SolutionsTotal Maintenance
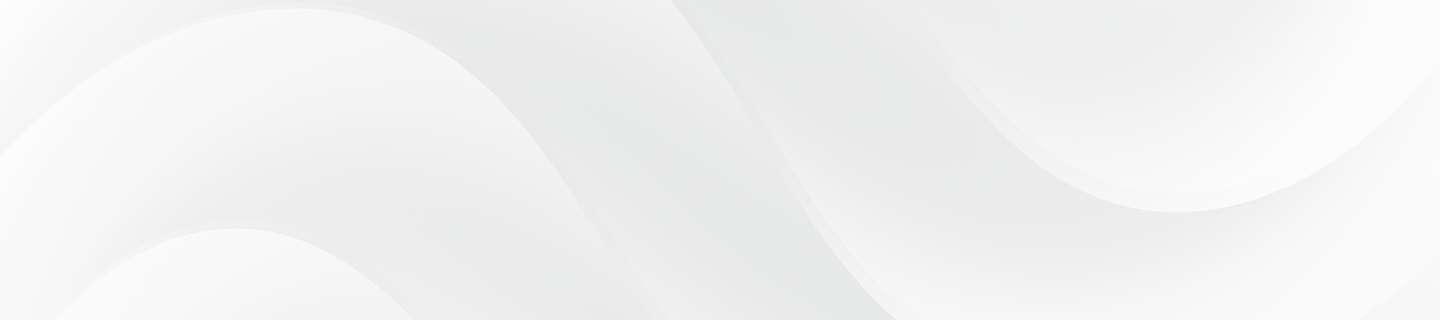
In today’s dramatically changing business environment, the impact of sudden equipment downtime on corporate profits is enormous, and an increasing number of businesses are implementing planned equipment maintenance with the aim of achieving non-stop factories.
Meanwhile, the manufacturing industry faces another major issue of passing down the expertise of highly experienced employees.
Case01Preventing defect outflow by understanding the tendency of molding defects
Predictive
Maintenance
Device level
The tendency of defects to appear in resin molding isn’t well understood, leading to loss costs as the occurrence of continuous defects goes unnoticed.
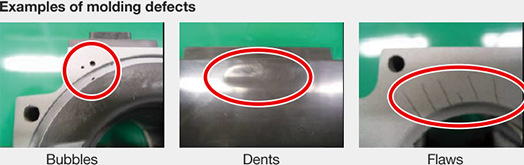
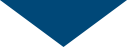
Analyze and diagnose feature quantities to prevent plastic molding machine defects
from continuously occurring
Using the data collected with MELIPC industrial-use PC in the MELSOFT MaiLab (data analysis software), feature quantities from parameter waveform data that may affect molding quality are selected, the association with defects is analyzed, and diagnostic rules are created. By collecting molding machine data in real time with MELIPC and diagnosing it based on rules using MELSOFT MaiLab, signs of molding defects are identified and maintenance can be performed before multiple defects occur.
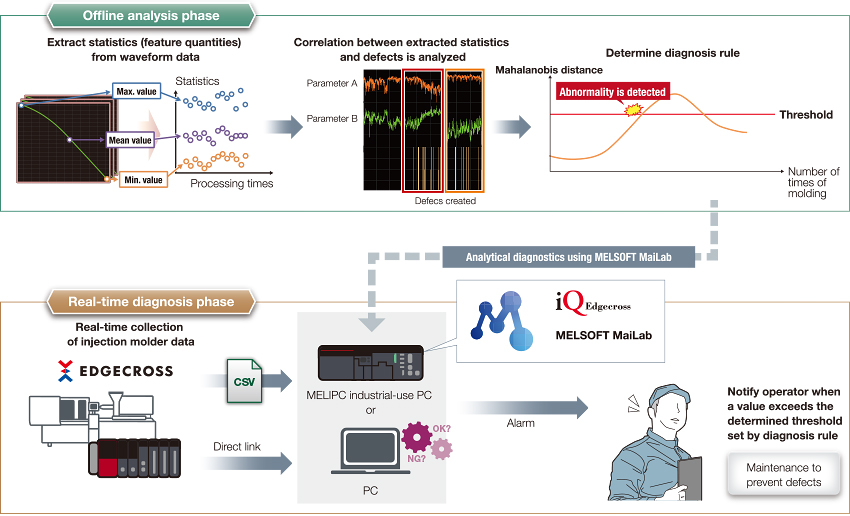
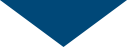
The costs of losses due to waste is reduced by detecting signs of molding defects.