Journals
2024.07.08
Human connections enhance productivity and quality improvements achieved through engineering
- #Focus
- #Asia-Oceania
- #Sustainability
- #Interview
- #Bangkok Thailand
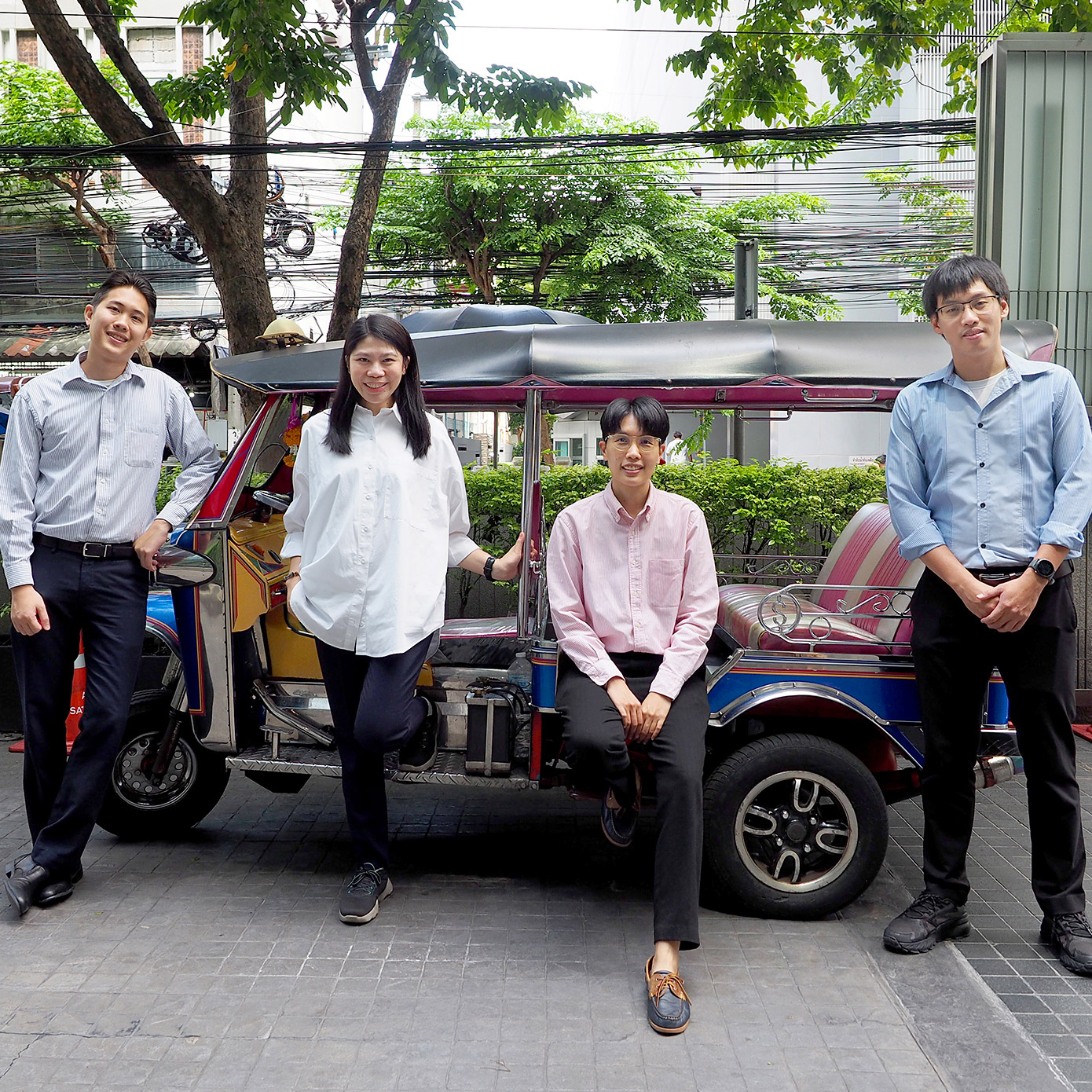
- Home
- Our Stories
- Article list
- Human connections enhance productivity and quality improvements achieved through engineering
Mitsubishi Electric has bases and affiliates around the world. Mitsubishi Electric Asia (Thailand) Co., Ltd., commonly known as ME-TH, is one of these, located in Bangkok, Thailand. Thailand is also home to six Mitsubishi Electric Group manufacturing companies that supply a wide range of products globally, making it an important country for the Group. Within ME-TH, the Manufacturing Engineering Division provides highly specialized knowledge and technology to Mitsubishi Electric Group factories improve productivity and product quality. This article introduces the activities and priorities of the ME-TH Manufacturing Engineering Division through interviews with four division members.
Contents
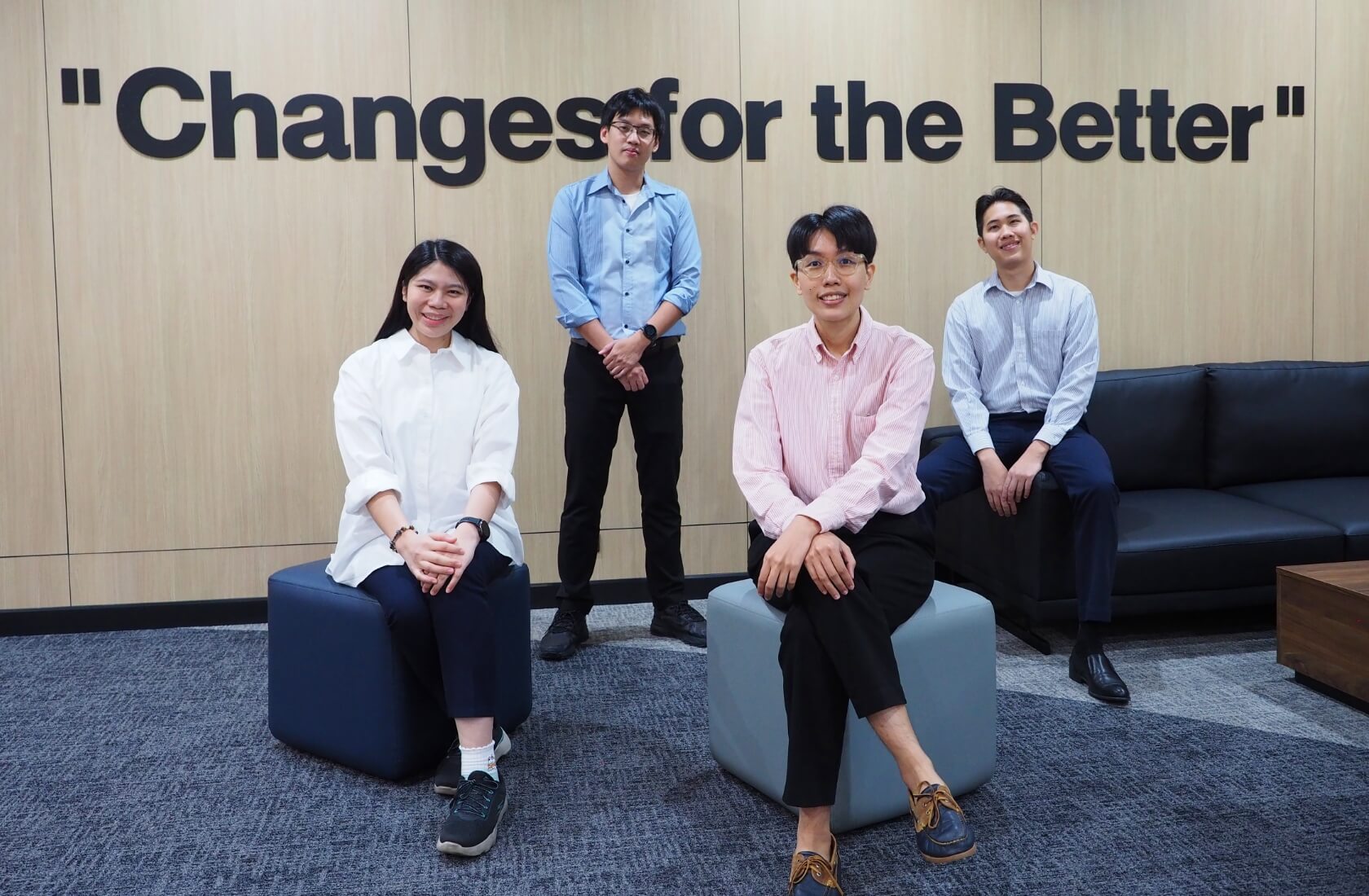
Ms. Mussalin Sirikwanwiwat ("Fai") Assistant Manager, Manufacturing Engineering Division
Mr. Kittipong Torsakulrath ("Pop") Assistant Manager, Manufacturing Engineering Division
Ms. Sansanee Thiangkhamdee ("Nam") Assistant Manager, Manufacturing Engineering Division
Mr. Anan Ritrudee ("Anan") Senior Engineer, Manufacturing Engineering Division
The Manufacturing Engineering Division: Experts in improving manufacturing
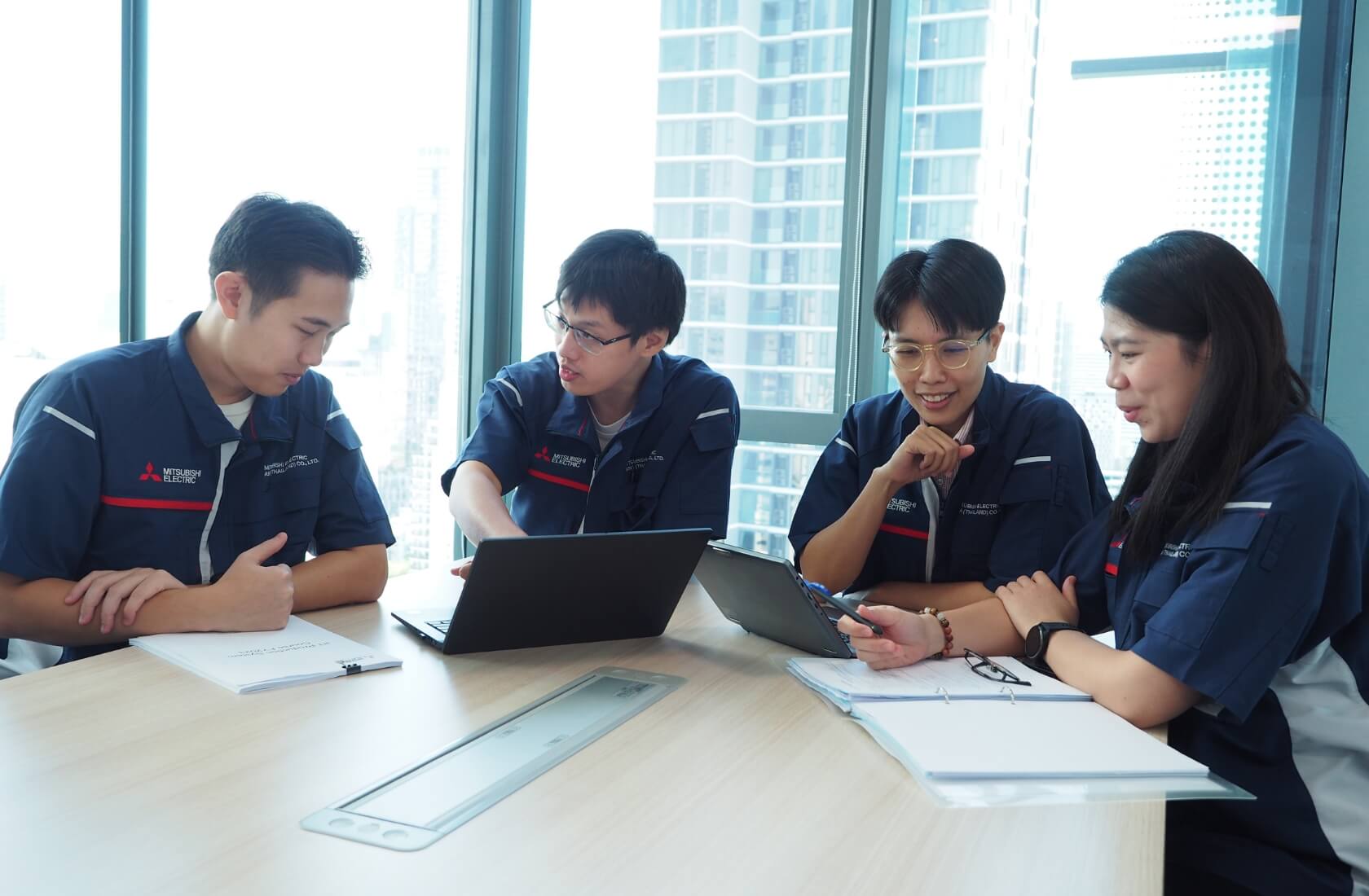
- What is the mission and role of the Manufacturing Engineering Division at ME-TH?
Fai: First of all, ME-TH itself doesn’t have a factory. Our Manufacturing Engineering Division visits manufacturing sites outside ME-TH to support productivity and quality improvement in manufacturing. We aim to create new value by adding our technology and know-how to the strengths of each manufacturing site. What is essential in manufacturing is for anyone to be able to produce products of the same quality at any time. To achieve this, we have to understand each situation in detail so that the relevant factors can be controlled. For example, it’s important to involve the whole team, not just one person, in understanding process control and making appropriate jigs.
- What are the challenges of collaborating with so many different manufacturing companies, each with their own characteristics?
Pop: The hardest part of providing support is getting everyone involved to understand things the same way. Our approach is to go to a manufacturing site first, look at parts or drawings, and then hold a meeting with representatives from each department to establish agreement. By listening to different opinions and ideas at that stage, we aim to create a common understanding and awareness among all concerned.
- What is the office atmosphere like at ME-TH?
Fai: The ME-TH office has a warm atmosphere, so we all feel close to each other and can talk to each other quickly if we need anything, whether it’s work-related or a private matter. From serious meetings to small talk with constant laughter, it’s an environment where we can discuss things easily.
Nam: ME-TH is like my family. We’re all comfortable talking to each other. After work, we even go out for dinner together—the whole company, that is, not only our division.
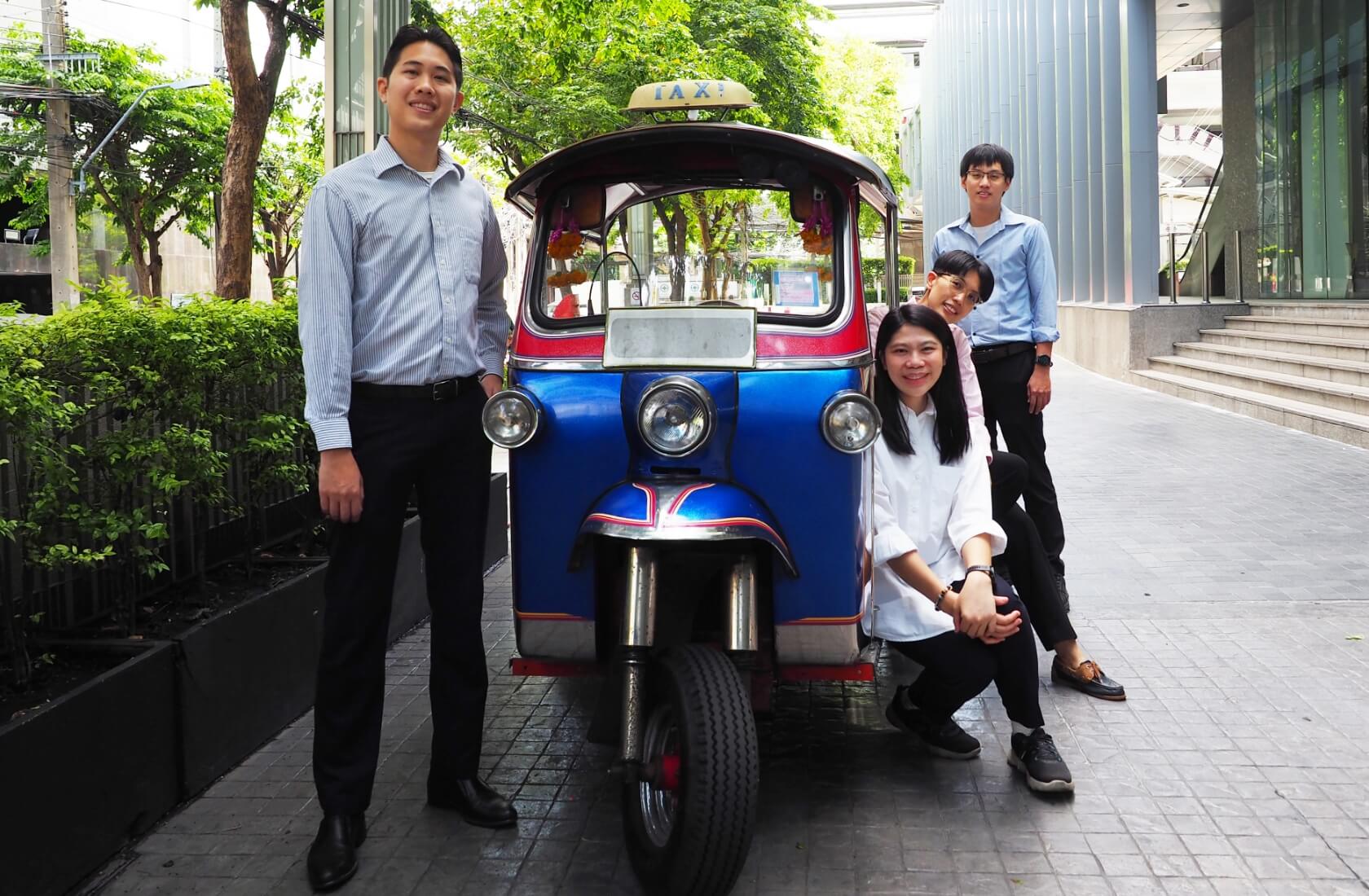
Pop: There are frequent opportunities to converse and exchange information with Japanese people working at ME-TH. During work hours, it’s useful and efficient to consult about work. Outside of work, social interactions are also common. We also interact with engineers in Japan, which helps us broaden our horizons.
Anan: Everyone in the office is friendly, so we all know each other well. We come from different departments and are at different ages, which allows for exchanging perspectives in various dimensions and applying new ideas both at work and in private life.
How do you identify challenges on production sites?
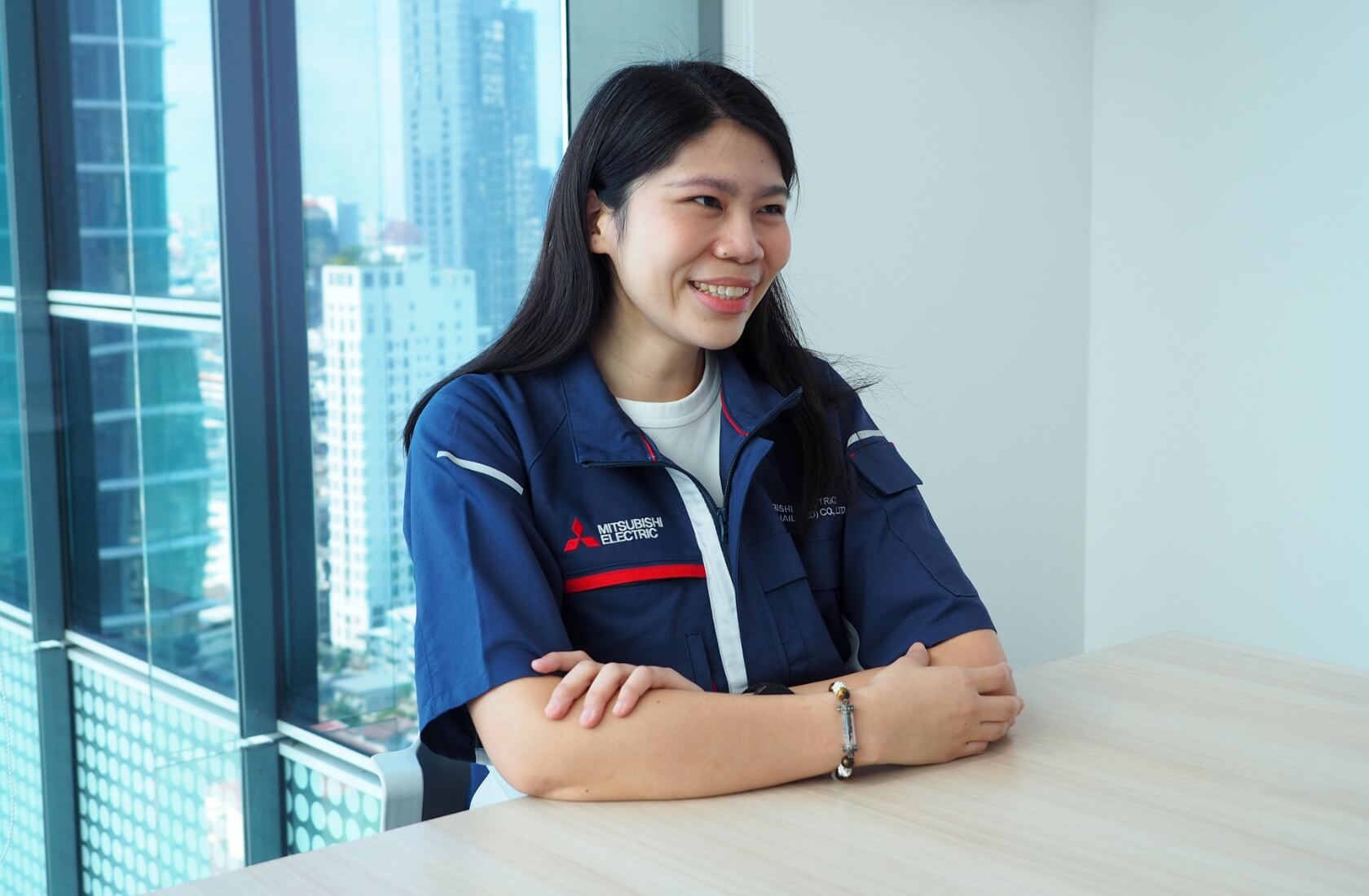
- Next, let's talk about your areas of specialization. Fai and Nam are both Just In Time (JIT) specialists—what does this involve?
Fai: JIT aims to "supply what is needed, in as much quantity as needed, when needed" in production with a lean and efficient production management system. To do this, we need to collect data first. The Manufacturing Engineering Division arrives at factories and other sites as outsiders unfamiliar with the local circumstances, and this is actually an advantage. We notice issues and abnormalities that people working at the site every day have grown accustomed to and see as normal. The first thing we do when we enter a site is to repeatedly question the people who work there about why defects and abnormalities occur. This helps us identify problems and areas where improvement is needed.
- Is it true that Mitsubishi Electric has a unique approach to JIT?
Fai: Every company knows how effective Kaizen is as an improvement method, but most companies apply it primarily to direct processes. The Mitsubishi Electric Group is also focused on indirect processes. We are always aiming for better results and continuous improvement. The concept "Kaizen culture well established in all worksites, including sales, procurement, manufacturing, shipping, and service" is our group’s strength. JIT Kaizen Activities should be promoted and pursued by all employees in all departments, both direct (manufacturing) and indirect (non-manufacturing).
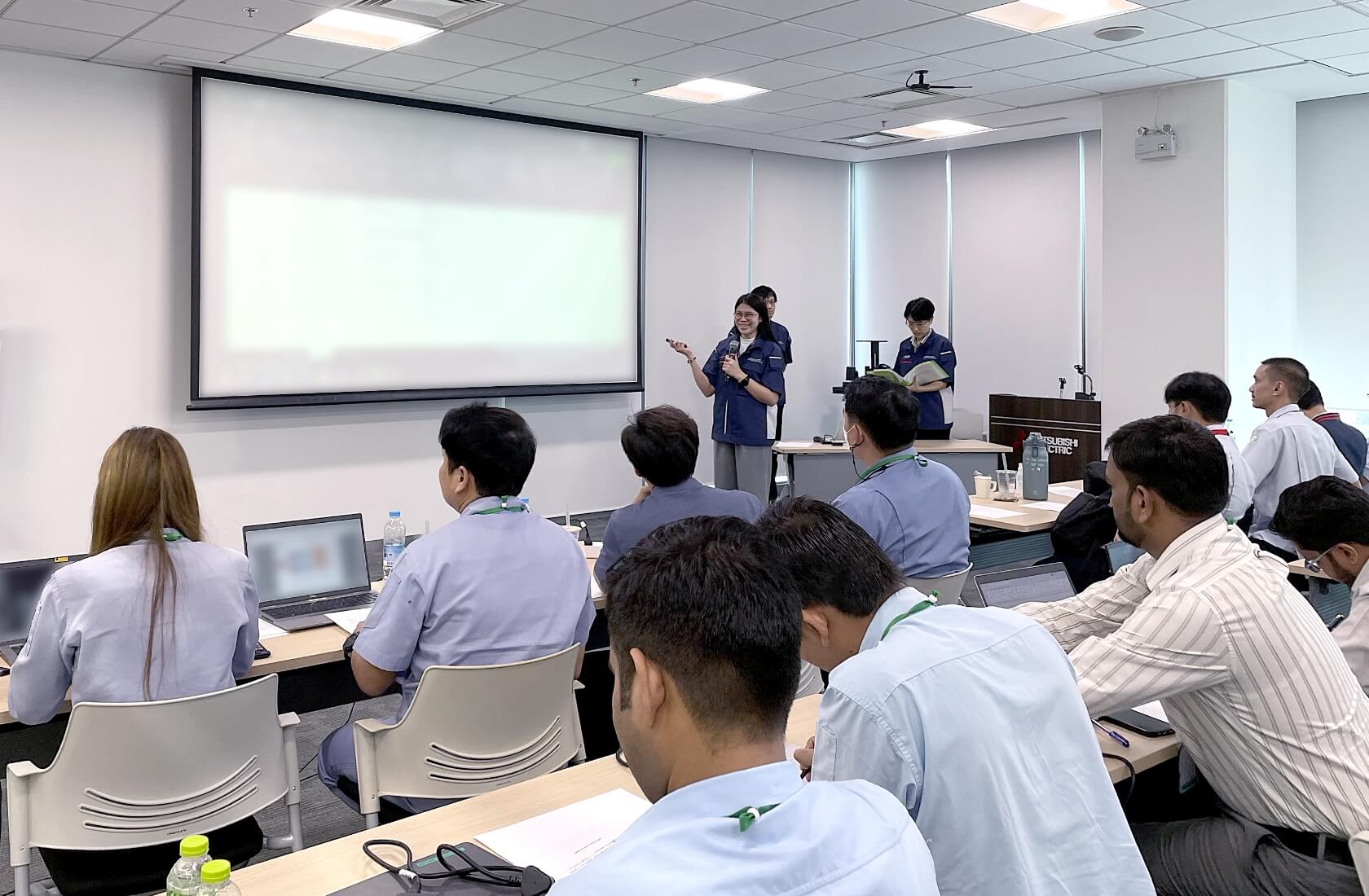
- How do you promote and share this approach to JIT?
Fai: Utilizing JIT skills learned in Japan, we hold JIT seminars as instructors for employees and suppliers in various departments at each manufacturing company. There are differences between Japan and Thailand, and the situation differs from factory to factory, so we cannot apply the exact methods we have studied, but one of our objectives is to change the mindset of our employees. What we hear from participants through seminars helps us understand the current situation at that factory. This in turn helps us research the factory’s needs and the areas currently requiring special focus so that we can extract key challenges.
From JIT to site-based self-development
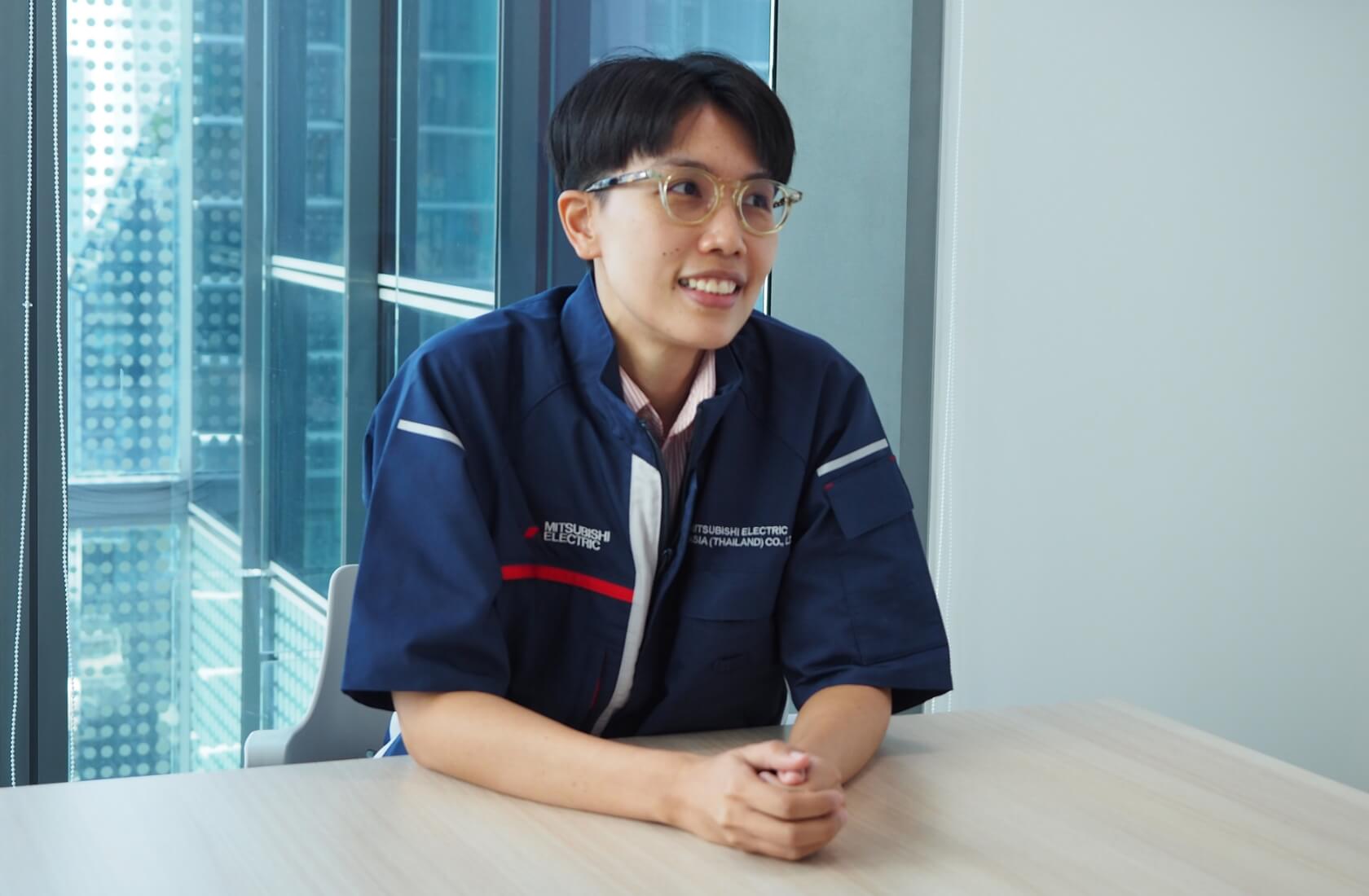
- Nam, what kind of JIT projects do you work on?
Nam: I’m working on JIT that involves logistics companies as well as manufacturing companies. Global logistics play an important role in JIT production. For example, each manufacturing company uses its own warehouse, but the volume of products shipped by each site varies depending on the peak and low season. We think it would be more efficient to consolidate the warehouses at each site and deliver from there. We aim to complete this logistics improvement project by 2025, and we expect it to make warehouse management easier and reduce the number of delivery trucks needed, thereby reducing costs—including warehouse rental fees—and environmental impact.
- You work with everyone from manufacturing companies to logistics companies. What are the advantages and difficulties of this approach?
Nam: The advantage is that each company can share its knowledge. If something goes wrong, the companies involved can come together to brainstorm and come up with a solution together. The difficulty, on the other hand, is achieving consensus. For example, the project I am working on involves 13 affiliated companies. When an issue arises, differing viewpoints and priorities can hinder the process of drawing a single conclusion about how to proceed.
- What do you see as the key to resolving this challenge?
Nam: Sharing end goals. For example, one of the common end goals of these 13 companies is to improve logistics efficiency. That’s what we do consistently, and drawing on the wisdom of each professional, we discuss how to make it work so that all 13 companies can reach their goals. Of course, new projects and activities are always challenging. Progress is slow at first, but eventually we reach our goal. It’s an exciting experience. But achieving these goals is not easy. There are many factors to consider, including the human factor. Many times, people don’t agree with our initial ideas, so we have to discuss things together to find the best and most appropriate solution. Sometimes we come up with a method together that seems optimal, but proves inadequate when we run the experiment. We must put in as much effort as possible to achieve the goals we set.
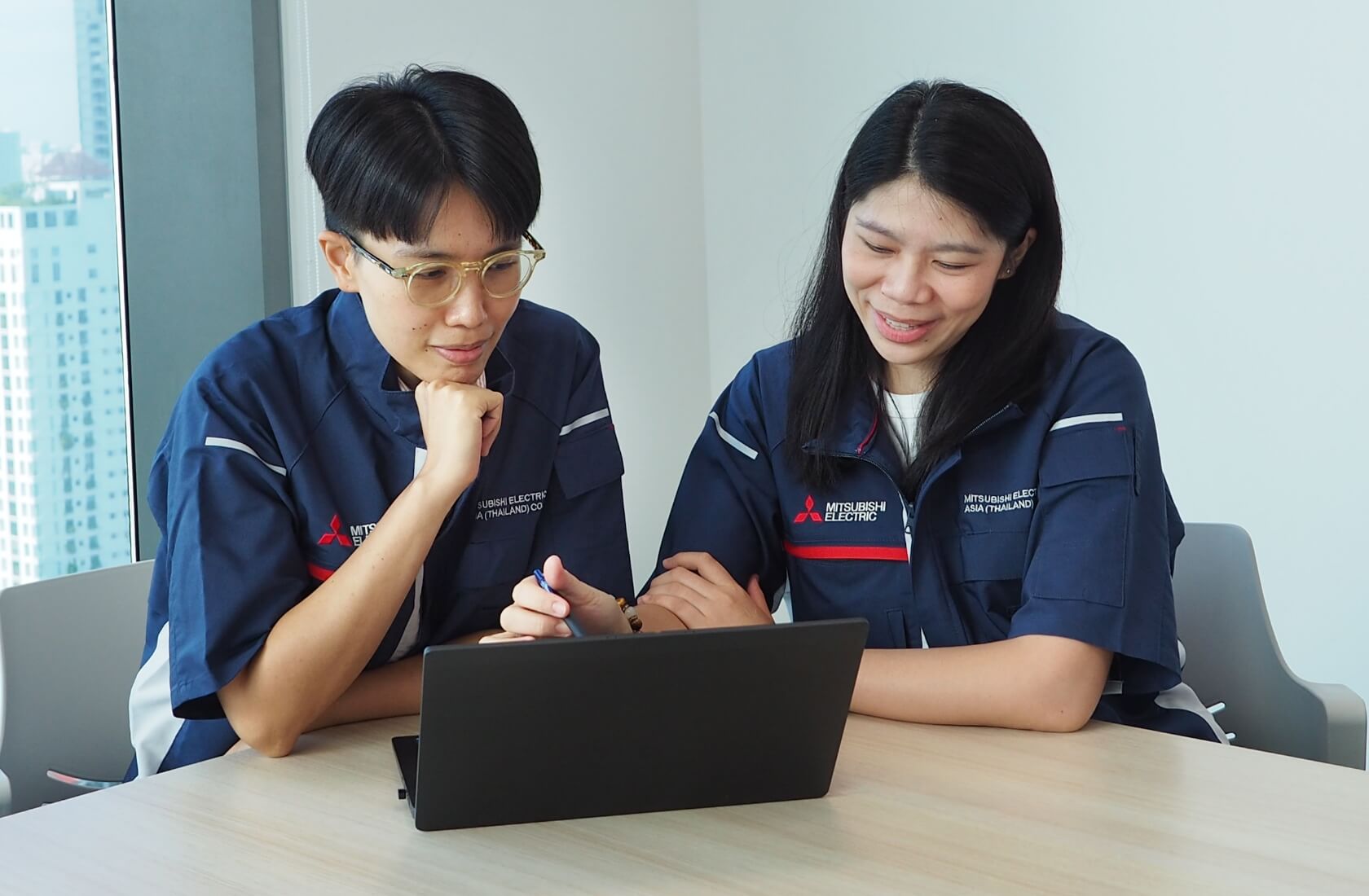
- Why does the Manufacturing Engineering Division place importance on "self-training of manufacturing companies"?
Fai: Each manufacturing site faces a variety of challenges. Of course, we can offer support, but if they can autonomously become aware of the problem and gather and analyze information, they will be able to solve issues in other areas. This makes it important for sites to nurture themselves. In addition, when we enter a site for the first time, we receive support such as explanations from the people there and exchange ideas with each other to resolve any problems. That way, we can learn from each other.
- Do you feel that you are contributing to raising the level of Thai manufacturing through your work?
Fai: Yes. We are in a position to teach at seminars, and we are in a position to be taught from the field. By continuing the cycle of passing on the knowledge acquired there to other sites, we believe that the productivity of each manufacturing site will improve, ultimately leading to a level-up in Thai manufacturing.
Two vital elements: Visualization through data, and sharing
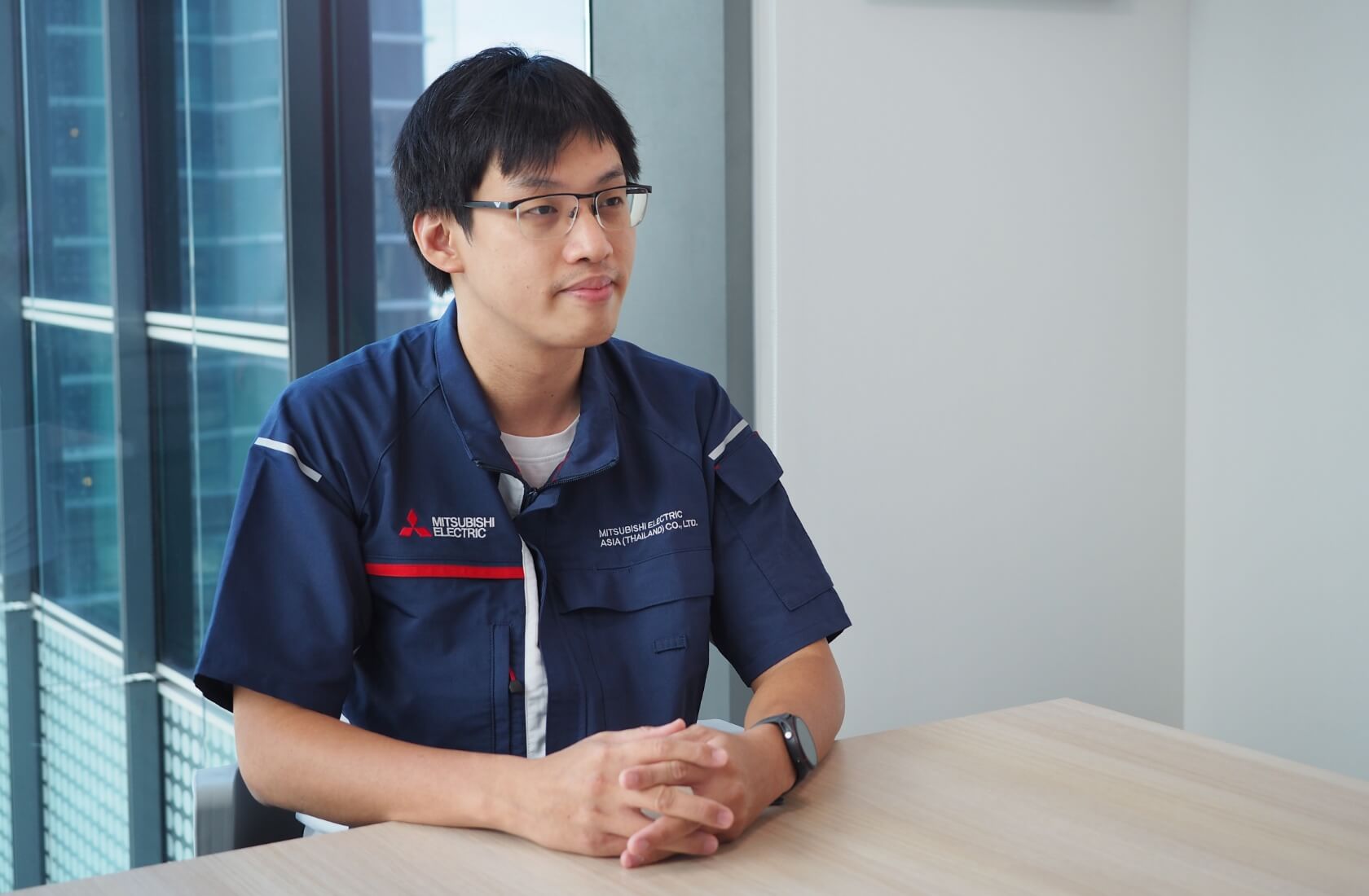
- Next I’d like to dive into Pop and Anan’s efforts. Let me start with a general question. Why does ME-TH emphasize the concept "Scientific support, not personal experience"?
Pop: To improve the productivity of each site, which is the objective of the Manufacturing Engineering Division, we must first understand process and equipment accurately. In order to do this, we use collected data, quantitative and qualitative, to determine whether there is a problem in the production process. If there is a problem, we solve it. Of course, we don't neglect people’s experiences. The experience of a skilled technician is also important, but the ideal is for anyone to be able to make products of the same quality. For this reason, "Data = facts" is indispensable at the manufacturing site.
- Can you give me an example?
Pop: Let me tell you about a project I’m working on to improve the cooling control process in plastic molding. In plastic injection molding, there is a process called cooling, and we aim to improve quality and reduce energy consumption by optimizing the process to control the cooling rate. The first step in the improvement project was to examine the data from the process. Because this process is not fully visible, we had to infer some aspects from related data to understand it more fully. The results showed that the process controlling the cooling rate is longer than the reference time. We are operating more facilities and using more energy than necessary.
- What steps have you taken to improve this?
Pop: The first improvement in the cooling rate control facility is making water flow smoothly by adjusting the cooling channels. The second is to measure temperature more accurately by improving the location of temperature sensors. We are working toward the realization of an efficient and appropriate cooling control process. This project will contribute to sustainability by reducing energy load and improve productivity by reducing energy costs. Reducing CO2 emissions at manufacturing sites is an important issue, and if this is achieved, it will have a huge impact both internally and externally.
Better communication is important for better manufacturing
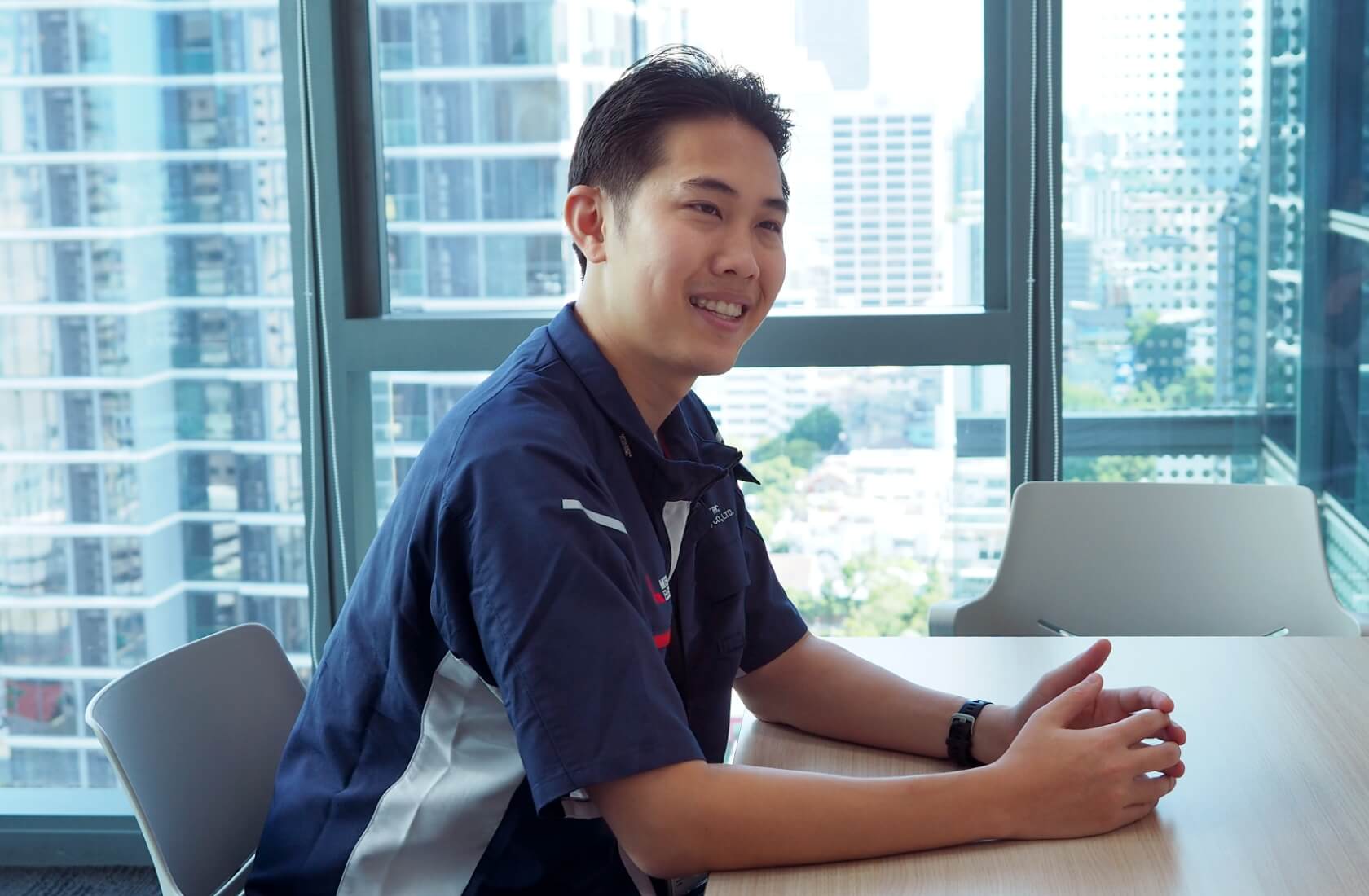
*PCBA: A printed circuit board assembly (PCBA) is a printed circuit board (PCB) with all the necessary components added—a finished component ready for use in electronic devices.
- Anan, can you tell us about the project you are working on improving the soldering process for PCBA?
Anan: At a factory, there is a high defect rate in the flow soldering process for PCBA. I collaborate with factory engineers to improve the process. This includes both taking action like evaluating results and countermeasures to eliminate direct causes, and consulting on machine condition and working manual standardization.
- Are any points that you struggle with or focus on?
Anan: The difficulty is that production is hard to stop. We would like to trial various improvements, but we can only run experiments during lunch breaks. Also, evaluation methods should measure the actual production result in terms of defect occurrence. That is why we must be careful changing process conditions. If we see too many defects, we have to return to the previous conditions and reconsider our approach.
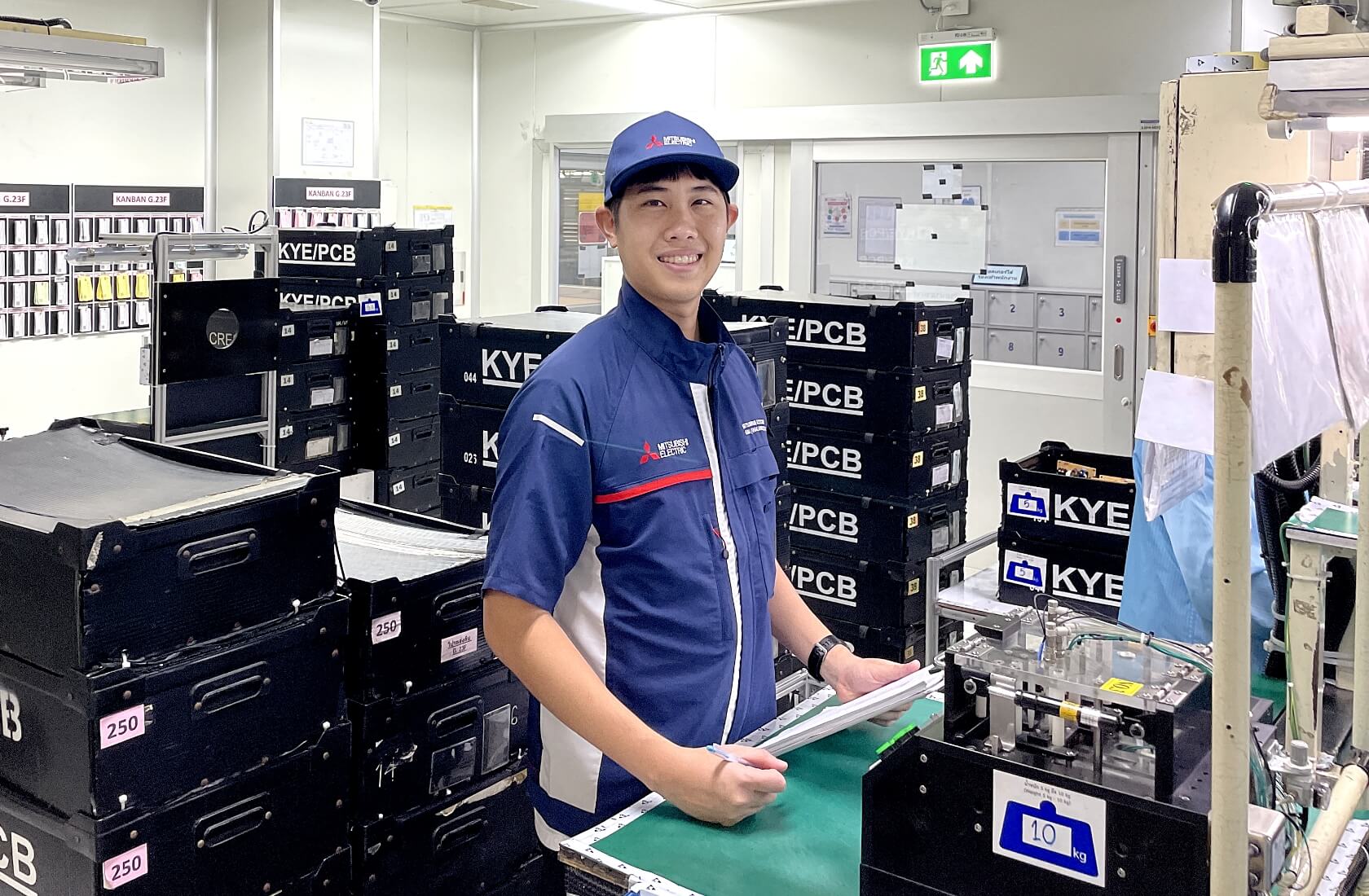
- What do you value when working on your projects?
Anan: Relationships are very important for productivity. Good relationships make people talk more deeply. For example, when holding the PCBA Experts Conference, participants sometimes have dinner together to further deepen relationships across company boundaries. These are bonding activities that make participants feel more comfortable asking and answering questions about improvement activities for PCBA processes.
- Finally, what are the future prospects and plans for the ME-TH Manufacturing Engineering Division?
Anan: Speaking on behalf of the team, I would like to promote our capabilities to affiliated companies here and overseas. Especially in Thailand, there are some affiliated employees who do not know we are ready and able to support them and solve the problems they face.
*The information on this page is current as of April, 2024.
Written by Our Stories Editing Team