SolutionsTotal Maintenance
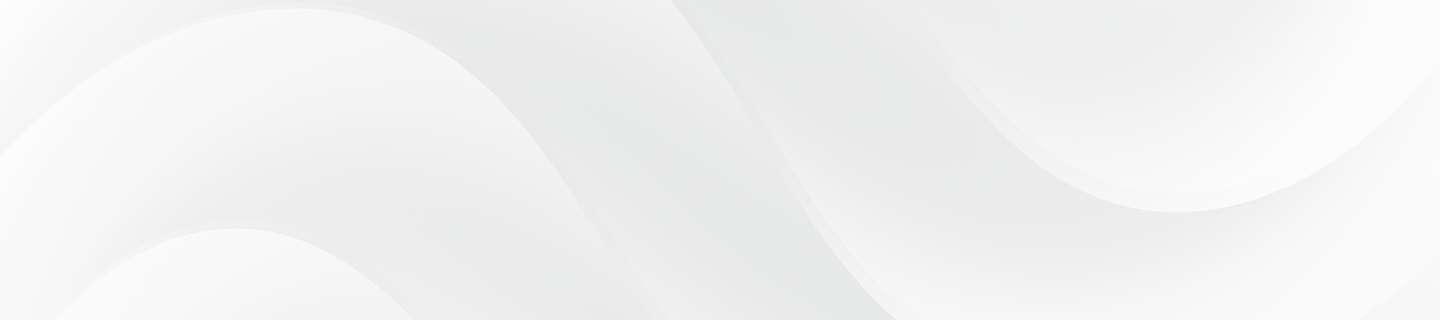
In today’s dramatically changing business environment, the impact of sudden equipment downtime on corporate profits is enormous, and an increasing number of businesses are implementing planned equipment maintenance with the aim of achieving non-stop factories.
Meanwhile, the manufacturing industry faces another major issue of passing down the expertise of highly experienced employees.
Case03Performing maintenance work on cylinders at the right time
Predictive
Maintenance
Device level
Delayed operation of the cylinder isn't noticed by operators, which leads to increased equipment cycle time.
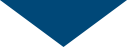
Optimize maintenance by monitoring the cylinder operating time
The Cylinder and Cycle Time Monitor function of the e-F@ctory Starter Package measures and visualizes the cylinder operation time, automatically detects delays in the operating time caused by various factors (e.g., sticking due to dirt), and sounds an alarm.
This facilitates timely maintenance work without the need to rely on operator intuition and experience.
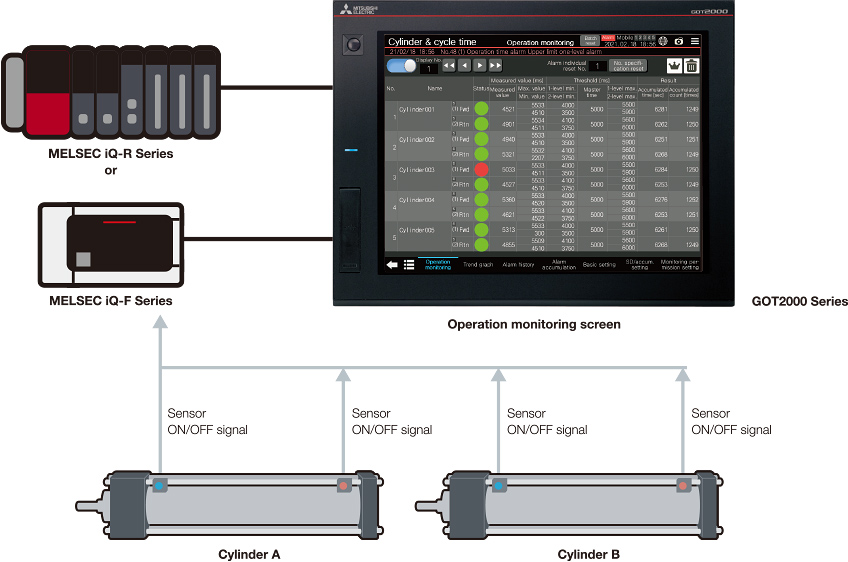
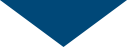
Prevents deterioration of the performance operating ratio and keeps production within the set tact time.