SolutionsTotal Maintenance
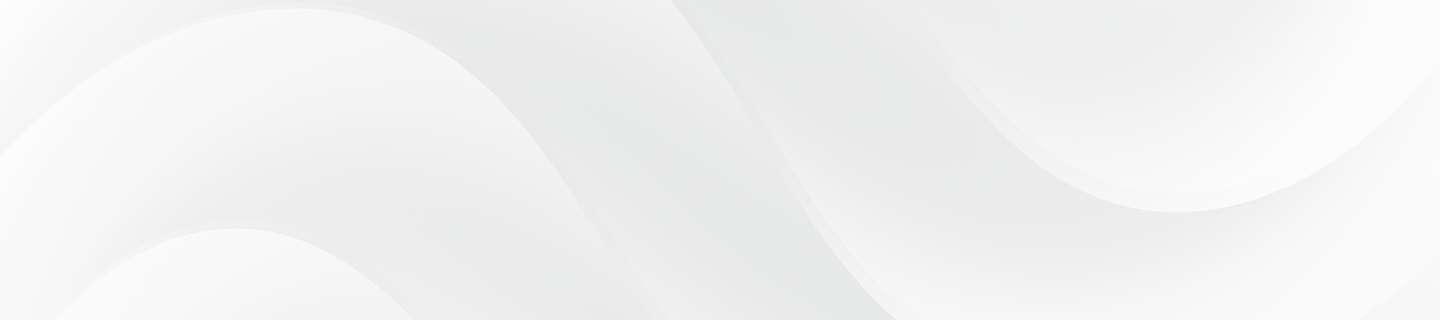
In today’s dramatically changing business environment, the impact of sudden equipment downtime on corporate profits is enormous, and an increasing number of businesses are implementing planned equipment maintenance with the aim of achieving non-stop factories.
Meanwhile, the manufacturing industry faces another major issue of passing down the expertise of highly experienced employees.
Case08Understanding when to replace servo amplifiers
Preventive
Maintenance
Device level
The sudden failure of servo amplifiers causes unexpected downtime.
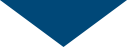
Use the service life diagnosis for servo systems
Using the GOT Servo Amplifier Life Diagnosis function, it is possible to check the accumulated energization time of smoothing capacitors and the number of times the inrush relay has been turned on and off, therefore helping users understand when servo amplifiers need to replaced.
There are also functions for inverters and robots*1 to check when maintenance parts should be replaced.
Please refer to the GOT2000 Series Product and Solution Introduction (P. 32) for more information.
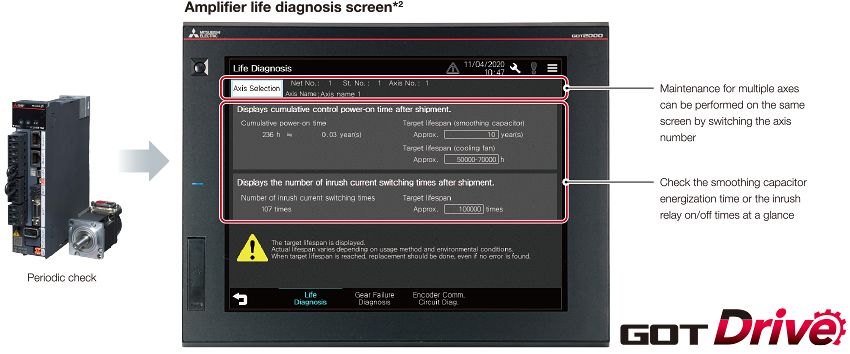
*1 The degree of wear for each part is a reference value calculated from the operation status of the robot and is used for supporting the maintenance and inspection plan. It does not guarantee service life.
*2 Ready to use sample screens (VGA) are included in GT Works3. For the details, please contact your local sales office.
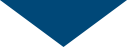
Planned maintenance is made possible by understanding the repair and replacement timing of servo amplifiers in advance