more |
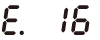 |
E.16 |
User definition error by the PLC function |
more |
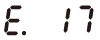 |
E.17 |
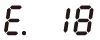 |
E.18 |
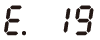 |
E.19 |
 |
E.20 |
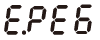 |
E.PE6 |
Internal storage device fault |
more |
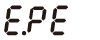 |
E.PE |
Parameter storage device fault (control |
more |
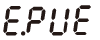 |
E.PUE |
PU disconnection |
more |
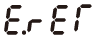 |
E.RET |
Retry count excess |
more |
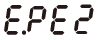 |
E.PE2 |
Parameter storage device fault (main |
more |
 |
E.CPU |
CPU fault |
more |
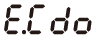 |
E.CDO |
Abnormal output current detection |
more |
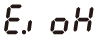 |
E.IOH |
Inrush current limit circuit fault |
more |
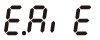 |
E.AIE |
Analog input fault |
more |
Operation panel indication |
Name |
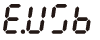 |
E.USB |
USB communication |
more |
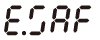 |
E.SAF |
Safety circuit fault |
more |
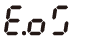 |
E.OS |
Overspeed occurrence |
more |
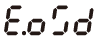 |
E.OSD |
Speed deviation excess detection |
more |
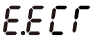 |
E.ECT |
Signal loss detection |
more |
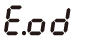 |
E.OD |
Excessive position fault |
more |
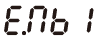 |
E.MB1 |
Brake sequence fault |
more |
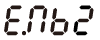 |
E.MB2 |
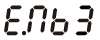 |
E.MB3 |
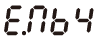 |
E.MB4 |
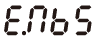 |
E.MB5 |
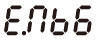 |
E.MB6 |
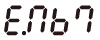 |
E.MB7 |
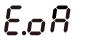 |
E.OA |
Acceleration error |
more |
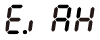 |
E.IAH |
Abnormal internal temperature |
more |
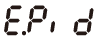 |
E.PID |
PID signal fault |
more |
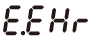 |
E.EHR |
Ethernet communication |
more |
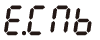 |
E.CMB |
Board combination |
more |
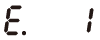 |
E.1 |
Option fault |
more |
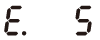 |
E.5 |
CPU fault |
more |
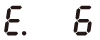 |
E.6 |
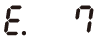 |
E.7 |
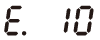 |
E.10 |
Output side fault |
more |
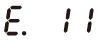 |
E.11 |
Opposite rotation deceleration fault |
more |
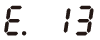 |
E.13 |
Internal circuit fault (15 V poser supply) |
more |
Others
Operation panel indication |
Name |
 |
No fault history |
more |
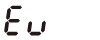 |
24 V external power supply operation |
more |
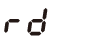 |
Backup in progress |
more |
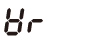 |
Restoration in progress |
more |
Causes and corrective actions
Operation panel lock
Operation panel indication |
HOLD |
Description |
Operation lock is set. Operation other than pressing the STOP/RESET key is disabled. |
Check point |
-------------- |
Corrective action |
Press the MODE key for 2 seconds to release the lock. |

Password locked
Operation panel indication |
LOCD |
Description |
Password function is active. Display and setting of parameters are restricted. |
Check point |
-------------- |
Corrective action |
Enter the password in Pr.297 Password lock/unlock to unlock the password function before operating. |

Write disable error
Operation panel indication |
Er1 |
Description |
- Parameter setting was attempted while Pr.77 Parameter write selection is set to disable parameter write.
- Overlapping range has been set for the frequency jump.
- The PU and inverter cannot make normal communication.
|
Check point |
- Check the Pr.77 setting.
- Check the settings of Pr.31 to Pr.36 (frequency jump).
- Check the connection of PU and the inverter.
|

Write error during operation
Operation panel indication |
Er2 |
Description |
Parameter write was attempted while Pr.77 Parameter write selection = "0". |
Check point |
Check that the inverter is stopped. |
Corrective action |
- After stopping the operation, make parameter setting.
- When setting Pr.77 = "2", parameter write is enabled during operation.
|

Calibration error
Operation panel indication |
Er3 |
Description |
Analog input bias and gain calibration values have been set too close. |
Check point |
Check the settings of the calibration parameters C3, C4, C6, and C7 (calibration functions). |

Mode designation error
Operation panel indication |
Er4 |
Description |
- Parameter setting was attempted in the External or NET operation mode while Pr.77 Parameter write selection = "1".
- Parameter write was attempted when the command source is not at the operation panel.
|
Check point |
- Check that the operation mode is the PU operation mode.
- Check that the Pr.551 PU mode operation command source selection setting is correct.
|
Corrective action |
- After setting the operation mode to the "PU operation mode", make parameter setting.
- When Pr.77 = "2", parameter write is enabled regardless of the operation mode.
- Set Pr.551 = "4".
|

Error
Operation panel indication |
Err. |
Description |
- The RES signal is turned ON.
- This error may occur when the voltage at the input side of the inverter drops.
|
Corrective action |
Turn OFF the RES signal. |

Stall prevention (overcurrent)
Operation panel indication |
OLC |
FR-LU08 indication |
OL |
Description |
- When the output current of the inverter increases, the stall prevention (overcurrent) function is activated.
- The following section explains about the stall prevention (overcurrent) function.
|
During acceleration |
When the output current (output torque under Real sensorless vector control or Vector control) of the inverter exceeds the stall prevention level (Pr.22 Stall prevention operation level, etc.), this function stops the increase in frequency until the overload current decreases to prevent the inverter from resulting in overcurrent trip. When the overload current is reduced below stall prevention operation level, this function increases the frequency again. |
During constant-speed operation |
When the output current (output torque under Real sensorless vector control or Vector control) of the inverter exceeds the stall prevention level (Pr.22 Stall prevention operation level, etc.), this function reduces frequency until the overload current decreases to prevent the inverter from resulting in overcurrent trip. When the overload current is reduced below stall prevention operation level, this function increases the frequency up to the set value. |
During deceleration |
When the output current (output torque under Real sensorless vector control or Vector control) of the inverter exceeds the stall prevention level (Pr.22 Stall prevention operation level, etc.), this function stops the decrease in frequency until the overload current decreases to prevent the inverter from resulting in overcurrent trip. When the overload current is reduced below stall prevention operation level, this function decreases the frequency again. |
Check point |
- Check that the Pr.0 Torque boost setting is not too large.
- The Pr.7 Acceleration time and Pr.8 Deceleration time settings may be too short.
- Check that the load is not too heavy.
- Check for any failures in peripheral devices.
- Check that the Pr.13 Starting frequency is not too large.
- Check that Pr.22 Stall prevention operation level is appropriate.
|
Corrective action |
- Gradually increase or decrease the Pr.0 setting by 1% at a time and check the motor status.
- Set a larger value in Pr.7 and Pr.8.
- Reduce the load.
- Try Advanced magnetic flux vector control, Real sensorless vector control, or Vector control.
- Change the Pr.14 Load pattern selection setting.
- The stall prevention operation current can be set in Pr.22 Stall prevention operation level. (The initial value is 150% for the ND rating.) The acceleration/deceleration time may change. Increase the stall prevention operation level with Pr.22 Stall prevention operation level, or disable stall prevention with Pr.156 Stall prevention operation selection. (Use Pr.156 to set either operation continued or not at OLC operation.)
|

Stall prevention (overvoltage)
Operation panel indication |
OLV |
FR-LU08 indication |
oL |
Description |
- When the output voltage of the inverter increases, the stall prevention (overvoltage) function is activated.
- The regeneration avoidance function is activated due to excessive regenerative power of the motor.
- The following section explains the stall prevention (overvoltage) function.
|
During deceleration |
If the regenerative power of the motor becomes excessive to exceed the regenerative power consumption capability, this function stops decreasing the frequency to prevent overvoltage trip. As soon as the regenerative power has reduced, deceleration resumes. |
Check point |
- Check for sudden speed reduction.
- Check if the regeneration avoidance function (Pr.882, Pr.883, Pr.885, and Pr.886) is being used.
|
Corrective action |
The deceleration time may change. Increase the deceleration time using Pr.8 Deceleration time. |

Regenerative brake pre-alarm
Operation panel indication |
RB |
FR-LU08 indication |
RB |
Description |
Appears if the regenerative brake duty reaches or exceeds 85% of the Pr.70 Special regenerative brake duty value. If the regenerative brake duty reaches 100%, a regenerative overvoltage (E. OV[ ]) occurs. |
Check point |
- Check if the brake resistor duty is not too high.
- Check that the Pr.30 Regenerative function selection and Pr.70 settings are correct.
|
Corrective action |
- Set the deceleration time longer.
- Check the Pr.30 and Pr.70 settings.
|

Electronic thermal relay function pre-alarm
Operation panel indication |
TH |
FR-LU08 indication |
TH |
Description |
Appears if the cumulative value of the electronic thermal O/L relay reaches or exceeds 85% of the preset level of Pr.9 Electronic thermal O/L relay. If the specified value is reached, the protection circuit is activated to shut off the inverter output. |
Check point |
- Check for large load or sudden acceleration.
- Check that the Pr.9 setting is appropriate.
|
Corrective action |
- Reduce the load and frequency of operation.
- Set an appropriate value in Pr.9.
|

PU stop
Operation panel indication |
PS |
FR-LU08 indication |
PS |
Description |
- The motor is stopped using the STOP/RESET key under the mode other than the PU operation mode. (To enable the STOP/RESET key under the mode other than the PU operation mode, set Pr.75 Reset selection/disconnected PU detection/PU stop selection.
- The motor is stopped by the emergency stop function.
|
Check point |
- Check for a stop made by pressing the STOP/RESET key on the operation panel.
- Check for whether the X92 signal is OFF.
|
Corrective action |
- Turn OFF the start signal and press the PU/EXT key for release.
- Turn ON the X92 signal and OFF the start signal for release.
|

Speed limit indication (output during speed limit)
Operation panel indication |
SL |
FR-LU08 indication |
SL |
Description |
Output if the speed limit level is exceeded during torque control. |
Check point |
- Check that the torque command is not larger than required.
- Check if the speed limit level is set too low.
|
Corrective action |
- Decrease the torque command value.
- Increase the speed limit level.
|

Safety stop
Operation panel indication |
SA |
FR-LU08 indication |
SA |
Description |
Appears when safety stop function is activated (during output shutoff). |
Check point |
- Check if an emergency stop device is activated.
- Check if the shorting wire between S1 and PC or between S2 and PC is disconnected when not using the safety stop function.
|
Corrective action |
- An emergency stop device is active when using the safety stop function. Identify the cause of emergency stop, ensure the safety and restart the system.
- When not using the safety stop function, short across terminals S1 and PC and across S2 and PC with shorting wire for the inverter to run.
- If "SA" is indicated when wires across S1 and PC and across S2 and PC are both conducted while using the safety stop function (drive enabled), internal failure might be the cause. Check the wiring of terminals S1, S2, and SIC and contact your sales representative if the wiring has no fault.
|

Maintenance timer
Operation panel indication |
MT |
FR-LU08 indication |
MT |
Description |
Appears when the inverter's cumulative energization time reaches or exceeds the parameter set value. Set the time until the MT is displayed using Pr.504 Maintenance timer warning output set time (MT). "MT" does not appear when the setting of Pr.504 is the initial value ("9999"). |
Check point |
The set time of maintenance timer has been exceeded. |
Corrective action |
Take appropriate countermeasures according to the purpose of the maintenance timer setting.
Setting "0" in Pr.503 Maintenance timer clears the indication. |

Continuous operation during communication fault
Operation panel indication |
CF |
FR-LU08 indication |
CF |
Description |
Appears when the operation continues while an error is occurring in the communication line or communication option (when Pr.502 = "6"). |
Check point |
- Check for a break in the communication cable.
- Check for communication option faults.
|
Corrective action |
- Check the connection of communication cable.
- Replace the communication option.
|

Load fault warning
Operation panel indication |
LDF |
FR-LU08 indication |
LDF |
Description |
Appears when the load is deviated from the detection width set in Pr.1488 Upper limit warning detection width or Pr.1489 Lower limit warning detection width. |
Check point |
- Check if too much load is applied to the equipment, or if the load is too light.
- Check that the load characteristics settings are correct.
|
Corrective action |
- Inspect the equipment.
- Set the load characteristics (Pr.1481 to Pr.1487) correctly.
|

Ethernet communication fault
Operation panel indication |
EHR |
FR-LU08 indication |
EHR |
Description |
Appears when Ethernet communication is interrupted by physical factors while Pr.1431 Ethernet signal loss detection function selection = "1 to 3". |
Check point |
- Check for a break in the communication cable.
- Check for a break in the Ethernet cable.
|
Corrective action |
- Connect the Ethernet board securely.
- Check that the Ethernet cable is connected to the Ethernet connector properly and the Ethernet cable is not damaged.
|

Duplicate IP address
Operation panel indication |
DIP |
FR-LU08 indication |
DIP |
Description |
Appears when duplicate IP address is detected. |
Check point |
Check that the specified IP address is not overlapping with the IP address of any other device on the network. |
Corrective action |
Enter a unique IP address. |

IP address fault
Operation panel indication |
IP |
FR-LU08 indication |
IP |
Description |
Appears when the IP address or the subnet mask is out of the specified range. |
Check point |
- Check that "0 or 255" is not set in the third or fourth octet of the IP address.
- Check that the subnet mask setting is appropriate.
- Check that the IP address settings are correct.
|
Corrective action |
- Set "1 to 254" in the third or fourth octet of the IP address.
- Set the subnet mask (Pr.1438 to Pr.1441) correctly.
- Set the IP address (Pr.1434 to Pr.1447) correctly.
|

Incorrect parameter setting
Operation panel indication |
SE |
FR-LU08 indication |
SE |
Description |
Appears when a start command is input while the condition to start operation is not satisfied in the motor setting (Pr.71, Pr.450, Pr.80, Pr.453, Pr.81, or Pr.454) for the control method selected in Pr.800 or Pr.451. |
Check point |
Check that the motor setting is appropriate for the control method. |
Corrective action |
Change the control method setting or the motor setting as appropriate. |

Corrosion warning
Operation panel indication |
Cor |
FR-LU08 indication |
Cor |
Description |
Appears when the corrosion level of the control circuit board becomes "3" (Pr.198 = "3"). (Available only for the
FR-E8[][]-[]-60 (with coating).) |
Check point |
Check that the operating environment of the inverter is appropriate. |
Corrective action |
- Improve the operating environment of the inverter (by a filter or ventilation).
- Consider replacing the inverter early.
|

Undervoltage
Operation panel indication |
UV |
FR-LU08 indication |
-------------- |
Description |
If the power supply voltage of the inverter decreases, the control circuit will not perform normal functions. In addition, the motor torque will be insufficient and/or heat generation will increase. To prevent this, if the power supply voltage decreases to about 115 VAC (230 VAC for the 400 V class, 330 VAC for the 575 V class) or below, this function shuts off the inverter output and "UV" is displayed. The warning is removed when the voltage returns to normal. |
Check point |
Check that the power supply voltage is normal. |
Corrective action |
Check the devices on the power system such as the power supply itself. |

Stroke limit warning
Operation panel indication |
LP |
FR-LU08 indication |
LP |
Description |
Appears when the Forward stroke end (LSP) signal or the Reverse stroke end (LSN) signal is assigned to the input terminal and the signal is turned OFF (normally closed input). The indication remains displayed while the signal is OFF. |
Check point |
Check if the LSP/LSN signal is turned OFF (normally closed input). |
Corrective action |
Turn ON the LSP/LSN signal (normally closed input). |

Home position return error
Operation panel indication |
HP1, HP2 |
FR-LU08 indication |
HP1, HP2 |
Description |
Appears when an error occurs during the home position return operation under position control. |
Check point |
Identify the cause of the error occurrence. |
Corrective action |
Check the parameter setting, and check that the input signal is correct. |

Emergency drive in operation (Standard model / Ethernet model)
Operation panel indication |
ED |
FR-LU08 indication |
ED |
Description |
Appears during emergency drive operation. |
Check point |
Emergency drive operation is performed by turning ON the X84 signal. |
Corrective action |
The display is cleared when the emergency drive operation ends. |

Fan alarm
Operation panel indication |
FN |
FR-LU08 indication |
FN |
Description |
For the inverter that contains a cooling fan, FN appears on the operation panel when the cooling fan stops due to a fault, low rotation speed, or different operation from the setting of Pr.244 Cooling fan operation selection. |
Check point |
Check the cooling fan for a failure. |
Corrective action |
The fan may be faulty. Contact your sales representative. |

Overcurrent trip during acceleration
Operation panel indication |
E.OC1 |
FR-LU08 indication |
OC During Acc |
Description |
When the inverter output current reaches or exceeds approximately 230% of the rated current during acceleration, the protection circuit is activated and the inverter output is shut off. |
Check point |
- Check for sudden speed acceleration.
- Check if the downward acceleration time is too long in a lift application.
- Check for output short-circuit.
- Check that the Pr.3 Base frequency setting is not 60 Hz when the motor rated frequency is 50 Hz.
- Check if the stall prevention operation level is set too high. Check if the fast-response current limit operation is disabled.
- Check that the regenerative driving is not performed frequently. (Check if the output voltage becomes larger than the V/F reference voltage at regenerative driving and overcurrent occurs due to increase in the motor current.)
- Check that the encoder wiring and the specifications (encoder power supply, resolution, differential/complementary) are correct. Check also that the motor wiring (U, V, W) is correct (under Vector control).
- Check that the rotation direction is not switched from forward to reverse rotation (or from reverse to forward) during torque control under Real sensorless vector control.
- Check that the inverter capacity matches with the motor capacity. (PM sensorless vector control)
- Check if a start command is given to the inverter while the motor is coasting. (PM sensorless vector control)
|
Corrective action |
- Set the acceleration time longer. (Shorten the downward acceleration time of the lift.)
- If "E.OC1" always appears at start, disconnect the motor once and restart the inverter. If "E.OC1" still appears, contact your sales representative.
- Check the wiring to make sure that output short circuit does not occur.
- Set 50 Hz in Pr.3 Base frequency.
- Lower the stall prevention operation level. Activate the fast-response current limit operation.
- Set the base voltage (rated voltage of the motor, etc.) in Pr.19 Base frequency voltage.
- Check the wiring and specifications of the encoder and the motor. Perform the setting according to the specifications of the encoder and the motor (under Vector control).
- Prevent the motor from switching the rotation direction from forward to reverse (or from reverse to forward) during torque control under Real sensorless vector control.
- Choose inverter and motor capacities that match. (PM sensorless vector control)
- Input a start command after the motor stops. Alternatively, use the automatic restart after instantaneous power failure / flying start function. (PM sensorless vector control)
|

Overcurrent trip during constant speed
Operation panel indication |
E.OC2 |
FR-LU08 indication |
OC During Cnst Spd |
Description |
When the inverter output current reaches or exceeds approximately 230% of the rated current during constant-speed operation, the protection circuit is activated and the inverter output is shut off. |
Check point |
- Check for sudden load change.
- Check for a short-circuit in the output circuit.
- Check if the stall prevention operation level is set too high. Check if the fast-response current limit operation is disabled.
- Check that the rotation direction is not switched from forward to reverse rotation (or from reverse to forward) during torque control under Real sensorless vector control.
- Check that the inverter capacity matches with the motor capacity. (PM sensorless vector control)
- Check if a start command is given to the inverter while the motor is coasting. (PM sensorless vector control)
|
Corrective action |
- Keep the load stable.
- Check the wiring to make sure that output short circuit does not occur.
- Lower the stall prevention operation level. Activate the fast-response current limit operation.
- Prevent the motor from switching the rotation direction from forward to reverse (or from reverse to forward) during torque control under Real sensorless vector control.
- Choose inverter and motor capacities that match. (PM sensorless vector control)
- Input a start command after the motor stops. Alternatively, use the automatic restart after instantaneous power failure / flying start function. (PM sensorless vector control)
|

Overcurrent trip during deceleration or stop
Operation panel indication |
E.OC3 |
FR-LU08 indication |
OC During Dec |
Description |
When the inverter output current reaches or exceeds approximately 230% of the rated current during deceleration (other than acceleration or constant speed), the protection circuit is activated and the inverter output is shut off. |
Check point |
- Check for sudden speed reduction.
- Check for a short-circuit in the output circuit.
- Check for too fast operation of the motor's mechanical brake.
- Check if the stall prevention operation level is set too high. Check if the fast-response current limit operation is disabled.
- Check that the rotation direction is not switched from forward to reverse rotation (or from reverse to forward) during torque control under Real sensorless vector control.
- Check that the inverter capacity matches with the motor capacity. (PM sensorless vector control)
- Check if a start command is given to the inverter while the motor is coasting. (PM sensorless vector control)
|
Corrective action |
- Set the deceleration time longer.
- Check the wiring to make sure that output short circuit does not occur.
- Check the mechanical brake operation.
- Lower the stall prevention operation level. Activate the fast-response current limit operation.
- Prevent the motor from switching the rotation direction from forward to reverse (or from reverse to forward) during torque control under Real sensorless vector control.
- Choose inverter and motor capacities that match. (PM sensorless vector control)
- Input a start command after the motor stops. Alternatively, use the automatic restart after instantaneous power failure / flying start function. (PM sensorless vector control)
|

Regenerative overvoltage trip during acceleration
Operation panel indication |
E.OV1 |
FR-LU08 indication |
OV During Acc |
Description |
If regenerative power causes the inverter's internal main circuit DC voltage to reach or exceed the specified value, the protection circuit is activated to stop the inverter output. The circuit may also be activated by a surge voltage produced in the power supply system. |
Check point |
- Check for too slow acceleration. (e.g. during downward acceleration in vertical lift load)
- Check that the Pr.22 Stall prevention operation level is not set to the no load current or lower.
- Check if the stall prevention operation is frequently activated in an application with a large load inertia.
|
Corrective action |
- Set the acceleration time shorter.
Use the regeneration avoidance function (Pr.882, Pr.883, Pr.885, and Pr.886).
- Set a value larger than the no load current in Pr.22.
- Set Pr.154 Voltage reduction selection during stall prevention operation = "11".
|

Regenerative overvoltage trip during constant speed
Operation panel indication |
E.OV2 |
FR-LU08 indication |
OV During Cnst Spd |
Description |
If regenerative power causes the inverter's internal main circuit DC voltage to reach or exceed the specified value, the protection circuit is activated to stop the inverter output. The circuit may also be activated by a surge voltage produced in the power supply system. |
Check point |
- Check for sudden load change.
- Check that the Pr.22 Stall prevention operation level is not set to the no load current or lower.
- Check if the stall prevention operation is frequently activated in an application with a large load inertia.
- Check that acceleration/deceleration time is not too short.
|
Corrective action |
- Keep the load stable.
- Use the regeneration avoidance function (Pr.882, Pr.883, Pr.885, and Pr.886).
- Use a brake resistor or brake unit, or the multifunction regeneration converter (FR-XC) as required.
- Set a value larger than the no load current in Pr.22.
- Set Pr.154 Voltage reduction selection during stall prevention operation = "11".
- Set the acceleration/deceleration time longer. (Under Vector control or Advanced magnetic flux vector control, the output torque can be increased. However, sudden acceleration may cause an overshoot in speed, resulting in an occurrence of overvoltage.)
|

Regenerative overvoltage trip during deceleration or stop
Operation panel indication |
E.OV3 |
FR-LU08 indication |
OV During Dec |
Description |
If regenerative power causes the inverter's internal main circuit DC voltage to reach or exceed the specified value, the protection circuit is activated to stop the inverter output. The circuit may also be activated by a surge voltage produced in the power supply system. |
Check point |
- Check for sudden speed reduction.
- Check if the stall prevention operation is frequently activated in an application with a large load inertia.
|
Corrective action |
- Set the deceleration time longer. (Set the deceleration time which matches the moment of inertia of the load.)
- Make the brake cycle longer.
- Use the regeneration avoidance function (Pr.882, Pr.883, Pr.885, and Pr.886).
- Use a brake resistor or brake unit, or the multifunction regeneration converter (FR-XC) as required.
- Set Pr.154 Voltage reduction selection during stall prevention operation = "11".
|

Inverter overload trip (Electronic thermal O/L relay)
Operation panel indication |
E.THT |
FR-LU08 indication |
Inv. overload trip |
Description |
If the temperature of the output transistor elements exceeds the protection level with a rated output current or higher flowing without the overcurrent trip (E.OC[]), the inverter output is stopped. (Overload capacity 150% 60 s) |
Check point |
- Check that acceleration/deceleration time is not too short.
- Check that torque boost setting is not too large (small).
- Check that load pattern selection setting is appropriate for the load pattern of the using machine.
- Check the motor for the use under overload.
- Check that the encoder wiring and the specifications (encoder power supply, resolution, differential/complementary) are correct. Check also that the motor wiring (U, V, W) is correct (under Vector control).
|
Corrective action |
- Set the acceleration/deceleration time longer.
- Adjust the torque boost setting.
- Set the load pattern selection setting according to the load pattern of the using machine.
- Reduce the load.
- Check the wiring and specifications of the encoder and the motor. Perform the setting according to the specifications of the encoder and the motor (under Vector control).
|

Motor overload trip (electronic thermal relay function)
Operation panel indication |
E.THM |
FR-LU08 indication |
Motor overload trip |
Description |
The electronic thermal O/L relay function in the inverter detects motor overheat, which is caused by overload or reduced cooling capability during low-speed operation. When the cumulative heat value reaches 85% of the Pr.9 Electronic thermal O/L relay setting, pre-alarm (TH) is output. When the accumulated value reaches the specified value, the protection circuit is activated to stop the inverter output. When the inverter is used to drive a dedicated motor, such as a multiple-pole motor, or several motors, the motor cannot be protected by the electronic thermal O/L relay. Install an external thermal relay on the inverter output side. |
Check point |
- Check the motor for the use under overload.
- Check that the setting of Pr.71 Applied motor for motor selection is correct.
- Check that the stall prevention operation setting is correct.
|
Corrective action |
- Reduce the load.
- For a constant-torque motor, set the constant-torque motor in Pr.71.
- Set the stall prevention operation level accordingly.
|

Heat sink overheat
Operation panel indication |
E.FIN |
FR-LU08 indication |
Heatsink overheat |
Description |
When the heat sink overheats, the temperature sensor is activated, and the inverter output is stopped.
The FIN signal can be output when the temperature becomes approximately 85% of the heat sink overheat protection operation temperature.
For the terminal used for the FIN signal output, assign the function by setting "26 (positive logic) or 126 (negative logic)" from Pr.190 to Pr.196 (Output terminal function selection). |
Check point |
- Check for too high surrounding air temperature.
- Check for heat sink clogging.
- Check that the cooling system is not stopped. (Check that FN is not displayed on the operation panel.)
- Check that the cooling fan is installed in correct orientation.
|
Corrective action |
- Set the surrounding air temperature to within the specifications.
- Clean the heat sink.
- Replace the cooling fan.
- Install the cooling fan in correct orientation.
|

Undervoltage
Operation panel indication |
E.UVT |
FR-LU08 indication |
Under Voltage |
Description |
When a PM motor is used, the protective function is activated in the following case: a fault such as power failure or voltage drop occurs, the converter voltage drops to cause the motor to coast, and restarting and coasting are repeated by the automatic restart after instantaneous power failure function. |
Check point |
Check that no fault is found in the power supply. |
Corrective action |
Supply appropriate power. |

Input phase loss
Operation panel indication |
E.ILF |
FR-LU08 indication |
Input phase loss |
Description |
When Pr.872 Input phase loss protection selection is enabled ("1") and one of the three-phase power input is lost, the inverter output is shut off. This protective function is not available when "0" is set in Pr.872. This protective function is available for the three-phase power input model. |
Check point |
Check for a break in the cable for the three-phase power supply input. |
Corrective action |
- Wire the cables properly.
- Repair a break portion in the cable.
|

Stall prevention stop
Operation panel indication |
E.OLT |
FR-LU08 indication |
Stall prevention STP |
Description |
[V/F] [Magnetic flux]
If the output frequency has fallen to 0.5 Hz by stall prevention operation and remains for 3 seconds, a fault (E.OLT) appears and the inverter is shut off. OLC or OLV appears while stall prevention is being activated. |
[Sensorless] [PM]
When speed control is performed, a fault (E.OLT) appears and the inverter output is shut off if frequency drops to the Pr.865 Low speed detection (initial value is 1.5 Hz) setting by torque limit operation and the output torque exceeds the Pr.874 OLT level setting (initial value is 150%) setting and remains 3 seconds. |
Check point |
- Check the motor for the use under overload.
- Check that the Pr.865 and Pr.874 values are correct.
(Check the Pr.22 Stall prevention operation level setting under V/F control and Advanced magnetic flux vector control.)
- Check if a motor is connected under PM sensorless vector control.
|
Corrective action |
- Reduce the load.
- Change the Pr.22, Pr.865, and Pr.874 values. (Check the Pr.22 setting under V/F control and Advanced magnetic flux vector control.)
- For the test operation without connecting a motor, select the PM sensorless vector control test operation.
- Also check that the stall prevention (overcurrent) warning (OLC) or the stall prevention (overvoltage) warning (OLV) countermeasure is taken.
|

Loss of synchronism detection
Operation panel indication |
E.SOT
[PM] |
FR-LU08 indication |
Motor Step Out |
Description |
The inverter output is shut off when the motor operation is not synchronized. (This function is only available under PM sensorless vector control.) |
Check point |
- Check that the PM motor is not driven overloaded.
- Check if a start command is given to the inverter while the PM motor is coasting.
- Check if a motor is connected under PM sensorless vector control.
- Check if a motor other than PM motors is driven.
|
Corrective action |
- Set the acceleration time longer.
- Reduce the load.
- If the inverter restarts during coasting, set Pr.57 Restart coasting time ≠ "9999", and select the automatic restart after instantaneous power failure.
- Check the connection of the IPM motor.
- For the test operation without connecting a motor, select the PM sensorless vector control test operation.
- When driving a PM motor, offline auto tuning must be performed.
|

Upper limit fault detection
Operation panel indication |
E.LUP |
FR-LU08 indication |
Upper limit fault |
Description |
The inverter output is shut off when the load exceeds the upper limit fault detection range. This protective function is not available in the initial setting of Pr.1490 (Pr.1490 = "9999"). |
Check point |
- Check if too much load is applied to the equipment.
- Check that the load characteristics settings are correct.
|
Corrective action |
- Inspect the equipment.
- Set the load characteristics (Pr.1481 to Pr.1487) correctly.
|

Lower limit fault detection
Operation panel indication |
E.LDN |
FR-LU08 indication |
Lower limit fault |
Description |
The inverter output is shut off when the load falls below the lower limit fault detection range. This protective function is not available in the initial setting of Pr.1491 (Pr.1491 = "9999"). |
Check point |
- Check if the equipment load is too light.
- Check that the load characteristics settings are correct.
|
Corrective action |
- Inspect the equipment.
- Set the load characteristics (Pr.1481 to Pr.1487) correctly.
|

Brake transistor alarm detection
Operation panel indication |
E.BE |
FR-LU08 indication |
Brake transistor err |
Description |
- The inverter output is shut off if a fault due to damage of the brake transistor and such occurs in the brake circuit.
In such a case, the power supply to the inverter must be shut off immediately.
|
Check point |
- Reduce the load inertia.
- Check that the brake duty is proper.
|
Corrective action |
Replace the inverter. |

Output side earth (ground) fault overcurrent
Operation panel indication |
E.GF |
FR-LU08 indication |
Ground Fault |
Description |
The inverter output is shut off if an earth (ground) fault overcurrent flows due to an earth (ground) fault that occurred on the inverter's output side (load side). |
Check point |
Check for a ground fault in the motor and connection cable. |
Corrective action |
Remedy the earth (ground) fault portion. |

Output phase loss
Operation panel indication |
E.LF |
FR-LU08 indication |
Output phase loss |
Description |
The inverter output is shut off if one of the three phases (U, V, W) on the inverter's output side (load side) is lost. |
Check point |
- Check the wiring. (Check that the motor is normally operating.)
- Check that the capacity of the motor used is not smaller than that of the inverter.
- Check if a start command is given to the inverter while the motor is coasting. (PM sensorless vector control)
|
Corrective action |
- Wire the cables properly.
- Input a start command after the motor stops. Alternatively, use the automatic restart after instantaneous power failure / flying start function. (PM sensorless vector control)
|

External thermal relay operation
Operation panel indication |
E.OHT |
FR-LU08 indication |
Ext TH relay oper |
Description |
The inverter output is shut off if the external thermal relay provided for motor overheat protection or the internally mounted thermal relay in the motor, etc. switches ON (contacts open). This function is available when "7" (OH signal) is set in any of Pr.178 to Pr.184 (Input terminal function selection). This protective function is not available in the initial status. (OH signal is not assigned.) (This protective function is available for the standard model and the Ethernet model.) |
Check point |
- Check for motor overheating.
- Check that the value "7" (OH signal) is set correctly to any of Pr.178 to Pr.184 (Input terminal function selection).
|
Corrective action |
- Reduce the load and operation duty.
- Even if the relay contacts are reset automatically, the inverter will not restart unless it is reset.
|

PTC thermistor operation
Operation panel indication |
E.PTC |
FR-LU08 indication |
PTC thermistor oper |
Description |
The inverter output is shut off if resistance of the PTC thermistor connected between terminal 2 and terminal 10 is equal to or higher than the Pr.561 PTC thermistor protection level setting for a continuous time equal to or longer than the setting value in Pr.1016 PTC thermistor protection detection time. This protective function is not available in the initial setting of Pr.561 (Pr.561 = "9999"). |
Check point |
- Check the connection with the PTC thermistor.
- Check the Pr.561 and Pr.1016 settings.
- Check the motor for operation under overload.
|
Corrective action |
Reduce the load. |

Option fault
Operation panel indication |
E.OPT |
FR-LU08 indication |
Option Fault |
Description |
- Appears when torque command by the plug-in option is selected using Pr.804 Torque command source selection and no plug-in option is mounted. This function is available under torque control.
- Appears when the switch for manufacturer setting of the plug-in option is changed.
- Appears when a communication option is connected while Pr.296 Password lock level = "0 or 100".
|
Check point |
- Check that the plug-in option for torque command setting is connected.
- Check for the password lock with a setting of Pr.296 = "0, 100".
|
Corrective action |
- Check for connection of the plug-in option. Check the Pr.804 setting.
- Set the switch on the plug-in option, which is for manufacturer setting, back to the initial setting.
- To apply the password lock when installing a communication option, set Pr.296 ≠ "0, 100".
|

Communication option fault
Operation panel indication |
E.OP1 |
FR-LU08 indication |
Option1 Fault |
Description |
- The inverter output is shut off if a communication line error occurs in the communication option.
|
Check point |
- Check for an incorrect option function setting and operation.
- Check that the plug-in option is plugged into the connector securely.
- Check for a break in the communication cable.
- Check that the terminating resistor is fitted properly.
|
Corrective action |
- Check the option function setting, etc.
- Connect the plug-in option securely.
- Check the connection of communication cable.
- If the fault occurs again when the inverter is reset, contact your sales representative.
|

User definition error by the PLC function
Operation panel indication |
E.16 to E.20 |
FR-LU08 indication |
Fault 16 to Fault 20 |
Description |
The protective function is activated by setting "16 to 20" in the special register SD1214 for the PLC function. The inverter output is shut off when the protective function is activated.
The protective function is activated when the PLC function is enabled. This protective function is not available in the initial setting (Pr.414 = "0"). |
Check point |
Check if "16 to 20" is set in the special register SD1214. |
Corrective action |
Set a value other than "16 to 20" in the special register SD1214. |

Internal storage device fault
Operation panel indication |
E.PE6 |
FR-LU08 indication |
Fault |
Description |
This protective function is activated by an inverter reset if writing data fails due to power-OFF or a data fault occurs in the storage device during parameter operations. |
Check point |
Check if the power was turned OFF during parameter operations. |
Corrective action |
Check the power supply or the devices on the power system to check that the devices have no fault.
- When E.PE6 occurs due to power-OFF during parameter operations:
Check the read value of Pr.890. When the value is "7" or smaller, perform All parameter clear and then an inverter reset. The parameters that had been changed before All parameter clear must be set again.
- When E.PE6 occurs due to other reason (such as turning OFF/ON the power or an inverter reset) or when the read value of Pr.890 is "8" or more:
Contact your sales representative.
|

Parameter storage device fault (control circuit board)
Operation panel indication |
E.PE |
FR-LU08 indication |
Corrupt Memory |
Description |
The inverter output is shut off if a fault occurs in the parameter stored. (EEPROM failure) |
Check point |
Check for too many number of parameter write times. |
Corrective action |
Contact your sales representative.
Set "1" in Pr.342 Communication EEPROM write selection (write to RAM) for the operation which requires frequent parameter writing via communication, etc. Note that writing to RAM goes back to the initial status at power OFF. |

PU disconnection
Operation panel indication |
E.PUE |
FR-LU08 indication |
PU disconnection |
Description |
- The inverter output is shut off if communication between the inverter and PU is suspended, e.g. the cable is disconnected from the PU connector, when the disconnected PU detection function is valid in Pr.75 Reset selection/disconnected PU detection/PU stop selection.
- The inverter output is shut off if communication errors occurred consecutively for more than permissible number of retries when Pr.121 PU communication retry count ≠ "9999" during the RS-485 communication.
- The inverter output is shut off if communication is broken within the period of time set in Pr.122 PU communication check time interval during the RS-485 communication via the PU connector. (This protective function is available for the standard model.)
|
Check point |
Check the Pr.75 setting. |
Corrective action |
Change the Pr.75 setting. |

Retry count excess
Operation panel indication |
E.RET |
FR-LU08 indication |
Retry count excess |
Description |
The inverter output is shut off if the operation cannot be resumed properly within the number of retries set in Pr.67 Number of retries at fault occurrence. This function is available when Pr.67 is set. This protective function is not available in the initial setting (Pr.67 = "0"). |
Check point |
Find the cause of the fault occurrence. |
Corrective action |
Eliminate the cause of the fault preceding this fault indication. |

Parameter storage device fault (main circuit board)
Operation panel indication |
E.PE2 |
FR-LU08 indication |
PR storage alarm |
Description |
The inverter output is shut off if a fault occurs in the inverter model information. |
Check point |
-------------- |
Corrective action |
Contact your sales representative. |

CPU fault
Operation panel indication |
E.CPU |
E. 5 |
E. 6 |
E. 7 |
FR-LU08 indication |
CPU fault |
Fault 5 |
Fault 6 |
Fault 7 |
Description |
The inverter output is shut off if the communication fault of the built-in CPU occurs. |
Check point |
- Check for devices producing excess electrical noises around the inverter.
- When Ethernet communication is used, check that the communication cable is connected properly.
|
Corrective action |
- Take measures against noises if there are devices producing excess electrical noises around the inverter.
- When Ethernet communication is used, connect the communication cable properly.
- Contact your sales representative.
|

Abnormal output current detection
Operation panel indication |
E.CDO |
FR-LU08 indication |
OC detect level |
Description |
The inverter output is shut off if the output current exceeds the Pr.150 Output current detection level setting. This functions is available when "1" is set in Pr.167 Output current detection operation selection. When the initial value (Pr.167 = "0") is set, this protective function is not available. |
Check point |
Check the settings of Pr.150, Pr.151 Output current detection signal delay time, Pr.166 Output current detection signal retention time, and Pr.167. |

Inrush current limit circuit fault
Operation panel indication |
E.IOH |
FR-LU08 indication |
Inrush overheat |
Description |
The inverter output is shut off when the resistor of the inrush current limit circuit is overheated. The inrush current limit circuit is faulty. |
Check point |
- Check that frequent power ON/OFF is not repeated.
- Check if the input side fuse (5A) in the power supply circuit of the inrush current limit circuit contactor is blown.
- Check that the power supply circuit of inrush current limit circuit contactor is not damaged.
|
Corrective action |
Configure a circuit where frequent power ON/OFF is not repeated.
If the problem still persists after taking the above measure, contact your sales representative. |

Analog input fault
Operation panel indication |
E.AIE |
FR-LU08 indication |
Analog input fault |
Description |
The inverter output is shut off when a 30 mA or higher current or a 7.5 V or higher voltage is input to terminal 2 while the current input is selected by Pr.73 Analog input selection, or to terminal 4 while the current input is selected by Pr.267 Terminal 4 input selection. |
Check point |
Check the Pr.73, Pr.267, and the voltage/current input switch settings. |
Corrective action |
Either give a current less than 30 mA, or set Pr.73, Pr.267, and the voltage/current input switch to the voltage input and input a voltage. |

USB communication fault
Operation panel indication |
E.USB |
FR-LU08 indication |
USB comm error |
Description |
The inverter output is shut off when the communication is cut off for the time set in Pr.548 USB communication check time interval. |
Check point |
Check that the USB communication cable is connected securely. |
Corrective action |
- Check the Pr.548 setting.
- Connect the USB communication cable securely.
- Increase the Pr.548 setting or set "9999."
|

Safety circuit fault (Standard model / Ethernet model)
Operation panel indication |
E.SAF |
FR-LU08 indication |
safety circuit fault |
Description |
- The inverter output is shut off when a safety circuit fault occurs.
- The inverter output is shut off if the either of the wire between S1 and PC or S2 and PC becomes non-conductive while using the safety stop function.
- When the safety stop function is not used, the inverter output is shut off when the shorting wire between terminals S1 and PC or across S2 and PC is disconnected.
|
Check point |
- Check that the safety relay module or the connection has no fault when using the safety stop function.
- Check if the shorting wire between S1 and PC or between S2 and PC is disconnected when not using the safety stop function.
|
Corrective action |
- When using the safety stop function, check that the wiring of terminals S1, S2 and PC is correct and the safety stop input signal source such as a safety relay module is operating properly.
- When the safety stop function is not used, short across terminals S1 and PC and across S2 and PC with shorting wires.
|

Safety circuit fault (Safety communication model)
Operation panel indication |
E.SAF |
FR-LU08 indication |
safety circuit fault |
Description |
When a fault related to functional safety occurs, the inverter output is shut off by the protective function. For details, refer to the FR-E800-SCE Instruction Manual (Functional Safety). |

Overspeed occurrence
Operation panel indication |
E.OS |
FR-LU08 indication |
Overspeed occurrence |
Description |
The inverter output is shut off when the motor speed exceeds the Pr.374 Overspeed detection level under encoder feedback control, Real sensorless vector control, Vector control, and PM sensorless vector control. This protective function is not available in the initial status. |
Check point |
- Check that the Pr.374 setting is correct.
- Check that the setting of Pr.369 Number of encoder pulses does not differ from the actual number of encoder pulses. (Under encoder feedback control or Vector control)
|
Corrective action |
- Set the Pr.374 correctly.
- Set Pr.369 correctly. (Under encoder feedback control or Vector control)
|

Speed deviation excess detection
Operation panel indication |
E.OSD |
FR-LU08 indication |
Spd deviation fault |
Description |
When Pr.285 Speed deviation excess detection frequency is set during Vector control or PM sensorless vector control, the inverter output is shut off if the motor speed is increased or decreased by factors such as influence of the load and cannot be controlled in accordance with the speed command value. |
Check point |
- Check that the settings of Pr.285 and Pr.853 Speed deviation time are correct.
- Check for sudden load change.
- Check that the setting of Pr.369 Number of encoder pulses does not differ from the actual number of encoder pulses.
|
Corrective action |
- Set Pr.285 and Pr.853 correctly.
- Keep the load stable.
- Set Pr.369 correctly.
|

Signal loss detection
Operation panel indication |
E.ECT |
FR-LU08 indication |
Encoder signal loss |
Description |
The inverter output is shut off when the encoder signal is shut off under orientation control, encoder feedback control, or Vector control. This protective function is not available in the initial status. |
Check point |
- Check for the encoder signal loss.
- Check that the encoder specifications are correct.
- Check for a loose connector.
- Check that the switch setting of a Vector control compatible option is correct.
- Check that the power is supplied to the encoder. Alternatively, check that the power is not supplied to the encoder later than the inverter.
- Check that the voltage of the power supplied to the encoder is the same as the encoder output voltage.
|
Corrective action |
- Remedy the signal loss.
- Use an encoder that meets the specifications.
- Make connection securely.
- Make a switch setting of a Vector control compatible option correctly.
- Supply the power to the encoder. Or supply the power to the encoder at the same time when the power is supplied to the inverter.
If the power is supplied to the encoder after sent to the inverter, check that the encoder signal is properly sent and set "0 (initial value)" in Pr.376 Encoder signal loss detection enable/disable selection to disable signal loss detection.
- Make the voltage of the power supplied to the encoder the same as the encoder output voltage.
|

Excessive position fault
Operation panel indication |
E.OD [Vector] |
FR-LU08 indication |
Position fault |
Description |
The inverter output is shut off when the difference between the position command and position feedback exceeds Pr.427 Excessive level error during position control. This protective function is not available in the initial status. |
Check point |
- Check that the position detecting encoder mounting orientation matches the parameter.
- Check that the load is not large.
- Check that correct values are set in Pr.427 and Pr.369 Number of encoder pulses.
- When "11 or 12" is set in Pr.538 Current position retention selection, check that the power was not turned OFF or the inverter was not reset before completion of the position data writing to the EEPROM.
|
Corrective action |
- Check the parameters.
- Reduce the load.
- Set Pr.427 and Pr.369 correctly.
- While "11 or 12" is set in Pr.538, to turn OFF the power or reset the inverter after the output shutoff, wait at least one second.
|

Brake sequence fault
Operation panel indication |
E.MB1 to 7 |
FR-LU08 indication |
E.MB1 Fault to E.MB7 Fault |
Description |
The inverter output is shut off when a sequence error occurs during use of the brake sequence function (Pr.278 to Pr.283). This protective function is not available in the initial status. (The brake sequence function is invalid.) |
Check point |
Find the cause of the fault occurrence. |
Corrective action |
Check the set parameters and perform wiring properly. |

Acceleration error
Operation panel indication |
E.OA |
FR-LU08 indication |
Acceleration Error |
Description |
The acceleration error (E.OA) occurs and the inverter output is shut off when the acceleration rate of the motor rotation speed has exceeded the faulty acceleration rate detection level (Pr.375). This protective function is not available in the initial status. |
Check point |
- Check for sudden load change.
- Check that the Pr.375 Faulty acceleration rate detection level setting is correct.
- Check if the acceleration/deceleration rate setting is high.
|
Corrective action |
- Reduce the load.
- Set Pr.375 Faulty acceleration rate detection level correctly.
- If the acceleration/deceleration rate is great and an error occurs during normal operation, set Pr.375 to "9999 (no error detection)".
|

Abnormal internal temperature (IP67 model)
Operation panel indication |
E.IAH |
FR-LU08 indication |
Abnormal Intnl Temp |
Description |
The inverter output is shut off when the inverter internal temperature reaches the specified value or higher. |
Check point |
- Check for too high surrounding air temperature.
- Check if the cooling fan stops due to a fault.
|
Corrective action |
- Install an inverter suitable for the installation environment.
- Replace the cooling fan.
|

Ethernet communication fault
Operation panel indication |
E.EHR |
FR-LU08 indication |
Ethernet communication fault |
Description |
- Appears when Ethernet communication is interrupted by physical factors while Pr.1431 Ethernet signal loss detection function selection = "3" or Pr.1457 Extended setting for Ethernet signal loss detection function selection = "3".
- The inverter output is shut off if Ethernet communication is broken for the time set in Pr.1432 Ethernet communication check time interval or longer for all devices with IP addresses in the range specified for Ethernet command source selection (Pr.1449 to Pr.1454).
- Check that the Pr.1432 setting is not too short.
- When the CC-Link IE Field Network Basic is used, the inverter output is shut off in the following cases: the data addressed to the own station is not received for the predetermined timeout period or longer, or the status bit of the cyclic transmission addressed to the own station turns OFF (when the master inverter gives a command to stop the cyclic transmission). (For the details of the timeout period, status bit of the cyclic transmission, and command to stop the cyclic transmission, refer to the User's Manual of the master device which supports the CC-Link IE Field Network Basic.)
- When BACnet/IP is used, the inverter output will be shut off after the time period set in Pr.1432 after power is supplied to the inverter if an IP address of any other inverter falls within the Ethernet IP address range set for command source selection. (This protective function is available for the Ethernet model and the safety communication model.)
|
Check point |
- Check for a break in the Ethernet cable.
- Check that the Pr.1432 setting is not too short.
- Check for excessive noise around the inverter.
- When the CC-Link IE Field Network Basic is used, check that the timeout period set in the master is not shorter than the period during which the inverter does not receive the data addressed to the own station.
- When the CC-Link IE Field Network Basic is used, check that the status bit of the cyclic transmission addressed to the own station is not OFF.
- When BACnet/IP is used, check that IP addresses of other inverters are not included in the Ethernet IP address range set for command source selection.
|
Corrective action |
- Check that the Ethernet cable is connected to the Ethernet connector properly and the Ethernet cable is not damaged.
- Set a larger value in Pr.1432.
- When excessive noise occurs around the inverter, change the communication setting of the master. (The noise may be reduced by setting a shorter timeout period or increasing the number of retries in the communication setting of the master.)
- When the CC-Link IE Field Network Basic is used, set a timeout period longer than the period during which the inverter does not receive the data addressed to the own station. When the CC-Link IE Field Network Basic is used, turn ON the status bit of the cyclic transmission addressed to the own station.
- When BACnet/IP is used, do not include IP addresses of other inverters in the Ethernet IP address range set for command source selection.
|

Board combination fault
Operation panel indication |
E.CMB |
FR-LU08 indication |
Board combination fault |
Description |
Appears when the combination of the circuit board and the inverter is not appropriate or when the circuit board
is not connected to the inverter. |
Check point |
Check that the board is connected to the inverter properly. |
Corrective action |
- Connect the board to the inverter properly.
- Contact your sales representative.
|

PID signal fault
Operation panel indication |
E.PID |
FR-LU08 indication |
PID signal fault |
Description |
The inverter output is shut off if the measured value exceeds the PID upper limit or PID lower limit parameter setting, or the absolute deviation value exceeds the PID deviation parameter setting during PID control. Set this function in Pr.131 PID upper limit, Pr.132 PID lower limit, Pr.553 PID deviation limit and Pr.554 PID signal operation selection. This protective function is not available in the initial status. |
Check point |
- Check the meter for a failure or break.
- Check that the parameter settings are correct.
|
Corrective action |
- Check that the meter has no failure or break.
- Set the parameters correctly.
|

Option fault
Operation panel indication |
E.1 |
FR-LU08 indication |
Fault 1 |
Description |
- The inverter output is shut off when a contact failure occurs between the inverter and the plug-in option.
- Appears when the switch for manufacturer setting of the plug-in option is changed.
|
Check point |
- Check that the plug-in option is plugged into the connector securely.
- Check for excessive noise around the inverter.
|
Corrective action |
- Connect the plug-in option securely.
- Take measures against noises if there are devices producing excessive electrical noises around the inverter. If the problem still persists after taking the above measure, contact your sales representative.
- Set the switch on the plug-in option, which is for manufacturer setting, back to the initial setting.
|

Inverter output fault
Operation panel indication |
E.10 |
FR-LU08 indication |
Fault 10 |
Description |
The inverter output is shut off if the inverter detects an output current fault such as an earth (ground) fault that occurred on the inverter's output side (load side). |
Check point |
Check for an earth (ground) fault in the motor and connection cable. |
Corrective action |
Remedy the earth (ground) fault or other fault. |

Opposite rotation deceleration fault
Operation panel indication |
E.11
[Sensorless] |
FR-LU08 indication |
Opst rot dtct fault |
Description |
The speed may not decelerate during low speed operation if the rotation direction of the speed command and the estimated speed differ when the rotation is changing from forward to reverse or from reverse to forward during torque control under Real sensorless vector control. The inverter output is shut off when overload occurs due to the un-switched rotation direction. This protective function is not available in the initial status (V/F control). (This function is only available under Real sensorless vector control.) |
Check point |
Check that the rotation direction is not switched from forward to reverse rotation (or from reverse to forward) during torque control under Real sensorless vector control. |
Corrective action |
- Prevent the motor from switching the rotation direction from forward to reverse (or from reverse to forward) during torque control under Real sensorless vector control.
- Contact your sales representative.
|

Internal circuit fault
Operation panel indication |
E.13 |
FR-LU08 indication |
Intrnl circuit fault |
Description |
Appears when the internal circuit is faulty. |
Check point |
-------------- |
Corrective action |
Contact your sales representative. |

No fault history
Operation panel indication |
E.0 |
FR-LU08 indication |
No faults |
Description |
Appears when no fault records are stored. (Appears when the fault history is cleared after the protective function has been activated.) |

24 V external power supply operation
Operation panel indication |
EV |
FR-LU08 indication |
--------- |
Description |
Blinks when the main circuit power supply is OFF and the 24 V external power supply is being input in either of the following conditions:
- When the FR-E8DS is installed
- IP67 model-E800 Instruction Manual (Function)
|
Check point |
Power is supplied from a 24 V external power supply. |
Corrective action |
- Turning ON the power supply (main circuit) of the inverter clears the indication.
- If the indication is still displayed after turning ON of the power supply (main circuit) of the inverter, the power supply voltage may be low, or the jumper between terminals P/+ and P1 may be disconnected.
|

Backup in progress
Operation panel indication |
RD |
FR-LU08 indication |
Rd |
Description |
Backup operation is in progress to back up inverter parameters and the data used in the PLC function to a computer. |

Restoration in progress
Operation panel indication |
WR |
FR-LU08 indication |
WR |
Description |
Restore operation is in progress to restore the backup data stored in the computer in the inverter. |
